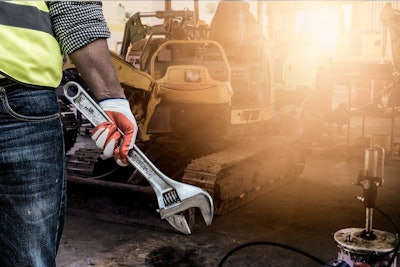
Shortages of trained and qualified diesel technicians have hampered the heavy equipment industry for decades. One solution: Branch Civil, a heavy/highway firm headquartered in Roanoke, Virginia, is developing its own techs.
In coordination with Virginia’s Department of Labor and Industries, Branch Civil launched a four-year apprenticeship program in June 2021.
Natalie Kerschner, equipment operations data analyst for the company, oversees the program. It requires apprentices to complete 144 hours a year of classroom and self-guided online study, and 2,000 hours of hands-on, paid work per year for four years. The self-study is a mixture of online Cat and Deere training and Branch Civil’s own curriculum, Kerschner says. Apprentices also attend a 16-week welding program from Virginia Western Community College to earn a welder’s certificate.
Enthusiastic buy-in
Kerschner worked closely with Tim Morgan, Branch Civil’s equipment manager, to detail what they needed to create fully trained, journeyman equipment technicians. “It took us about six months to put together the program,” she says. “And we had to get buy-in from the people above us, but they were pretty enthusiastic about it. Our sister company, Hopkins Lacy, has had a thriving apprenticeship program for over 25 years now. So, they were a good model to look to.”
The Virginia Department of Labor and Industry has multiple classifications of apprenticeship programs. “We applied for the Heavy Equipment Technician program,” says Kerschner. “They have to look through our plan and make sure it's comprehensive and meets their standards. But we got to develop a lot of our own program.”
The Cat and Deere online curriculum consists of self-guided lessons and tests. Apprentices have to score at least 80 percent on these tests. But they can retake them too. Their progress is tracked in Branch Civil’s learning management systems run by the company’s human relations department. Branch Civil also provides the students with education on maintaining small equipment like concrete saws, chainsaws and handheld compactors.
Retaining the trained
A concern many contractors have with training apprentices is that their students will leave at the end of the training program when they receive their journeyman’s card. “We ask that they work with us for at least two years beyond the end of their training,” says Kerschner. “They sign a contract, saying that they will do that, or if they leave, they are responsible for paying back the cost of their training — not the cost of their labor — just the classes and training that we put them into. The costs are minimal, so it's not a huge burden.”
“You have to take that risk,” says Morgan. “It’s like the old saying, ‘what’s the cost of training?’ Well, what’s the cost of not training?” Looking at it altruistically, even if the apprentice does not stay with the company after his or her four years are up, at least the program is helping to fill the industry pipeline of up-and-coming technicians, he says.
Train the trainers
Currently, there are two apprentices in Branch Civil’s program, and for now, that’s the number they prefer.
“Each apprentice has a designated mentor who works with them on a one-to-one basis,” says Kerschner. The company hopes to hire more experienced mechanics who can serve as mentors, and we also provide training on how to mentor apprentices. This train-the-trainer type program teaches the mentors how to be good leaders and help the apprentices grow, she says.
Hands-on advantages
Compared to a more formal program where student apprentices spend a lot of time in a community college classroom, Branch Civil’s on-the-job training and one-to-one relationship with mentors have distinct advantages, says Kerschner.
“A lot of people do really well learning as they go. With hands-on training, they have people other than their mentor available to help them as well,” Kerschner says. “And over the four years, they learn exactly what they're getting into because it's also the place where we hope they'll want to continue working. They already are part of the team and know what it's like to work for us, and they don't need to find an employer after finishing.”
State requirements
While the bulk of the apprentices’ time is spent working for Branch Civil, the state of Virginia still has a vested interest in making sure the apprenticeship program offers everything the students need.
“You submit your work process to them, which is the hourly breakdown of how much time they're going to spend on each component of the training," says Kerschner. “They have an education expert who reviews this and your education plan. They will also review the resumes of the people doing the training and the applications for each apprentice.”
A facility inspection is also required. “They want to make sure it's a good facility for training and that the apprentices will have access to the technology they need,” she says. After that, it’s just a matter of submitting an annual progress report and a reinspection every three years. Once the apprentice completes the program, the state will issue them a journeyman’s card that is transferable to other states.
Kerschner also says companies considering their own apprenticeship programs should consider education grants to defer some of the costs. “Sometimes it depends on what demographics you're hiring. They have different requirements, but it's worth looking into to see if you qualify for any grants.”