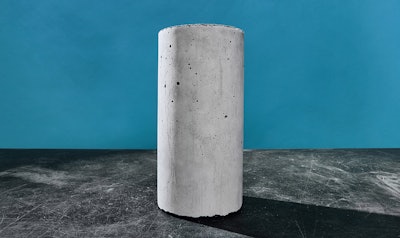
A low-emission cement startup born out of MIT has big plans to expand its production capacity and begin working with state transportation departments across the country.
Sublime Systems, based in Somerville, Massachusetts, manufactures Sublime Cement, a low-carbon alternative to Portland cement created through an electrified process.
The company was co-founded by former MIT postdoctoral fellow and its current CEO Leah Ellis, PhD., in March 2020. The company has around 90 full-time employees, around 30 of which are devoted strictly to research and development.
Sublime Cement can be used in any application suited for Portland cement, including commercial buildings, civil infrastructure, roads and sidewalks, the company says. Current demand, says Greg Williams, vice president of product, is coming from hyper-scaler data centers.
“They use a ton of concrete as well as other building materials,” he says. “A lot of them have internal Scope 3 emissions targets and very aggressive targets for decarbonizing their supply chains. And so, they're willing to and excited to work with companies like Sublime.
“We're at the early stages. They're willing to pay a bit of a scaling premium to help us come down that cost curve and get to mass scale.”
Some of Sublime Systems’ recent accomplishments include pouring product as part of the first net-zero building in Boston and securing a $75 million investment and equity agreements from cement producers Holcim and CRH.
Sublime Systems also recently established a new distribution channel partner program, through which general contractors will form “Sublime Deployment Ready” teams to shape pathways that move the product from specification to construction.
Connecting with MassDOT, Growing Production
Sublime Systems has a close working relationship with the Massachusetts DOT, which has been rewriting its cement and concrete specs, according to Williams, to better open the door for new, alternative materials coming onto the market. By the end of 2025, Sublime Systems plans to have its product in MassDOT’s hands to be entered in its qualified construction material list.
“It would be able to be used for future construction projects with Massachusetts DOT and that includes roads, bridges, all of the above,” Williams says. “Obviously, we really need a much greater volume of production before they're going to be able to deploy at scale. But at least we’ll have been approved beyond the list and have those relationships, probably do some initial test pours.”
Finishing of a Sublime Cement floor in Boston, Massachusetts, 2024.Sublime Systems
Sublime Systems has also collaborated with other DOTs when applying for grants to test new materials.
Williams says MassDOT is seen as a leader in the New England area, and a good working relationship with that department could open the door to other DOTs in the region.
A big part of Sublime’s future involves expanding production capacity. The company’s pilot plant in Somerville can produce up to 200 tons per year.
A second, commercial-scale Sublime Systems plant, capable of producing up to 30,000 tons per year, is in the design-build phase and on track to open in 2028 in Holyoke, Massachusetts, says Williams.
Additionally, part of Sublime Systems’ recent $75 million investment with major cement manufacturers will include the development of full-scale cement manufacturing plants around the world, with the first set to come online in 2031.
How It’s Made
Sublime Systems manufactures low-carbon cement through a process that avoids fossil fuels and limestone.
“Cement is a major contributor to carbon emissions, and that's primarily for two reasons,” says Williams. “One, the use of limestone as a feed stock – roughly half its weight is CO2 – which gets released during the manufacturing process. And then the other contributor is the fossil fuels that are used to fire the kiln to high temperatures. And so together, that's why cement is 7-8% of global emissions.
“The two founders [of Sublime Systems] were both electrochemists, actually battery scientists, but essentially applied the principles of electrochemistry to cement production. They developed a new way of making cement, which avoids using a kiln.”
To make this product, the company extracts calcium, silicates and other ingredients from feedstocks, which is then blended into an ASTM-compliant cement designed to replace Portland cement.
Sublime Systems claims its final product outperforms or performs at a similar level to Portland cement on key durability characteristics. Additionally, the electrochemical process produces a lighter product that could better reflect heat and reduce the product variability that can occur with kiln and limestone manufacturing.
Williams says that manufacturing process, if paired with a renewable energy source, is essentially free of emissions.