Pretty soon you’ll be able to buy an electric Bobcat excavator from a company called Green Machine. Who’s Green Machine? What’s the difference between a battery-powered machine and an “all-electric” machine? In this video we break down Bobcat’s unique electric retrofit partnership with Green Machine and discuss the company’s work on making fully electric machines a reality.
Recently Bobcat and Green Machine—a company that is making quite a name for itself in these formative days of electric equipment— made an announcement that establishes an interesting manufacturing partnership that will bring electric excavators to the market in a rather unique way. We’ll get back to that.
But excavators aren’t the only machines Bobcat is exploring electrification in. After all, skid steers and compact track loaders are the company’s bread and butter. Back in March Bobcat brought a compact excavator, skid steer and a CTL to ConExpo that cumulatively represented two different approaches to machine electrification.
So today we’re going to take a closer look at Bobcat’s work toward electrification. After all, last September during the company’s Next is Now event—which, as that name suggests, focused a lot on the company’s gaze toward the future—Bobcat Vice President of Global Innovation Joel Honeyman said that electric machines would be slow in taking off, but would eventually take over completely. Now for context, Honeyman was speaking about the direction of the construction equipment industry as a whole, but he wasn’t excluding Bobcat’s lineup from that trend.
Specifically, Honeyman said it would be 2025 or so until electric machines—including obviously battery-powered machines but also allowing for fuel-cell models as well—before these machines would make up a meaningful amount of the Bobcat lineup.
So if that’s the horizon that Bobcat is aiming for when it comes to machine electrification, this partnership with Green Machine is Bobcat’s starting point. Today we’re going to take a closer look at that partnership, dig into Bobcat’s thoughts on electric machines and those two differing approaches to electrification that we mentioned earlier and hopefully give you a better idea of how the company is going about building the foundation of an electric machine lineup.
A Complex Pivot
You’re probably already aware that there are certain restraints when it comes to manufacturing vehicles powered by lithium ion battery technology. And we could spend an entire article talking about those limitations and the shortcomings of lithium ion batteries like cost and ramping up scale of manufacturing.
But narrowing things down specifically for construction equipment, there are two big ones that currently jump out and they are: 1) charging times, and 2) range, or the number of hours during a work day a full charge can get you.
There’s another more obvious or common sense complication for the companies getting started with electrification, and that’s complexity. These are companies built atop diesel powertrains. Not only that, but you also have to seamlessly integrate this new electric drivetrain you’re working on with existing hydraulics systems. So, pivoting to electrification is not going to be a quick process.
The good news is that helping matters somewhat in this regard has been the increased amount of electronics and technology introduced to the construction equipment industry by Tier 4 Final emissions regulations.
When you add up the advances in engine technology, machine control, telematics and other technology additions that have been made to heavy equipment in the last 15 years or so, the need for more intricate, complex and advanced electrical architecture—essentially all the wiring that runs through the machine—has risen within these machines. And that improved electrical architecture not only paves the way for electrification but, down the line, autonomy as well.
So all of a sudden, getting electrification right has far greater implications. Because, while we’re a ways off from a job site full of autonomous machines, providing full automation for customers that want or need it is definitely on the roadmap not only for established OEMs, but for startups looking for their chance to disrupt the industry as well.
An Experienced Partner
We mentioned earlier Green Machine, the company that Bobcat is partnering with on in this first step toward electrification. Green Machine has built its company and reputation on being able to address the issues we talked about earlier—those of complexity and integrating battery power with hydraulic systems on heavy equipment. And they’ve done that through retrofits on a variety of machine brands. At ConExpo this year the company’s work was seen not only at the Bobcat booth, but at the Takeuchi and Case booths as well.
In fact, Green Machine was Case’s partner in developing one of the biggest announcements at ConExpo 2020, the battery electric Case 580 EV backhoe, aka “Project Zeus”.
To devise these retrofit systems, Green Machine works with two partner companies, Moog Inc. and WhisperDrive. Green Machine and WhisperDrive work so closely they kind of seem like they’re part of the same company or maybe even a subsidiary of one another. They’re not.
Adding to some of that confusion is that on the surface, WhisperDrive is a very similar company to Green Machine because it also has a focus on consulting with OEMs and devising methods for implementing battery technology into heavy equipment. When it comes to Moog, Green Machine leans on its expertise in electric motors and actuators, the components that provide motion to the tracks and tools on a machine.
But Green Machine doesn’t just partner as consultant with OEMs looking to electrify their fleet. They also sell and rent machines that carry the Green Machine brand as well. The company lists three mini excavators, a mini skid steer and a light tower for sale on its website. The two excavators are actually manufactured by Takeuchi and then retrofitted by Green Machine.
A Sense of Urgency
So with the need to not only figure out batteries as a power source and the increased complexity that brings to a machine’s electrical architecture, it’s not a surprise that Green Machine along with the major construction equipment makers have started on the smaller end of machine lineups when it comes to electrification. To put it simply, smaller machines require smaller batteries which require less time during a work day tethered to a charger.
But there are other considerations too such as zero emissions being particularly attractive to jobs well suited for small equipment—urban jobsites, interior jobsites, utility jobs, and so on.
Now, because of this focus on smaller machines, regardless of whether its due to battery limitations or market pressures, this whole situation kind of means two different things for OEMs depending on the types of machines they make.
For companies like Volvo—which inside the industry really took the first major step toward electrifying a machine lineup when it announced that it hoped to replace all of its compact machines with battery-powered models—this restriction is freeing in a way because it allows them to dip their toes in the electric waters. That’s a bit of a dangerously mixed metaphor there, but you see what I’m getting at right?
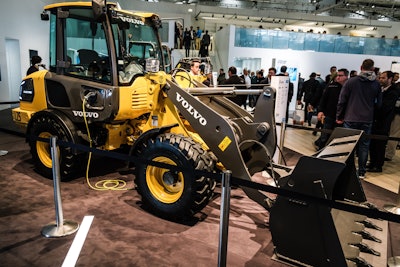
Volvo’s bread and butter isn’t compact equipment. It’s the larger stuff. So they can make a commitment to electrify the smaller machines and expose that segment of their revenues to a new technology while learning more about it and preserving the stability of their larger lineups. To Volvo’s credit though, they’ve long been researching electrification and much of that work started with their larger mining equipment.
For a company like Bobcat though, it can’t really waste any time. It doesn’t have a whole equipment segment that it can experiment with in an active market, take note of all the good ideas that worked and then implement them on the right machines at the right time.
Really, the closest thing the company has to something like that, you could argue, is excavators. Now, I don’t want to suggest that this is the reasoning behind this official announcement with Green Machine. After all, Green Machine’s primary focus has been excavators and there could be some other aspect of this machine type and its engineering that makes it a better candidate for electrification than say a CTL or a skid steer.
But I will point out that starting with excavators is a much more conservative approach in terms of what part of the Bobcat lineup is being exposed to the potential risks inherent with not only implementing a new technology but partnering with an upstart, outside company as well.
Bobcat’s Electric Retrofit Excavator
And apart from the potential risk this move poses to Bobcat, this is also a rather different type of partnership. Just to be clear, this deal with Green Machine only involves compact excavators, despite the fact that the two companies are actually working together on other machine types as we’ll detail shortly.
As part of this deal, Bobcat says that it will manufacture the compact excavators as it normally does, diesel engine and all, and then pass those machines along to Green Machine where those excavators will be retrofitted with a lithium ion battery.
From there, Green Machine—not Bobcat—will handle the sale of these newly electrified excavators. However, unlike the Takeuchi models that Green Machine retrofits and sells, the Bobcat branding will not be removed from these machines. Even though the electric retrofit will be completely handled by Green Machine, the excavator will still look like a Bobcat from the outside. Like I said, it’s a bit of a unique situation.
Here’s the other thing, while Bobcat says these retrofitted electric excavators will go on sale this year, we don’t yet know what size or what model of excavator Bobcat is going to be passing along to Green Machine as of yet.
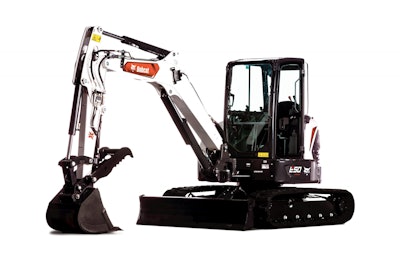
In its press release for this announcement, Bobcat included the above photo of an E50 excavator, so one would assume that model will be part of this deal. However, at ConExpo, where Bobcat showed off some of the work it had been doing with Green Machine, the excavator they showed there was much smaller.
When I reached out to Bobcat to make sure I understood all of this correctly, I asked if there were any other specific models in the works but hadn’t gotten a response prior to this article publishing.
Electric and Hydraulic
The other thing to know about these Green Machine retrofitted Bobcat electric excavators is that while they will be battery-powered, they’ll still have hydraulics. That means they aren’t technically fully electric machines as there will be at least some fluid running through them.
As I said, at ConExpo back in March Bobcat brought some examples of this type of electric/hydraulic machine that it’s working on with Green Machine. (You can see footage of these machines in the video version of this report at the top of the page.) The first of which was a prototype excavator that would be a brand new model for the company called the E17e. Looking at the current compact excavator lineup at Bobcat, this machine would presumably slot in between Bobcat’s smallest model, the 1.1-metric-ton E10 and the 2-metric-ton E20.
The other electric/hydraulic machine Bobcat showed at ConExpo was the S70e prototype, a modified version of the company’s smallest skid steer, the S70.
In terms of charging times and how much run time you’ll get out of these machines during a work day—and bear in mind these numbers could change as both of these machines are prototypes—the E17e has a charge time of only 4 hours—impressively low at this point—with a run time of eight hours if you’re using the machine to 100 percent of it capabilities. What that means is that you could get up to 12 or 14 hours off a charge if the workload is light enough.
The S70e skid steer on the other hand currently requires a 6-hour charge and also has a roughly 8-hour battery life.
The main positive to a battery-powered machine with hydraulics is that you retain most of the feel of operating the traditional diesel powered machine since your implements remain hydraulic. However, while you do significantly lessen your maintenance time and costs on this type of machine—some OEMs say by as much as 90 percent—you’ll still have to maintenance the hydraulics.
And just to be clear, the overwhelming majority of machines—prototype or otherwise—that I’ve seen introduced in recent years be it from Volvo, Case, Bobcat or whoever else, have been like this with the combination of lithium ion battery and hydraulics.
For instance, the Case 580 EV backhoe I mentioned earlier that Case built with the help of Green Machine. That is powered by a lithium ion battery pack tied into traditional hydraulics. And because of that quick electric torque, Case told us at the show that that machine offers better performance than its diesel powered counterpart.
And the 580 EV is already in production—albeit in a made-to-order mode of production—but it’s in production nonetheless thanks to Green Machine’s help. And while it’s clearly only a first step due to the fact that you could see run times as little as 4 hours on the 580 EV if you’re pushing the machine to its max or heavily leaning on the hydraulics, it’s a clear indicator that Green Machine has gotten good enough at integrating batteries and hydraulics that OEMs feel comfortable displaying and even selling this machine setup to customers.
“All Electric”
The thing is, this combination or setup or whatever you want to call it, it’s clearly not the end goal and Bobcat knows that. So, at ConExpo the company showed that it’s already hard at work at realizing fully electric machines with the T76e, an all-electric prototype and a modification of the company’s new T76 compact track loader.
The T76e on hand at ConExpo was equipped with a lithium ion battery pack for power along with electric motors and more importantly, electric actuators instead of hydraulic actuators.
Now, the biggest advantage with moving to electric actuators when it comes to construction equipment is their precision. And that means that operators might feel like they’re operating a completely different machine when they hop inside a machine with electric actuators for the first time. A fully electric machine will deliver torque almost instantly and the actuators will offer precise tool or bucket positioning that hydraulics simply cannot match.
Precision in Control… and Development
At ConExpo I had the chance to speak with Britta Kopp, Bobcat’s marketing manager for innovation. Here’s what she had to say about presenting an all-electric prototype at this moment in time and about the benefits of all-electric machine like the T76e Bobcat had on display:
“We really wanted to push the industry. We know what’s capable with hydraulics and we know what’s not capable—what’s holding the machine back with hydraulics,” Kopp says. “On a full electric platform your precision and your finite control are just exponentially increased. So your capabilities of the machine are truly based on math and coding and programming that computer to do exactly what you want it to do. So you can have so much more flexibility in the machine to do what needs to be done.”
In those comments, Kopp keyed in on another totally different aspect of precision when it comes to electric actuators and that’s the degree of precision this technology gives Bobcat engineers when developing a specific machine and its specs and capabilities.
Essentially, Kopp says that when you have a battery and you have electric motors and actuators, the machine’s capabilities and limitations no longer come as a result of its hardware or components. Horsepower isn’t dependent on a larger or smaller engine. Tool capability isn’t dependent on the amount of hydraulic flow. Instead, Kopp says in an electric machine, all of these things now depend on code.
“It’s all coded in there. It’s a computer programmer going in there and putting in the exact numbers you want all of your performance speculations to be,” Kopp says. “So if you want it to be an exact horsepower, you program that number in and that’s what it hits. So all of your traditional breakout speeds, lift capacities, all of that is all based on programmed code. You’re not hindered by the capabilities of a hydraulic system or a drive motor system.”
And that’s where you find another big reason for Bobcat to push this approach to electrification forward. Last year at the Next is Now event that I mentioned earlier, Bobcat announced that it would start building in more commonality between the new R Series skid steers and compact track loaders that roll off its assembly lines.
Essentially, every new Bobcat CTL and skid steer would be manufactured with all available options equipped and on board. And when a customer purchases one those options—like high-flow hydraulics for example—they’ll be toggled on or off, digitally, at the dealership.
A fully electric machine whose source code controls horsepower, breakout speeds, lifting capacities and more, would give Bobcat or any other OEM the ability to make one machine that replaces several different models. Then you come in, tell your dealer what amount of capability you need and that’s what you pay for.
The takeaway: Rather than models being defined by more components or less components they could be differentiated by a few taps on an iPhone at the dealership.
But getting back to what you can expect from these electrified machines and how they’ll differ from traditional diesel powered counterparts, Bobcat says even though hydraulics are known for their ability to generate a huge amount of force, there won’t be any power drop-off when you go all-electric.
Plus, an all-electric machine brings maintenance and service costs essentially down to zero. And removing the hoses, pumps, filters and all the other bulk that hydraulics require you to route though a machine, that frees up a lot of space. Now, It’s unclear whether or not OEMs will be able to make use of this freed up space—especially when you factor in the fact that electric machines will need large batteries—but there might be some possibilities in the way of improvising visibility or maybe just freeing up a bit of cab space.
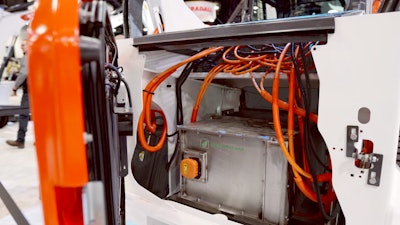
I mean just take a look at the engine compartment of the T76e prototype in the photo above. With the engine removed and replaced by the battery system, there’s a ton of unused space there. There are a litany of ways this could change the design of skid steers and CTLs in the future.
But getting back to the core difference between an electric and diesel machine, at ConExpo Kopp told me that a battery and electric actuators deliver a faster, quieter, more precise and more efficient machine with a bit of a learning curve when it comes to getting used to the different feel of the controls.
“Learning new controls, there’s always a learning curve to it,” Kopp says. “But [what] you can expect is it’s either on or off. So, your speed to do things is going to be increased, your torque—your breakout speed—it’s really just going to be all or nothing.”
When Kopp says the machine is “all or nothing” she’s talking about the availability of its power. Because there’s no engine, there’s no rpms ramping up or down slowing down power delivery. Because of that, electric drivetrains deliver torque at a much faster rate than traditional diesel or gas drivetrains and so having more power more quickly available will definitely take some getting used to for operators—but that’s a good problem.
Kopp also says that the availability and the quick delivery of that power won’t decrease with your battery life. You can expect the same performance at a full charge as you’ll have with 5 percent or less.
Coming Soon
So when can you expect to see electric Bobcat machines—either all-electric of electric/hydraulic—hit the market? Well, the electric/hydraulic will definitely be first. The Green Machine retrofitted Bobcat excavators will go on sale through Green Machine’s channels at an unspecified point in time “later this year”.
The all-electric machines like the T76e are a different story. Kopp tells me that Bobcat has working prototypes in the field today and she added that within one or two years, Bobcat plans to scale up these field tests with more machines on more customer jobsites hoping to perfect this all-electric drivetrain before a full rollout which may come in the next five years or so.