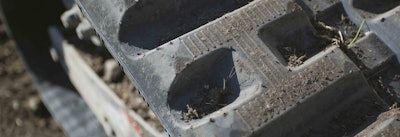
Compact excavators are often workhorses on jobsites, spending the day digging trenches or picking and placing materials. In these applications, or even in more demanding work such as demolition, the excavator has the advantage of sitting in one place and letting the swing of the machine’s house and movement of the boom and arm do the work.
But even though the excavator is not moving back and forth across the jobsite like a skid-steer or compact track loader, tracking the wear on the undercarriage is still a critical part of any maintenance plan.
“Compact excavator undercarriages don’t see the same duty cycle as that of a compact track loader,” says Tom Connor, excavator product specialist at Bobcat. “However, tracking wear is still important, as an improperly tensioned track or worn sprocket could cause additional problems, and additional costs, for a contractor.”
Tracking tracks
A good plan to track the wear on a machine’s undercarriage starts with a daily visual inspection of the tracks. Connor says depending on the applications the machine is used in, tracks may need to be replaced due to old age before other reasons. However, damage to tracks can still happen and a daily inspection will help prevent failure of a track.
Another important item to check is track tensioning. Connor says the tracks should be tensioned correctly, not too tight and not too loose. Referring to the operation and maintenance manual will help keep the tracks in the right tension range.
“Running too tight can suck up power on the machine, Connor says, “while running too loose could lead to a track being thrown when the machine twists and turns in loose materials such as pea rock. That is hard on the track as it puts an enormous force on it that it is not necessarily designed for.”
Undercarriage components
While other undercarriage components may not need a daily inspection like tracks, regular monitoring of the components can help identify potential problems early. Idlers, rollers and sprockets are all components that should be checked.
Connor says that it can be hard to see normal wear on the idlers and rollers, which may need to be measured. However, since the idlers and rollers are permanently sealed and lubricated, a sure sign to look for is fluid or moisture leaking around the seal, indicating a failure. In this case, the preventative maintenance for the machine is to replace the damaged roller or idler, as they are not serviceable at that point.
While accelerated wear on the sprocket is not common, it should still be checked periodically. To check the wear on a sprocket, look at the teeth. A good sprocket tooth has a rounded end, while a worn tooth is more pointed. This is especially important to check when putting a new set of tracks on the machines. “You don’t want to put a new track on a bad sprocket because it will accelerate the wear of the steel imbeds in the new track,” Connor says.
Whether it’s being used as a trenching and excavating application, or to demolish and move concrete, a compact excavator has the same risks of any tracked machine. However, a routine inspection schedule can help identify issues early and prevent extra downtime or damage to the machine.
Editor’s Note: This article was provided by product experts at Bobcat.