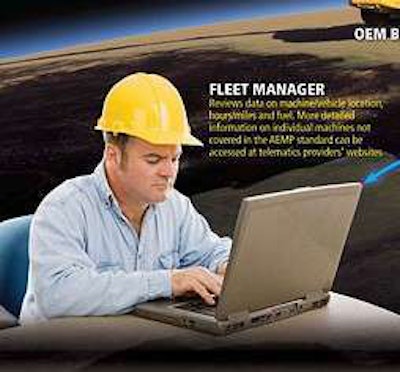
The telematics portion of the 2012 Association of Equipment Management Professionals Asset Management Symposium wrapped up with presentations from contractors and fleet managers with first hand experience in implementing these systems.
First up was Kerry Sudria, corporate operations and technical manager for Kiewit, who said that if for no other reason, Kiewit needs telematics to keep up with its 17,000 pieces of equipment. It’s not hard to understand why telematics is important to Kiewit’s operations when you look at it from the perspective of a service, lube or fuel truck, he said.
On a large jobsite the equipment may be scattered over 20 miles or so. Some of it may be parked in ravines, under bridges or behind buildings. Telematics enables the technicians and lube and fuel truck drivers to find these assets quickly and efficiently.
The second plus for telematics, Sudria said, was the ability to control idling.
“Reducing idle time is an absolute no-brainer,” he said. “Fuel is the highest controllable maintenance cost we have, and fuel cost is just the tip of the iceberg.” The downstream benefit is that you also reduce engine hours and maintenance by an equal amount–as much as a third, he estimates. This reduces the frequency of oil changes and PMs, which in turn means your techs work more efficiently and you need fewer of them and your machines last longer and retain more of their residual value.
“It keeps us from burning up work hours,” Sudria said. “That’s cash back in your pocket.” And by having fewer techs working fewer hours in the field the chances for an accident or contamination or a poor repair are reduced, he said.
Strategically, telematics allows you to improve machine scheduling and utilization, Sudria said. This reduces the need for outside rentals or to overspend on equipment.
Kiewit uses manufacturer telematics solutions whenever it can, Sudria said, but it is also experimenting with innovative ways to use a variety of related technologies. The company is introducing RFID (radio frequency identity) tags to keep up with smaller items such as headache balls, crane hooks and small generators.
The company is also working toward the use of tablet devices for daily visual inspections and reports from the field. And it’s tinkering with an automated lube truck that will be able to electronically read the piece equipment its getting ready to service. It will engage only the pumps for the products that that specific piece needs, log the quantity and send a record of the service back to the office or shop electronically.