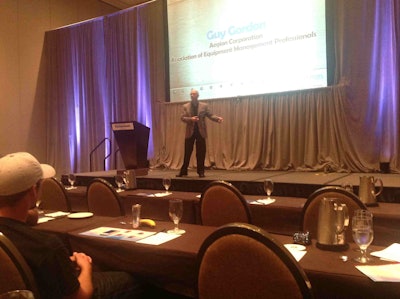
The education portion of the Randall-Reilly Construction Symposium kicked off today in Dallas with a presentation from Guy Gordon, who is director of asset management for Aegion, chairman of the Association of Equipment Management Professionals.
Gordon began by asking attendees to define who manages the equipment in their construction companies. He noted that everybody: operators, service techs, owners, purchasing, supervisors and finance managers, has some say-so in how equipment is managed. Each of these see the equipment in a different light and may have different objectives other that effective asset management. None have the total package: experience, knowledge and objectivity to maximize asset returns, he says.
That’s where a professional equipment manager can prove his worth, Gordon says. Has to be analytical, financially astute, mechanically inclined, efficiency driven, a good risk assessor, problem solver, results motivated, frank and efficient.
With those skills at his disposal the professional equipment manager can offer his company a return on their investment and drive a level of excellence throughout the organization. For example, Gordon said, the equipment managers are usually the first people in the organization to know when a job is going bad. Project managers who are feeling a financial pinch on a job will start deferring maintenance, a sure sign of something gone wrong. That’s one example of where the ability to be frank comes in handy. Otherwise the equipment manager is going to be the first one to get the blame.
High level managers can also look at equipment from the perspective of the financial people including ability to make clear decisions on utilization rates, rental options and disposal. And that can sometimes mean being familiar with accounting terminology and practices. You don’t have to be an accountant, Gordon says, but if you don’t know something about depreciation schedules you can get the company in trouble.
A well educated equipment manager will also steer others in the organization away from making emotional decisions, the sort of boys with their toys thinking or pride of ownership thinking that doesn’t square with the best financial interests of the company.
The kind of top tier fleet managers Gordon referred to can come from a surprising number of disciplines. The typical scenario is a technician who works his way up, but there are also plenty of financial personnel with high mechanical aptitude, engineers knowledgeable in accounting principles and others with high level of motivation to understand the requirements of the profession. This includes many people with college degrees and advanced degrees.
Gordon cites the Association of Equipment Management Professionals as the best source for furthering the education of people who want to move up in this field. The association offers a Certified Equipment Manager course that he and many of his equipment managers have taken. “They used to think I was nuts until I had them take this course and then they were able to see the reasons behind what I said and what I do,” he says.
The coursework for the CEM certification includes: financial management, procurement management, benchmarking, lifecycle costs, technology, personnel policies, safety, technology, controls, parts management, preventive maintenance and more.
For more information visit AEMP.org
.