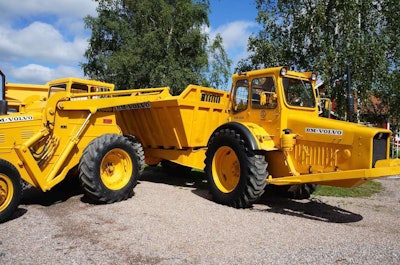
Volvo Construction Equipment says it has begun using additive manufacturing techniques not only as part of the company’s process for prototyping new machines, but also to supply customers with replacement parts.
Known more commonly as 3D printing, additive manufacturing creates three dimensional objects by slowly placing layers of a molten metal or liquefied plastic in a pattern or shape laid out by the printer’s software. The printer software creates its initial renderings for the 3D-printed parts using drawings from the Volvo archives, 3D models and product information. Printing a part can take as little as one week, Volvo says.
The company is currently printing the replacement and prototype parts with plastic and says that “parts can be made of any shape and size, and for any unit in Volvo CE’s range of off-road machinery.” Parts printed with metal may be offered in the future.
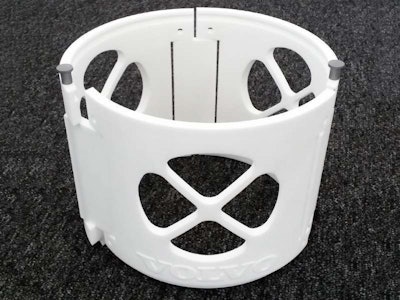
“We are supporting customers through the life cycle of their equipment,” says Jasenko Lagumdzija, Volvo CE’s manager of business support. “It’s especially good for older machines where the parts that have worn out are no longer made efficiently in traditional production methods. Producing new parts by 3D printing cuts down on time and costs, so it’s an efficient way of helping customers.”
Cabin parts, plastic coverings and sections of air conditioning units are some of the more typical spare parts the company has printed up until now.
“The customer is getting exactly the same part in replacing plastic with plastic,” says Annika Fries, aftermarket branding manager at Volvo CE. “We do a lot of quality assurance – the 3D parts have the same specifications and go through the same process as the original, and get the same warranty, so customers can be confident they are getting a genuine Volvo approved part.”
Beyond the customer benefit of extending the life of a machine whose parts are no longer being manufactured, Volvo says 3D-printed parts benefit the company in big ways as well.
“Lead-times are significantly reduced with 3D printing and since there are no minimum order quantity requirements, we benefit from quicker delivery of parts, lower inventory levels in our warehouses and an improved ability to balance supply and demand,” says Daniel Kalfholm, Volvo CE’s project leader for aftermarket purchasing in the EMEA region. “And it can all be carried out a purchase price that is comparable to that of a traditionally manufactured component.”