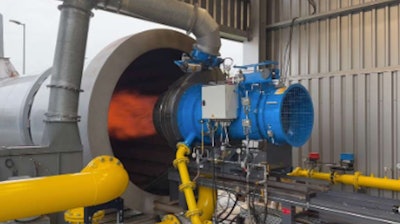
Wirtgen Group member Benninghoven has unveiled the world’s first hydrogen-powered burner for asphalt production.
The new burner from Benninghoven runs on 100% green hydrogen, with the first user producing "several thousand tons of asphalt virtually no emissions," the company says.
The burner is intended to be a step in reducing the high carbon emissions of asphalt production for road construction.
Low-temperature asphalt, recycling rates of up to 100% reclaimed asphalt, and now hydrogen has been identified as the most environmentally friendly energy sources that would be sustainable, future-proof, cost-effective, and significantly reduce emissions.
Asphalt production requires a thermal process in which industrial burners heat and dewater the starting material – aggregates and/or reclaimed asphalt – before it is mixed with bitumen.
The new Benninghoven burner generation enables the use of up to four fuels at the same time, in three aggregate states.WIRTGEN GROUP
Currently, the most sustainable fuel available is green hydrogen. Producing no greenhouse gases, it is suitable for the heating process due to its high energy density. In addition, emissions, specifically nitrogen oxide (NOx) are kept very low.
Power consumption has been reduced by 20%, and there is a 5-decibel reduction in noise from the new unit. By maximizing the use of burner space, heat transfer efficiency has been significantly improved. Also, the system includes burner control and geometry that ensures optimum flame production, the company says.
With the Benninghoven system, up to four separate burners can be operated at the same time.
According to the company, fuel types can be changed on the fly without operators needing to shut down the system. The usage flexibility increases efficiency and allows owners to determine the best available energy source.
Benninghoven says the new burners can be installed new or retrofitted to existing systems. The upgrade technology package is available now.
Using hydrogen as a fuel sources, emissions have been reduced, power consumption is down 20% and the overall process is smoother.Benninghoven