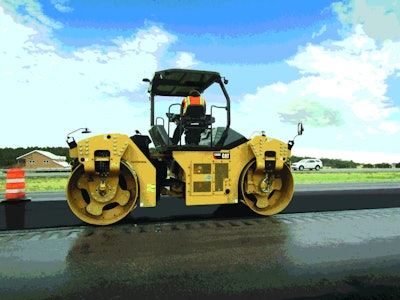
Caterpillar has introduced three models as part its B-series tandem vibratory asphalt roller line that incorporate new intelligent compaction enhancements, operator control advancements and an edge management system.
Intelligent compaction
The CB64B, CB66B and CB68B rollers feature the Cat Compaction Control system with auto-adjustable compaction, mapping for pass count and temperature, compaction meter value and machine-to-machine communication capabilities.
“Embedded into the bumper is our infrared temp sensor,” says Bryan Downing, global sales consultant with Caterpillar Paving Products. “This temp sensor is blasting out a sonic wave in a conical shape that bounces back and is recorded as a temperature and the operator sees that at the operator station. That’s the first level of intelligent compaction – empowering the operator with more information than they’ve had before.”
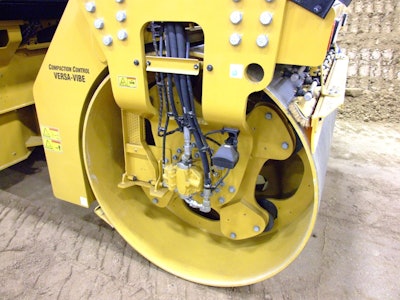
The next level of intelligent compaction data the machines produce, Downing adds, is pass count via GNSS mapping. “This will enable an operator to simply keep track of the number of passes—If that pass target is two passes or if it’s four passes. Sometimes with a very monotonous job like a roller operator is it’s hard to keep track of that information.”
Keeping track of pass maps has been made easier by adding machine-to-machine communication capabilities between operating displays on multiple machines at a worksite. This is ideal for pavement applications with five or seven pass rolling patterns in an echelon compaction setting where a trailing operator can pick up any missed coverage that is highlighted on the operator’s display panel.
Downing says the final step in Cat Compaction Control is adding an accelerometer that reads acceleration of the drum into the ground. The ground’s response is what is measured and the ratio of the two is output to the operator as the compaction meter value.
“The auto adjustable vibe system (Versa-Vibe system) is a system that has a dedicated accelerometer, a dedicated ECM (Electronic Control Module) that’s creating computations of that accelerometer reading and making adjustments to the vibe system,” Downing says. “All of our vibe systems have manual adjustments with exception of the auto adjustable one. That one automatically drives the highest amplitude, which delivers the maximum energy into the asphalt which drives for the quickest compaction.”
Operator control
With this new series, the operator’s seat slides from one side of the machine to the other and rotates 360 degrees. That rotation offers a unique change to the propelling system.
When the cockpit is slightly canted toward one end, pushing forward on the joystick propels the machine in that direction. Rotating the seat to slightly canted toward the opposite direction allows the operator to push the joystick forward and move in that new direction.
“It’s intuitive for operators so there’s no misconception,” Downing says. “Previous models for us we sat perfectly sideways. As a safety feature we’ve built complete visibility with this 360-rotating station, but also an intuitive control that changes.”
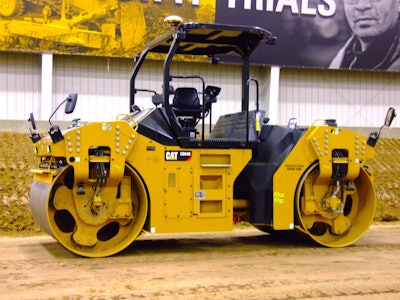
Edge management
The B-Series also offers a finishing tool that creates a clean edge to asphalt when needed, in both a bevel orientation and a clean cut off.
“The edge system is almost a must for every for unconfined action,” Downing says. “Not only do you put a nice clean edge on it, but you also create a better density on that edge. That’s what I really like about it and every chance I get to promote that with DOTs (departments of transportation) I’m doing it. The other side of that compaction wheel is the cutoff, and that’s used when you’re not confident and you don’t like the density that you’ve produced. You cut and discard the material. On a normal highway that’s unnecessary, but airports are examples where uniform density is critical.”
The CB64B has a 79-inch drum, while the CB66B and CB68B feature 84-inch drums. All models have a Cat C4.4 142 hp engine with Eco-mode and automatic speed control standard.