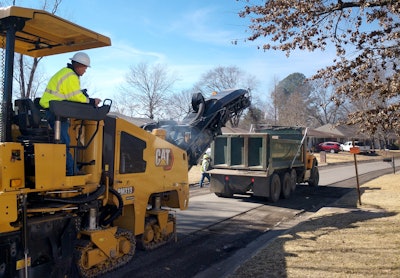
Caterpillar’s PM300 series cold planers have been updated with multiple design enhancements designed to improve machine performance, operating comfort, and milling power.
The PM310, PM312, and PM313 cold planers are designed for small to medium-size applications where a more compact, maneuverable machine is required. These updates mark the third generation of this series since its debut in 2018.
According to Jameson Smieja, Caterpillar sales support consultant, there are more than 20 improvements overall.
One of the changes was the integration with the Cat C9.3B engine, an upgrade from the Cat C9, which the PM300 series cold planers had been powered by since 2018.
“It's a lower complexity engine with improvements to the exhaust, fuel, and the air system,” Smieja said. The C9.3B offers a gross power rating of 343 horsepower.
Elimination of the exhaust gas recirculation system further reduces the complexity of the engine for the end user and provides a boost in gross horsepower and torque for milling operations.
In addition, he said easier access to engine oil filters simplifies maintenance, while multipiece, cartridge-style engine filters reduce waste and lower replacement costs.
Among the updates on the PM300 cold planers is a transition flashing between primary and loading conveyors, improving the containment of material.Caterpillar
Comfort Upgrades
Smieja said the PM300 series redesign includes several updates based on customer feedback related to the operator comfort environment. One of the big ones was lighting.
“These machines have always had attachable work lights to put around the machine,” Smieja said. Previously, Cat offered a halogen and kind of bright spot LED option. Today, the company has brought over its wide-dispersion LED working and LED roading light options from its larger planer platforms to the PM300 series to improve safety and visibility during milling and transportation around the jobsite.
“We brought that technology over into our smaller mills to help cast a wider amount of white light around the machine so when customers are milling at night, or at the end of the day or doing cleanup they can just have better visibility all around,” Smieja said. “It's safer, it's more comfortable for them to work and they feel a lot better operating the machine.”
Ventilation systems have also been upgraded on each machine.
One option on cold planners is to essentially have an extraction system. With a fan at the top, various tubes are routed into the material removal system to help pull any dust and fine material up and out and send it to the far end of the conveyor, where it's nowhere near the operators working around the machine.
“Without a system like that, it's not uncommon to have material and smoke leaking out around the cutting chamber, along the conveyors and things like that and that suction system helps pull that out,” Smieja said.
The latest PM300 series design includes a redesign of the transition flashing between primary and loading conveyors, improving the containment of material, and reducing build-up on the front machine frame.
“It's a moving belt conveyor so it's hard to keep a tight seal on something like that it's going to wear out immediately as it rubs against the welds,” Smieja said. “It's pretty common to come up to a machine like this and see material kind of spilling out.”
Improvements have been made along the entire conveyor system with updated seal designs where the conveyor attaches to the cutting chamber along the sides as well as where the first conveyor dumps onto the second to ensure the material is better contained and not able to spill onto the jobsite.
Further containment of material is achieved through feature enhancements to the right-hand side plate, chamber-to-conveyor sealing, and loading conveyor belt sealing. Front track deflectors positioned in front of the drive motors offer additional protection from debris impact and build-up, improving service life.
Offering the ability to be stowed when not in use, Cat also is now offering an exhaust deflector option on the opposite side of the machine.
“Some customers were telling us ‘Hey, when I'm running close to a building run and right up next to maybe windows in an apartment complex, that exhaust is blowing out towards those things,” Smieja said.
The optional deflector redirects exhaust away from buildings and ground personnel to improve the working environment.
“We want to make sure the machine does a good job getting that up and out of the way,” Smieja said.
Lastly, he said operators can now track the cutting edge from either side of the machine thanks to the addition of an adjustable on-screen guidance line feature to the left-hand camera. Ground personnel can also now control the obstacle jump capability from the rear ground controls to improve milling efficiency.
Cat will soon make VisionLInk Productivity, which helps measure, monitor and manage assets to maximize productivity, on PM600 and PM800 series cold planers.Caterpillar
High-Vision Telematics
In the coming months, VisionLink Productivity, the highest subscription level of VisionLink, Cat’s telematics offering, will be available for PM620, PM622, PM820, PM822, and PM825 cold planers. The VisionLink Productivity suite gathers, analyzes, and summarizes detailed telematic data such as time spent waiting for trucks, cutting and travel at the jobsite as well as distance cut, fuel burn, location, and cycle mapping.
“The main focus is helping the customer run the most productive and efficient job site, lower their costs, and improve their efficiency,” Smieja said. “We like to say the goal of it is to measure, monitor, and manage your operation.”
Whether it is a larger contractor with dozens of machines or an owner/operator seeking to keep track of one or two machines without being on the job every day, data is available on exactly how machines are performing in terms of productivity and utilization.
“With the full VisionLink Productivity suite, they get down into the into the details of what exactly is going on within that machine,” Smieja said. “That can become very eye-opening to the customer and give them the ability to start questioning the details of the operation.”
The system eliminates the need for contractors to collect such data manually and offers detailed reports in PDF, Excel, and CVS formats and can be scheduled for email inbox delivery.