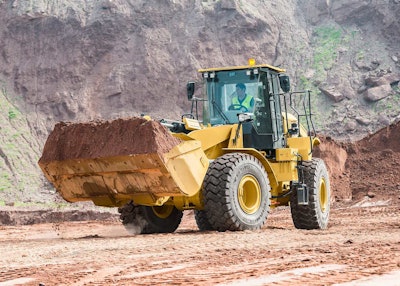
While there was an overarching technology theme to the massive ConExpo show earlier this year, the big story in the heavy equipment industry has been all about data. Specifically, the data coming off your machines’ telematics, and how that data can become a key part of your overall jobsite management picture, not to mention a manufacturer’s profit statement.
Before, manufacturers fought to be your machine supplier; now they’re fighting to be your data provider. The stakes are much higher than machine dominance.
Paolo Fellin, Caterpillar vice president, said bluntly: “Instead of Cat being a brand on the jobsite, we’re pushing to make Cat the jobsite brand.” He adds: “Before, we had the voice of the customer and the dealer, and now we have the voice of the machine.”
At ConExpo, both Deere and Volvo announced central telematics hubs for their machines, with Deere’s Machine Health Monitoring Center in Dubuque, Iowa, and Volvo’s Uptime Center in Shippensburg, Pennsylvania. Each company says their hub will be manned by data experts analyzing the big picture from aggregated machine information.
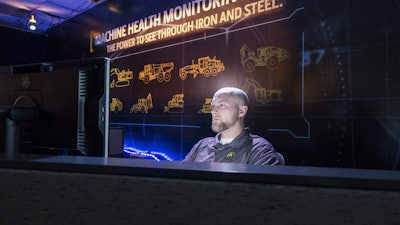
Short-term, these hubs will expedite essential machine health information to customers and dealers. Deere’s effort, for instance, will “get the right information in the right person’s hand at the right time,” Tim Worthington, manager, product support services, told me at the show. “Before, support operations have been largely reactive. This is devoted to preempting failure and driving action.”
But this is about much more than alerting you about excessive idling. It’s now about squeezing every asset dollar through jobsite uptime and productivity gains.
For example, says Volvo, idle-time knowledge can help point out where a machine’s jobsite path can be reconfigured, or perhaps even if a customer is using the right machine for the job. Deere anticipates their data analytics capability will help them develop and deploy solutions to repair machines faster, and even avoid downtime altogether. Cat says telematics information has already informed machine design, such as its new 950 GC, a lower-spec loader intended to appeal to lighter duty operations.
And companies beyond machine OEMs are getting into the data act, proposing sensors that will indicate oil fill times, combat coolant leaks and accurately predict fuel burn. (See Tom Jackson’s column on page 82.)
The recent Association of Equipment Management Professionals telematics standard—which standardized key telematics data no matter what the color of a machine—has been the great enabler, and now manufacturers and software firms are scrambling to get their mixed-fleet solutions and other data-based products into your hands. Include the drone alliances (Deere with Kespry, Cat with Airware) that will add even more data points to your back office and jobsite systems, and then top it off with the fact that telematics adoption rates are still at a low 15 to 20 percent, and everyone can smell the growth.
As dealer Chris Zaharis with Empire Cat puts it: “We see data as the new natural resource, and we’re in a hurry to get our customer’s assets connected.”