By Elliott Stanton
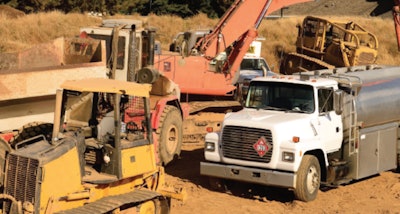
Our location in the Eagle Ford oil fields of Texas contains a state-of-the-art fueling station to keep trucks, tractors and support equipment fueled up and ready to go on a moment’s notice. As the onsite equipment manager, I also inherited the title of fuel manager and have been tasked with all of the responsibilities that go along with that title.
I’ve encountered fuel related issues on many occasions and seen firsthand the costs associated with fixing them as both an equipment manager and in a previous job at a dealer. I’ve also been a part of many fuel related discussions, and have come to realize that most companies have little information when it comes to fuel storage and filtration. After yet one more expensive fuel system repair, I decided there had to be a better way to manage these expenses, and took to researching fuel filtration.
New engines and fuel issues
Ask any contractor, and they’re all aware of the EPA tier emission regulations that have been enacted over the past 10 years. We all understand the intention of these regulations, and many contractors understand the general methods used to reach those goals, but most don’t fully understand the impacts that these regulations forced on engine design, which in turn have affected how engines function.
To better understand that, we first need to look at what has changed in today’s engines. One of the major sources of emission reduction is obtained by establishing a more complete burn of the diesel fuel inside the combustion chamber.
Ten years ago, most diesel engines used injection pumps that ran at roughly 3,000 psi. In today’s motors, those pressures can reach as high as 36,000 psi or more, a significant increase. Additionally, the sizes of injector orifices have been reduced. Putting this high-pressure fuel through smaller injector orifices creates a finer atomization of fuel inside the cylinder, and creates a more complete burn.
The downside of this design is that this high pressure turns small particulate matter into destructive projectiles inside your fuel system. These particles blast their way through your pumps, your connectors and fittings, and finally, your injectors. As with all aspects of these new emissions compliant engines, the prices of these components have seen major cost increases as well. It’s not uncommon for injectors to run $1,200 to $1,700 each. Fuel pumps can run thousands of dollars, and due to their complexity, are harder than ever to rebuild.
Water’s destructive impact
In addition to managing particulates in the fuel supply, we also have to be much more aware of water intermixed in diesel.
In our older Tier 1 engines, water could be a nuisance. In today’s high-tech engines, it can destroy entire fuel systems in just a few short minutes. Unlike diesel, water isn’t easily compressed and damages injectors and high pressure pumps. What’s more, some of the components in modern fuel systems are made from high-tech alloys that oxidize from exposure to water, creating additional particulates in your fuel system. But, the most frequent danger is that water in the fuel will blow out the tips of your injectors. And even on a four-cylinder backhoe or skid steer, you could be talking $4,000 or more on injectors alone.
Reducing or eliminating failures caused by contaminated fuel can create substantial savings in parts and service. Reduced downtime is another major source of savings that comes with properly filtering fuel. These two areas alone justify substantial investment in fuel filtration.
Cleaner fuel for reduced emissions
The other main area of savings for diesel filtration is in the emissions themselves. In removing the particulate from our fuel pre-burn, we eliminate those particles from the exhaust. Every contaminant that enters the combustion chamber of your engine is leaving through the exhaust, or worse yet, bouncing around in your engine. Anyone running a diesel particulate filter (DPF) understands the costs associated in having those filters cleaned or replaced. Compared to DPFs, fuel filtration is inexpensive, and by reducing build up in the filter, you also reduce regeneration intervals and save the diesel required to do a burn off of the DPF.
We’ve seen costs of cleaning these DPF’s run $800 to several thousand dollars per occurrence, in addition to the down time loss. Our experience shows that these cleaned DPF’s have a reduced second life, but with DPF and diesel oxidation catalyst (DOC) filters running $4,000 or more new, we continue to analyze costs of replacement versus renewal via cleaning. Either way, we’re talking about a major cost of ownership in DPF filters alone.
OEM fuel filtration
By in large, engine and equipment manufacturers have upgraded their filtration systems. So the argument that engines already have fuel filters is valid, but not all fuel filtration systems are equal, nor are they infallible. Some filters only go down to 10 microns, whereas others can go as low as 2 microns. The differences in those particulate sizes are substantial when talking about today’s low-tolerance engine designs.
As part of my research into finding clean diesel solutions, I talked with Dan Cummings, the owner of Tech-Smart in Reno, Nevada. Dan was raised on diesel and became a certified mechanic, working on heavy equipment in large mines and quarries across the western United States. (Dan’s been an excellent resource for technical knowledge throughout my project, and I owe a lot of this article to Dan.)
Dan was able to show me several options on the market that we could use to clean up fuel-related issues in our fleet. Seeing a demand for improved filtration, the market has responded with some excellent solutions. When talking to other equipment managers, the general belief is that filtration is a massive expenditure that will be hard to justify. But, there are plenty of great options out there for all sizes of operations and budgets, as well as fueling sources.
For example, with our heavy equipment fleet, 99 percent of our fuel is coming from either one of our locations or a temporary onsite fuel station. In that case, the cheapest and easiest solution is to put high level filtration on the supply sites and use OEM on-board fuel filters as the final protection only.
Our four bulk fueling hubs across the continental United States are filled directly from the manufacturer. The only filtration at these locations is on the exit end of the tank. Each fuel bay has two pumps with inline filtration prior to the standard filters at each pump. The fuel pumps are equipped with standard filters directly at each pump. From there, the fuel goes directly into a truck, or is stored for later use in a fuel tank. Tanks are equipped with filters and are changed out with each service every 5,000 miles. Fuel trucks delivering fuel to jobs and machines have filters changed out as part of a standard maintenance plan.
One of my favorite bulk filters are those made by Waterguard filters. These are not the cheapest filters on the market, but in my opinion, they yield the highest results. Waterguard filters have a revolutionary bushing system that allows for one filter to fit all your applications reducing inventory. I recommended buying them in bulk, as there is substantial savings in doing so.
Don’t get complacent
One of the biggest pieces of advice I can offer when working with filtration is to not be complacent. Like myself, many of you have other hats to wear, and just because the filter is screwed on tight doesn’t mean you can forget about it. Setting a schedule for filter replacement is important, but that’s not the only thing. Periodically testing for water in fuel before and after new loads allows you to stay on top of quality.
A general rule of thumb is to never fuel up during (or within 20 minutes after) an above ground tank fill up. This is not the most ideal time, as the fuel in the tank is stirred up and a lot of stress is put on the filtration system. Remember, you want to filter out as much particulate as possible so you don’t put the stress on your DPF filter to do it later.
I should point out that even with small micron filtration at the pump, it is still critical that preventive actions are taken on the machines as well, such as filling up a tank at the end of the day to reduce water condensation. By leaving tanks empty overnight, you’re collecting water through condensation in your tanks, negating your filtration efforts at the distribution center. Fuel management doesn’t end until the fuel has been burned in the combustion chamber.
In other applications, the investment in supplemental onboard filtration is also worthwhile, due to random fueling locations and use of outside fuel sources with unknown filtration and fuel management. In our operation, haul trucks need onboard filtration due to the high amount of off-site fuel consumption. Not all fuel is equal, so we must manage fill ups with the help of inline filtration. For this, we have found that Wix filters work best and they are accessible at any auto parts store. Should a driver run into some bad fuel, they can easily remove and replace the inline fuel filter before it damages the onboard OEM filter and leaves him stranded.
Conclusion
The costs of these modern engines and their components, as well as their downtime costs, are justifying investments in filtration that, frankly, were not economical even four or five years ago. The industry is seeing these increased costs of operation, but most are not actively looking for solutions or fixes.
The hope is that engine and equipment manufacturers will step up to the plate, but due to the massive time and financial costs of developing these new environmentally friendly engines, most are cash and time constrained. They’re also caught in a market that is increasingly reliant on parts and service revenues to offset lower margins on new equipment sales, and also trying to offset government-mandated engine development costs. Because of that, I do not expect any major improvements, and believe that progressive owner operators will be best served to make their own investments in research and aftermarket filtration solutions.
Fuel filtration and management has never been more demanding, nor have the potential costs and savings been so high. Today’s equipment managers need to take a proactive role in implementing fuel filtration and management programs. Your bottom line depends on it.