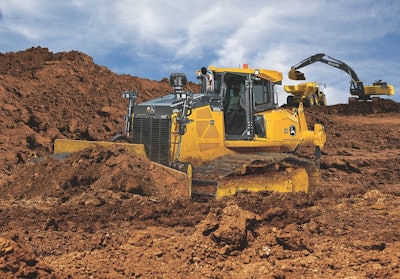
By Richard Ries
The general public may perceive dozers as simple, lumbering beasts. But those in the construction industry recognize them as focal points of advanced technology.
One of the most obvious advances in dozer technology is ever-improving machine control. “You could argue that no product category has been more affected by the continued adoption of machine control than dozers,” says Nathaniel Waldschmidt, product marketing manager, Case Construction Equipment.
One challenge with machine control is to present the greatest value and flexibility in a segmented market. Waldschmidt says Case accomplishes this with Universal Machine Control, introduced in 2018. “This allows customers to buy the machine from the factory with a universal blade guidance-system harness and universal machine brackets and mounts that integrate into any of the major machine control systems on the market.”
With Universal Machine Control, customers can install the machine control system they prefer. When the machine is ready to go to the secondary market, the second owner enjoys the same flexibility in system choice, and the first owner can easily remove the system for use on other equipment. Case is also going mastless with their new on-cab dual GNSS machine control system.
Smart everything
The markets are awash in smart products. Smart phones. Smart refrigerators. Smart cars. And now smart dozers. Integrating all these smart products is IoT, or the Internet of Things.
Liebherr introduced INTUSI at Bauma in April. INTUSI (INTelligent User Interface), which will be used in all Liebherr earthmoving machines and material handlers, relies on IoT technology to share information widely, whether that’s between machines or between machines and humans. The human interface is via touchscreen monitor. To ensure accurate interaction in rough underfoot conditions, input can also be provided via haptic controllers. Individual user adjustments can be made using INTUSI and then saved in an operator profile.
Jonathan Tolomeo, product marketing manager, Komatsu, says the system is designed to mimic the skills of seasoned operators. “This allows new hires to become proficient in far less time than they would have in the past.” He also notes that aftermarket systems tend to be used only for finish grading, or about 20 percent of a dozer’s duty cycle. Because the new dozer logic is useful from first to last pass, it has muc
h higher value. System hardware is essentially unchanged and relies on the same sensors and other components that have been in use on Komatsu dozers since 2013. The improved logic accesses much more information from that same hardware and makes better use of that information.
Features that didn’t exist 20 years ago and had only limited availability 10 years ago are now standard equipment on most or all dozers in an OEM’s lineup.
For example, John Deere provides a full range of features as basic equipment. Eco mode yields up to 20 percent fuel savings, while Auto Idle and Auto Shutdown further enhance fuel efficiency. SmartGrade 3D offers factory-integrated, mastless 3D grade control from first to last pass as a baseline of performance. Auto SmartGrade integrates the grade control
Electric drive
“Technology isn’t only about grade control,” says Sam Meeker, product application specialist, Caterpillar. Cat’s new D6 XE dozer features advanced technology in its electric drive system. It uses a single motor to drive the dozer in forward and reverse and a hydraulic differential steering system. Cat says the D6 XE offers up to 10 percent greater productivity and up to 10 percent fuel savings than previous models. Meeker says that while everyone enjoys the ease of electric drive, the numbers work best for longer-term owners (three years or more) and those putting at least 1,600 hours per year on a dozer.
Diesel-electric drive has been a mainstay in the rail industry for decades and is seeing growing interest in shipping and other markets. The operating efficiency and instant torque of electric drive would benefit construction, too. So why has it taken so long for the design to migrate to earthmoving?
Meeker says it’s been an issue with size and what he calls “packageability.” The D7E was a low-drive unit as a concession to this packageability problem. But recent advances, including big gains in the power density available in generators, has whittled down those problems and the D6 XE is a high-drive machine. Another advancement is the use of switched reluctance motors, which are rugged, efficient and work well in variable-speed and reversing applications. This is critical for dozers, which, unlike locomotives and ships, are constantly changing speed and direction throughout their duty cycle.
Humans still required
All the smart features in today’s dozers are meaningless if people are locked out of the process, so manufacturers have taken steps to improve communication between machines and humans.
Caterpillar has an entire catalog of YouTube videos on the various functions and features of its new monitor. (Search for “next gen dozer monitor” for a list.) One example Meeker cites is the ability of an operator to define a work mode using the monitor as an interface. Up to 17 operating parameters can be set and stored as a profile, such as “heavy dozing” or “slope work” or “
spreading.” Mode names are created by the operator.
Waldschmidt says Case’s M Series dozers – specifically the 1150M, 1650M and 2050M – allow operators to independently set blade sensitivity, dozer steering sensitivity and shuttle sensitivity to one of three modes: smooth, moderate or aggressive. This allows operators to quickly and easily match machine performance to their preferences or to job conditions.
Nick Rogers, product specialist, Liebherr USA, says Liebherr’s LiDAT system is available on every size dozer the company manufactures. An additional Teleservice package allows Liebherr service personnel to log in to machines remotely for diagnostics and repairs. LiDAT is enhanced telematics with much more robust data management, including the ability to manage data from multiple machines, whether they are all Liebherr or of mixed brands.
Despite advances in information exchange, the value of the technology still rests on its use. “The data stream is essential to productivity,” says Rogers. “But what are you doing with that information? Are you looking at it on a consistent basis? Being able
Better basics
While advanced technology is apparent in the marketplace, manufacturers are also building better basics.
Dressta launched their S Series dozers in 2016 with a new powertrain. Features common to the full range of Dressta dozers include a modular powertrain design with Cummins and Perkins engines and hydrostatic drive, six-sided ROPS cabs and one-piece mainframes. Blade choices include a six-way option, and both single- and multi-shank rippers are available.
While Dressta dozers employ three joysticks (drive, blade and ripper), their overall use of electronics is low, in part to keep costs down. This is not to say they’re primitive. For example, Cummins engines can be adjusted to give fuel-consumption options that were not available on earlier models, and shift presets can be altered to change how aggressively the machines respond to operator input.