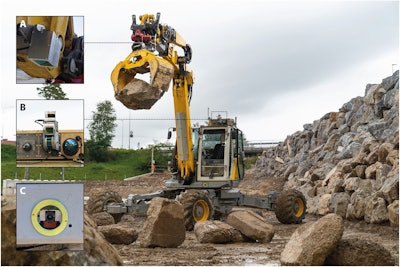
Researchers at RTH Zurich have trained a modified excavator to build a 215-foot-long stone retaining wall in Switzerland.
The 12-ton Menzi Muck M545, known as HEAP, or "hydraulic excavator for an autonomous purpose," was equipped with satellite navigation, inertial measurement, joint angle sensors and multiple cabin- and arm-mounted LiDAR sensors and cameras to map the site and scan the building materials.
(To watch the M545 in action, check out the video at the end of this story.)
Each stone was individually picked up, laser-scanned by the excavator’s grapple, placed back on the ground for storage and saved in the excavator’s inventory to later match to a spot on the wall. As the stones were placed on the wall, the excavator rescanned them and updated its geometric planner.
Researchers say this process was repeated each time after all scanned stones were placed or after the planner was no longer able to find solutions with the available inventory. The final wall consisted of 938 unique elements, with a mixture of reclaimed concrete, mixed erratics and gneiss boulders.
Because the test took place on an active construction site, a human operator remained in the cab to provide oversight and avoid accidents. The scanning, picking and placing were performed autonomously while the operator assisted with driving between operations.
When combining the scanning and placing tasks, each stone placement took the excavator 21 minutes to complete. That time dropped to 12.2 minutes per stone when excluding the preparatory scanning time. Field observers noted that a skilled human excavator operator averaged 11 minutes per stone placement.
“We are currently outperformed by human excavator operators in placement speed. Such operators, however, typically require string and paint references with which to register their construction and often a second or third person outside the machine to provide guidance and to insert small supporting stones, gravel, and soil by hand and shovel,” researchers wrote in Science Robotics. “In contrast, our process can build complex nonplanar global surface geometries without physical reference markers, does not require a skilled driver or small supporting stones, and provides a full digital twin of the built structure for better accountability and future reuse.”
The completed project – which can be seen at Circularity Park in Oberglatt, Switzerland – illustrates the potential for autonomous equipment to build with irregularly-shaped materials.
“Our use of local and reclaimed materials for the robotic assembly of dry-stacked structures has been applied toward the construction of freestanding and retaining walls, but the process could also be adapted to the development of coastal defenses, transportation, agricultural, or extraterrestrial infrastructure and as an alternative building method in sustainable disaster recovery,” researchers said.
Check out a video about the project from ETH Zurich below: