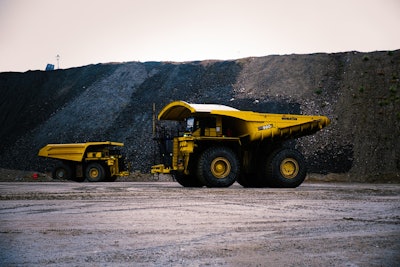
Though autonomy is a hot topic across several industries as self-driving cars and heavy trucks hold the promise of changing the way we transport ourselves and our goods, it’s old news in a way for mining.
Construction and mining equipment manufacturer Komatsu traces the roots of its autonomous technology back 30 years ago, long before the debates over whether Teslas should drive themselves on the open highway or whether it was safe for Uber operators to take their hands off the steering wheel. Today, Komatsu’s Autonomous Haulage System (AHS), which both operates and manages fleets of self-driving mining trucks with capacities between 200 and 400 tons, does so in mines at three locations around the globe. This month, Komatsu says it will hit a major milestone: 2 billion metric tons of material moved with these AHS trucks.
It seems autonomy has become Komatsu’s top priority, and not just on the mining side. The company also offers intelligent Machine Control, an integrated machine control platform on its construction machines that is capable of semi- or fully autonomous operation.
As we heard from Komatsu America officials in a recent report detailing the history and evolution of the company’s Smart Construction service, Komatsu’s ultimate goal is jobsite optimization by building machines that work in harmony with site plans that are digitally created and frequently updated. Machine autonomy and networking is the technology that makes that goal possible and it’s where a significant portion of the company’s research and development focus is placed right now.
The home base for those autonomy R&D efforts for mining equipment is Komatsu’s Arizona Proving Grounds (AZPG), located on 700 acres of remote desert about 45 minutes south of Tucson. What goes on there is so guarded that the company has never allowed any members of the media inside. That is, until this week.
Komatsu invited us out to the AZPG facility in order to fully acquaint us with its AHS system and all the work involved in implementing autonomy on existing mines.
History of AHS
Komatsu AHS is used in four mining applications: oil sands, copper, iron, and coal. The system manages 130 mining trucks globally for three different customers: Suncor Energy, Codelco and RioTinto. Komatsu says it is the first company to achieve 10 years of in-mine autonomy success and says that there have been zero safety incidents in the system’s entire existence.
Brian Yureskes, Komatsu director of global business development says that the system traces its roots back to 1997 when Modular, creators of the Dispatch fleet management system for mining, joined the Komatsu family of companies.
Using custom hardware and software, Dispatch made waves in the industry by allowing mines to optimize the assignment of haul trucks to loading and dumping locations while producing operator reports during a shift. That same year, Komatsu integrated GPS into the design of the autonomous system for the first time.
Testing of AHS began in 1990, but it wouldn’t be until 2016 that the first North American deployment came at Suncor.
Yureskes says that there is a spectrum of technologies and equipment within its autonomous system including manned machines, computer-assisted operations of manned machines, teleremote control of machines, and all the way up to full control provided by artificial intelligence.
Due to the fact that today’s mines have a wide range of both old and new trucks, AHS provides interoperability between both manned an autonomous trucks. This interoperability is made possible by the system’s two components: FrontRunner, which manages machine operation and guidance, and Dispatch, which handles fleet management, location tracking and production optimization.
Truck brains
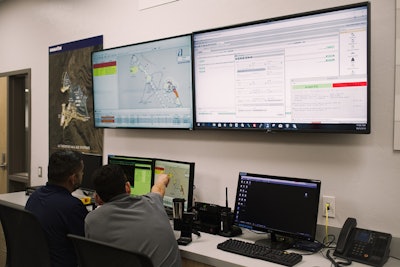
The command station of any mine running AHS is referred to by Komatsu as Central Control. This in-office control center typically consists of two operators monitoring several displays and frequently communicating with personnel in the pit. Anthony Cook, the Vice President for autonomous and communication solutions at Modular, says a good operator can typically operate up to 30 trucks once a mine’s dump and dig locations are all set up and located in the AHS system.
Komatsu took us into its own Central Control at the proving grounds to let us observe the operators in action. To be honest, it was kind of boring. But that’s exactly what Komatsu is going for. One of the primary benefits to AHS that Komatsu names is “precision and repeatability.” The system, according to Komatsu materials shared with the press, promises “precise placement of dumped loads, absolute control of material destinations, (and) consistent haul cycle times.”
“Reducing variability and increasing safety. That’s what automation is all about,” Yureskes says.
“We’re trying to turn this operation into almost a conveyor belt,” adds Cook. “In general, all you need to do is get out of the way and let this system run.”
Standing out from the array of smaller monitors in front of the two operators were two large TVs mounted alongside one another on the wall above them. The monitor on the left displayed autonomous operation data from the FrontRunner control system, while the display on the right was displaying fleet management information from Dispatch.
Though you could argue FrontRunner is the more important part of AHS due to the fact that it’s the piece telling the trucks where to go, Yureskes says that the fleet management side is just as important to the system as a whole. In fact, it’s probably best to think of FrontRunner and Dispatch as two sides to one brain.
“Autonomous systems need to work in tight conjunction with optimized fleet management to realize maximum benefits,” he says. After all, Dispatch is the part of the brain that keeps track of the locations of the assets, their assignments and the locations of dump and loading points. If FrontRunner is the pilot in the AHS system, Dispatch is the navigator, allowing FrontRunner to safely operate each autonomous truck, while also keeping track of their locations and that of any manned assets in the area in order to avoid collisions or other accidents.
The FrontRunner setup
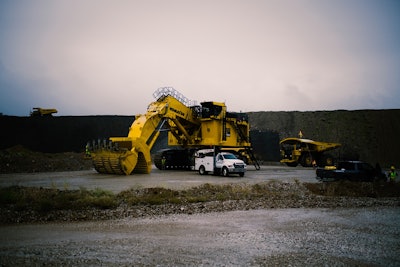
Autonomous control through FrontRunner requires trucks to be outfitted with a control cabinet, located just behind the seats inside the cab; wireless antennas for Wi-Fi and LTE connectivity; and for positioning, GPS, a set of gyroscopes, radar and lasers.
Komatsu says autonomous mining trucks can be ordered with all the needed equipment direct from the factory, but also offers a retrofit service for existing trucks already in the field. Joe Shoemaker, senior product manager for electric dump trucks, says the retrofit process can take as little as one week on newer trucks or up to three weeks on older models.
Komatsu says there are five primary elements to the way FrontRunner safely operates trucks and controls traffic on mine sites:
- Auto Interaction: This is what Komatsu calls communication between autonomous haul trucks inside the Autonomous Haulage System. By talking to each other, the trucks can navigate intersections and find dump and load locations.
- Manual Vehicle Interaction: This allows manned vehicles in the system to communicate with unmanned haul trucks. FrontRunner keeps track of manned vehicles in relation to unmanned trucks and can tell when they are traveling, passing or parking. The system makes autonomous operation and interaction decisions based on this information and the location of manned machines.
- Collision Detection System (CDS): Using a ‘Safety Envelope’ that surrounds each machine, the CDS can detect when the borders of these digital bubbles cross each other and signal a warning.
- Obstacle Detection System (ODS): Equipped with an ODS unit in front and back, manned an unmanned machines in AHS will come to a stop if one is detected.
- Emergency Stop Button (ESB): This button stops all FrontRunner-controlled autonomous haul trucks in operation. Central Control, all autonomous trucks and all manned vehicles in the system are equipped with an ESB.
All of these elements are illustrated on a display, pictured above, within each manned and unmanned vehicle in an AHS mine. Atop a mapped outline of the pit, the display indicates where FrontRunner is driving autonomous trucks using color-coded paths, bold lines that stretch out from each truck. The display also shows each machine’s safety bubble, allowing every operator to monitor machine proximity at a glance.
Autonomy means meeting in the middle
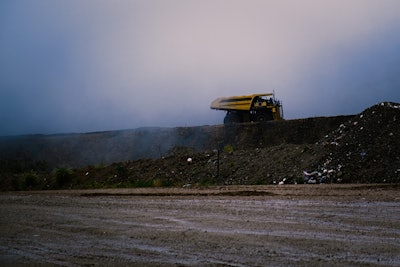
There’s more to bringing autonomy to a mine site than buying or retrofitting the trucks and setting up a Central Control. Komatsu says when a customer buys into AHS, a successful implementation of the system requires the forming of a partnership between the company and that customer.
For its part, Komatsu offers comprehensive, 24/7 support of both the software and hardware.
“Dedicated onsite support is critical,” to the success of the program, says Yureskes. “The mines that get the most benefit out of it are where the lines between the customer and Komatsu become blurry.”
From customers interested in bringing autonomy to their mines, Komatsu asks that they do their due diligence in ensuring they implement good mine planning practices. “Autonomous technology won’t remove inefficiency from a mine site,” Yureskes says. “If you have generally poor mine planning you’re not a great candidate for AHS.
“When you automate junk what you get is automatic junk.”
Yureskes outlined what Komatsu considers good qualities for an AHS-ready mine:
- Ability to segregate autonomous operation from everything else. Yureskes says autonomous truck operation areas must be secured with proper signage and barricades to ensure that only authorized personnel and equipment are able to enter the working area.
- Personnel trained in FrontRunner procedures and safety
- Simple Fixed Courses: Fixed courses allow for FrontRunner to better guide autonomous trucks and optimize production.
- Flexible Intersection Planning: For example, Komatsu has found that using ‘Y’ intersections helps autonomous trucks maintain speed and reduce interaction between autonomous trucks, thus increasing efficiency.
- Wide Roads and Dumping Areas
- Well-Maintained Haul Roads
- Minimized Manned Vehicle Interactions
To aid customers in meeting these requirements, Yureskes says Komatsu provides extensive consultation throughout the process of implementing AHS on a mine. “We do workshops of all the different applications and how they’re going to use it,” he says.
Paradigm shifted?
With the proven success of AHS in both testing and real-world environments in mind, along with the extensive preparation and work required from both Komatsu and its customers to implement the system, what does it all mean for the state of autonomy?
After talking with Cook, it’s clear that Komatsu believes autonomy is close to reaching an important level of maturity within the mining industry. Another sign of that confidence is the fact that they invited media to poke around inside the Arizona Proving Grounds in the first place.
Though Komatsu officials were reluctant to discuss what their success with autonomy means for the technology as a whole, they did point out the tough challenges inherent to the automotive and trucking industries that simply aren’t present in mining, or are present but at a much more manageable scale.
The key, as illustrated by the list of AHS requirements above, is creating a controlled environment. How car and truck makers will cope with infrastructure controlled by local law enforcement and federal and state departments of transportation, is anyone’s guess. Komatsu’s solution is a marriage of both human planning and comprehensive integration of software and hardware throughout the pit.
“There is sort of a paradigm shift that people need to get through,” Cook says. “But people have recognized that the technology has become more commoditized. They’ve accepted that the technology works and the level of inquiry is now much higher than it used to be.
“Now that we’ve come out of the latest (mining) trough, and there’s a lot more activity, autonomy has certainly become more a part of our customers’ buying process. While we used to only see interest in from the bigger mining companies, now we’re seeing it from the smaller ones as well.”
With a firm grasp of the technology and increasing customer interest, Cook says Komatsu is pushing forward with the technology, seeking to expand it and bring elements of it to other mining machines. The company’s intriguing Innovative Autonomous Haulage Vehicle, currently under development and the first mine truck designed to be cab-free, is one example. Cook notes another: Komatsu recently began testing a PC7000 shovel for teleremote operation at the proving grounds.
“We want to bring this technology to water carts and every other part of the mine,” he says. “But the order in which we develop that is going by what’s going to add the most value right now.”