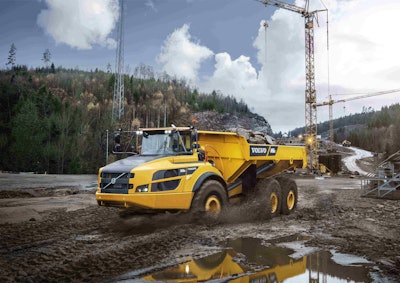
For decades, the average size of articulated dump trucks (ADTs or artics) has been creeping up. Where once 24-ton machines were considered the standard size, 35-ton machines are the new benchmark. And the over-39-ton size category now sports 17 models (see chart).
Maryanne Graves, ADT product manager, John Deere, says many improvements reflect the fact that ADT operators can be the least experienced, least trained of all operators on a work site.
Better drivetrains
Among the new features on Volvo ADTs are Volvo Dynamic Drive and Volvo Engine Brake (VEB) systems. Dynamic Drive matches transmission characteristics to the gradient of the slope and the payload. With Dynamic Drive, the machine will automatically detect when to choose a higher starting gear and when to shift up earlier. Or based on conditions, the truck may hold a lower gear longer, maximizing rimpull. Dynamic Drive can provide a 3- to 10-percent fuel efficiency improvement, depending on the model.
Maintaining traction is always a challenge for an ADT. Most manufacturers use locking differentials and axles. These are effective, but Komatsu took a different approach with their Komatsu Traction Control System (KTCS), which applies the hydraulic brake to the wheel that’s spinning and transfers power to the wheel that is not spinning. “The concern with locking diffs and locking axles is that, when engaged, they can create significant understeer,” says Bruce Boebel, senior product manager of wheeled products, Komatsu. “With locks on, ADTs tend to plow ahead; whereas, with KTCS, traction is improved while the operator maintains much greater steering control.” Boebel says KTCS, which is in place on the first and second axles, also extends tire life and therefore reduces tire costs.
Bell chose to remove the transmission retarder on the large trucks and provide automatic retardation in the brakes instead. One of the reasons is that the engine and transmission combination on the new series is longer, but Bell says the change also improves functionality for operators.
The operator can set the percent of retarder from 0 to 100. At 0 percent, retarder function is fully automatic, and Bell recommends operators use this setting. Because retarder action relies on oil shear in the space between the discs, there is no additional wear to the discs. The brake system has a dedicated hydraulic circuit providing filtration and cooling. The fan for the cooling system is software controlled to find the best balance between cooling, performance and fuel consumption.
The Doosan DA40-5 has multiple drivetrain improvements. A bolt-on rear differential replaces the previous one-piece rear axle, reducing power loss to the wheels. Improved gear ratios reduce axle speed, extend component life and minimize vibration. The sum of the changes equals better operator comfort and improved fuel efficiency.
Better dumping
Dumping the bin requires several steps, but they’re the same steps over and over all day long and are therefore perfect for automating with advanced electronics. Scott Thomas, product application specialist, Caterpillar, cites the assisted dump feature found on the 745 and 745 EJ as an example. “When the assist feature is turned on, pulling the hoist lever past a detent will bring the truck to a stop, apply the wait brake, set the engine to high rpm and raise the bed or activate the ejector automatically. This speeds up the dumping process and reduces cycle times while also lowering operator fatigue.”
Palermo says Volvo’s Dump Support System allows the operator to see the percentage of side inclination of the truck and set allowable parameters for safe dumping operations. The feature can be configured three ways: off, on with an alarm, and on with an alarm and a complete bed stop.
Better everything
When transitioning their two ADTs to the new -5 Series, Doosan improved visibility with sloping hoods, rearview mirrors with a field of view that goes to the center tires and a rearview camera. Heating and air conditioning, ergonomic controls and an air-suspension seat are all standard equipment.
While owners continue their trudge toward accepting telematics, manufacturers are leveraging the technology to everyone’s advantage. Where early telematics simply reported out-of-range conditions, current designs such as John Deere’s JDLink are all about overall machine health. The dealer and the factory both have roles in the program, but they’re different roles. “The information collected is the same but used differently by the dealer and the factory,” says Graves. The dealer looks at performance factors for individual machines to help customers derive the greatest value from each truck, she says, while the factory looks for trends by model across the entire customer base.
Matching the type of truck to the application is key. “With good haul roads, a rigid frame truck is likely a more economical approach on a cost-per-ton basis,” says Komatsu’s Boebel. “But where there are poor jobsite ground conditions and an articulated truck is the right choice, customers will find that new models provide advantages in every area of operation.”