Fill out the team
Pavers remain the cornerstone of a road contractor’s arsenal, but is another full-time member primed to join the equipment team?
By Mike Anderson
If you’re a paving contractor, no doubt you’re used to having milling equipment working at your jobsites. The use of cold planers as part of the road rehab and building process is almost as established as employing compactors and pavers. What’s different now though, say equipment manufacturers, is you may be looking to own that milling gear yourself, if you don’t already.
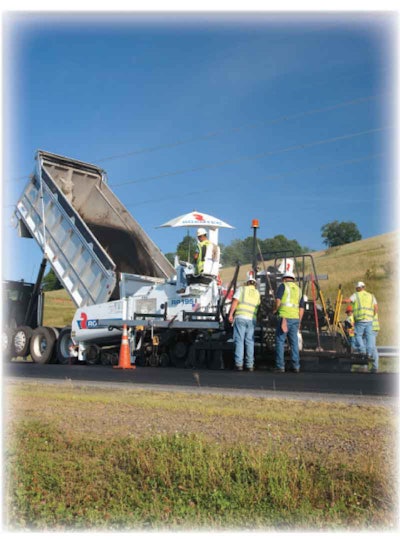
“Yes, yes,” Volvo’s Eric Fatyol says emphatically, “that is a trend occurring across the country. Milling contractors tend to go to their bigger customers first, where they can get in and out of jobs quickly and get their money. Smaller paving contractors are finding it hard to hire milling contractors who are going to be there when they need them, so those guys are going out and buying their own machines.”
It is “very common” for roadbuilding contractors to acquire their own milling machines rather than sub-contract the milling process out, agrees BOMAG’s John Hood. “Owning a cold planer offers them the ultimate flexibility and profit potential by giving them the ability to control the entire process without coordination from an outside vendor.”
Many mill-and-resurfacing projects today are done at night and require paved – not grooved – lanes to be reopened to traffic by an early hour, explains Jeff Wiley, senior vice president, Wirtgen America, “or substantial liquidated damages may be incurred. Moreover, these paved lanes likely will have to meet stringent smoothness criteria in order to qualify for bonuses, which often are the key to profitability as they are figured into the bid price by the contractor. It’s incumbent on the contractor to match paver performance with mill performance. Our products give contractors the high-performance equipment they need to meet deadlines, optimize smoothness and win bonuses.”
All major paver OEMs now offer milling machines (see Machine Matters More Roundup.) In addition to the possibility of an outside milling contractor not being available when needed, hiring one usually means paying for the operator and even a support person, says Fatyol, product specialist, paving and milling for Volvo. The operational cost savings, combined with today’s easier to operate machine controls, makes buying a milling machine more appealing to paving contractors, he says. “It’s still a high-maintenance item,” he says, “but they understand what it takes. These contractors are used to doing a lot of maintenance – look at a paving machine.”
We’ll first look at the paver part of this team, then examine milling machines starting on page 32.
The evolution of pavers
The cornerstone product for any roadbuilding contractor, the paver, continues to evolve. “There definitely is style to these Vision Series machines,” says Brodie Hutchins, general manager of Wirtgen America’s Vögele division, which represents one of eight brands offering tracked asphalt pavers at 125 horsepower and over (see Machine Matters Roundup on page 24). “There is a flat deck, streamlined hopper wings, and raked exhaust stacks coming out the back. As we solved technical requirements, we were able to address aesthetic design issues as well.”
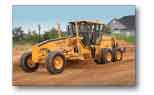
In developing the Vision Series, Vögele looked at “the specific requirements demanded by contractors in the United States, and at our existing technology as a global market leader,” says Hutchins. “We integrated proven Vögele technologies such as our conveyor and auger feeder systems, and screed assist, and put them into a package for North America, which required a platform that was lower and wider than seen in Europe. There is a clean-sheet design, yet leveraging proven Super Series technology.”
That technology includes the paver’s electrical system, says Hutchins: “Instead of a hodge-podge system, our electrical system was designed by us and we own the technology.” This includes the optional five-sensors-per-side Niveltronic Plus grade and slope system, meaning all sensors connected are recognized automatically, and can be controlled and monitored from the screed operator’s console. “All hardware and software are built into the paver,” says Hutchins. “It’s a Vögele design; other aftermarket electronic systems also may be used, but the Vision Series was designed with Niveltronic Plus in mind.”
Technological advances
Other industry leaders boast technological advances:
• The Caterpillar Paving Products division, which correspondingly offers paver models under the Caterpillar and Barber-Greene brands, makes machines available with the option of factory-installed Cat Grade and Slope Control, which is designed to work with assorted sensors in various applications. Including the highway-class Caterpillar AP1055E and Barber-Greene BG1055E being introduced this year with Tier 4 Interim engines, the pavers can also be equipped with the optional Cat Product Link fleet management system. Such packaging, says Caterpillar, allows the authorized dealer to be a single source for sales, parts and service for the entire machine.
• With Terex pavers, a rear frame raise system not only accommodates truck unloading, but allows operators to adjust the head of material at the spreading augers to reduce segregation. A three-point suspension system isolates the frame from the drive system to “float” the machine over any irregularities in the sub base, maintaining a consistent feed height at the screed and, thus, a smoother mat. The Smartrac tensioning system automatically maintains proper tension on the rubber track at all times, in forward and reverse.
• The auger assembly on Roadtec pavers can be hydraulically raised and lowered to help eliminate segregation and assist in loading and unloading. Augers are controlled by standard sonic feed sensors, and the auger chain case width has been kept to a minimum to further reduce segregation. All Roadtec pavers feature a 13-inch-high conveyor opening. Each conveyor is independently driven so that material delivery can be finely tuned for each side.
With tracked pavers, having a large footprint is important, says Volvo’s Fatyol. “You don’t have as much jerkiness as you’re paving. That’s one thing you don’t want is that back-and-forth motion, because it creates speed bumps and other problems with your mat.”
And that, all paver manufacturers point out, costs contractors bonus money. EW
Machine Matters Roundup
VOLVO
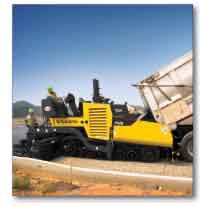
PF4410
• 158 gross horsepower
• 31,500 pounds operating weight
• 8’0” basic screed width
• 25’0” maximum paving width
PF6110
• 205 gross horsepower
• 47,614 pounds operating weight
• 10’0” basic screed width
• 26’0” maximum paving width
ABG7820
• 231 gross horsepower
• 40,022 pounds operating weight
• 8’2” basic screed width
• 32’8” maximum paving width
ABG8820
• 247 gross horsepower
• 46,416 pounds operating weight
• 8’2” basic screed width
• 42’8” maximum paving width
ABG9820
• 371 gross horsepower
• 57,080 pounds operating weight
• 9’10” basic screed width
• 52’5” maximum paving width
The wide Volvo asphalt paver offering available in the market is the result of two product heritages acquired by the company – the U.S.-sourced Blaw-Knox PF Series machines formerly of Ingersoll Rand and the ABG Series machines from Germany. Among the tracked machines, the 10-foot-class PF6110 has a claimed per-track footprint measuring 136 inches in length and 19 inches wide, which Volvo says is the industry’s largest, providing even weight distribution and improved flotation. The undercarriage was redesigned using heavy-duty, traction-drive technology and a new tandem-bogie weight distribution system providing traction during paving operations yet comfortable steering in travel mode.
BARBER-GREENE
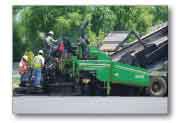
BG555E (new)
• 142 gross horsepower
• 35,810 pounds operating weight
• 8’0” basic screed width
• 20’2” maximum paving width
BG655D
• 174 gross horsepower
• 40,234 pounds operating weight
• 8’0” basic screed width
• 20’2” maximum paving width
BG1055E (new)
• 225 gross horsepower
• 44,167 pounds operating weight
• 10’0” basic screed width
• 24’2” maximum paving width
With models corresponding exactly to the asphalt pavers in the Caterpillar product lineup, Barber-Greene tracked machines likewise feature Cat’s Mobil-Trac undercarriage for optimized turning capability and travel speed, Advisor Display for fingertip access to machine performance data, diagnostics and job planning tools, and a standard fume ventilation system. Barber-Greene pavers can be equipped with Caterpillar’s Product Link fleet management system and factory-installed Cat Grade and Slope system. Alongside the Caterpillar AP1055E, a new Barber-Greene 10-foot-class model, the BG1055E, will be released this June.
DYNAPAC
• 220 gross horsepower
• 45,000 pounds operating weight
• 10’0” basic screed width
• 26’0” maximum paving width
Just over a year ago, Atlas Copco’s Dynapac brand launched an asphalt paver family designed specifically for the North American market, including the 10-foot-class tracked F1000T model. Design features include an outboard auger drive system, balanced undercarriage and a wide-width conveyor that, the company explains, eliminates the auger chain drive box and cuts out centerline segregation. Furthermore, the use of relay logic controls means no computers to troubleshoot, says Dynapac. Operator vision to the hopper and mat is improved with dual swing-out operation station and a flat operator’s area. The highway-class Dynapac tracked asphalt paver is powered by the 6.7-liter Cummins QSB engine used in other 10-foot-class paver makes and models.
LEEBOY
• 130 gross horsepower
• 25,000 pounds operating weight
• 8’0” basic screed width
• 15’6” maximum paving width
The largest tracked asphalt paver model offered by compact paving equipment manufacturer LeeBoy, the 8816B comes standard with the company’s heavy-duty Legend II screed system, featuring electrically-heated main screed and extensions. With its 10-ton-capacity receiving hopper served by independently-controlled slat feed conveyors, the 8816B is driven by a hydrostatically-powered, self-cleaning track with hydraulically-adjustable front idlers. Dual slide-out operator stations, common on the largest pavers in the market, enhance visibility to the paving area for the LeeBoy paver’s operator. Dual electronic control stations offer either right- or left-hand control of all paver functions.
VOGELE
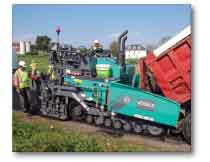
Vision 5100-2
• 170 gross horsepower
• 34,050 pounds operating weight
• 8’0” basic screed width
• 19’0” maximum paving width
Super 1800-2 SprayJet
• 174 gross horsepower
• 45,856 pounds operating weight
• 8’4” basic screed width
• 19’8” maximum paving width
Vision 5200-2
• 240 gross horsepower
• 34,400 pounds operating weight
• 10’0” basic screed width
• 25’6” maximum paving width
Super 2100-2
• 244 gross horsepower
• 47,179 pounds operating weight
• 8’4” basic screed width
• 42’7” maximum paving width
In addition to the tracked asphalt pavers listed above, identified by parent company Wirtgen as “primary North American models,” Vögele offers the Super 1600-2, Super 1800-2 and Super 1900-2 models with basic screed widths of 8 feet 4 inches, as well as a new flagship model, the highway-class Super 3000-2. With a maximum laydown rate of 1,600 tons per hour, the 402-horsepower Super 3000-2 replaced the 366-horsepower Super 2500, offering multiple-material paving widths ranging from a basic 9 feet 8 inches to a maximum 52 feet 6 inches. “Clean-sheet designed,” Vision Series machines have self-diagnostics, independently-operated hopper wings, and reversible augers and conveyors.
ROADTEC
• 174 gross horsepower
• 33,220 pounds operating weight
• 8’0” basic screed width
• 15’6” maximum paving width
RP-195
• 225 gross horsepower
• 43,000 pounds operating weight
• 10’0” basic screed width
• 19’6” maximum paving width
SP-200
• 225 gross horsepower
• 62,500 pounds operating weight
• 10’0” basic screed width
• 19’6” maximum paving width
In addition to standard 8- and 10-foot-class tracked asphalt paver models, Astec’s Roadtec brand offers the SP-200 “spray paver” that, in a single process, lays a tack coat down directly in front of the asphalt mix. Software has since been upgraded on the SP-200 to provide a more intuitive control interface, says Roadtec. On all company paver models, the cooling package is mounted on the machine’s side, where it can capture the cleanest and coolest air. Sauer-Danfoss 90 Series variable-displacement pumps are used, “since the larger capacity enables them to run at a more optimal speed, which permits them to run cooler and increase their life,” says Roadtec marketing manager Eric Baker.
CATERPILLAR
• 142 gross horsepower
• 35,810 pounds operating weight
• 8’0” basic screed width
• 20’2” maximum paving width
AP655D
• 174 gross horsepower
• 40,234 pounds operating weight
• 8’0” basic screed width
• 20’2” maximum paving width
AP1055E (new)
• 225 gross horsepower
• 44,167 pounds operating weight
• 10’0” basic screed width
• 24’2” maximum paving width
To be released in June, the 10-foot-class AP1055E powered by the Cat C7.1 engine with ACERT technology will be the first tracked asphalt paver available that meets Tier 4 Interim emissions standards, says Caterpillar. For reduced fuel burn, the new highway-class paver model will feature Eco-mode and automatic engine speed control. All Caterpillar asphalt paver models boast electronic engine power management, which manages the load on the engine and material handling system. In case of overload, engine and feeder performance is automatically modified to prevent stalling. Each model is available with factory-installed Cat Grade and Slope.
TEREX ROADBUILDING
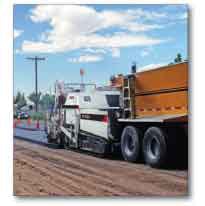
CR362L
• 160 gross horsepower
• 31,450 pounds operating weight
• 8’0” basic screed width
• 20’0” maximum paving width
CR462
• 220 gross horsepower
• 38,700 pounds operating weight
• 10’0” basic screed width
• 28’0” maximum paving width
CR562
• 260 gross horsepower
• 40,415 pounds operating weight
• 10’0” basic screed width
• 30’0” maximum paving width
CR662RM
• 260 gross horsepower
• 48,300 pounds operating weight
• 10’0” basic screed width
• 30’0” maximum paving width
Each available in assorted model versions, the Terex CR400, CR500 and CR600 Series pavers have been updated with Tier 4 Interim engines, to be integrated into production throughout 2011. This, the company says, has been accomplished with only minor modifications to the engine and cooling systems. Radiator and cooling fan sizes have increased, but space has been left under the hood for the module required in three years for Tier 4 Final, resulting in a “minimal” increase in hood height. The operator’s seat has been raised by the same amount, thus preserving visibility, says Terex Roadbuilding. The CR662 RoadMix paver/material transfer vehicle is now fully lined with a Ni-Hard cast liner.