California postpones enforcement of its off-highway emissions rule, leaving contractors wondering what to do next.
By Marcia Gruver and Mike Anderson
Editor’s note: This is the first part in a series of articles on California’s off-highway emissions regulations and their potential impact on the rest of the country.
California’s contractors can be excused if they’re a bit confused these days. For the past decade, the California Air Resources Board has been promising – and then delivering – a strict set of regulations governing off-highway equipment emissions. Enforcement for large contractors, identified as having fleets of heavy equipment such as dozers, scrapers and excavators with more than 5,000 total horsepower, was to start March 1.
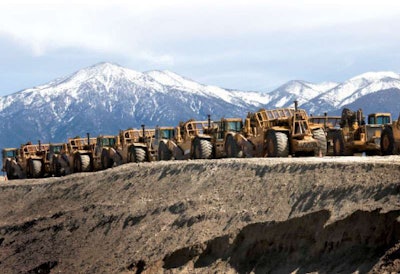
But on Feb. 11, James Goldstene, CARB executive officer, temporarily called the whole thing off. “Effective immediately” and “until further notice,” he said, no enforcement action would be taken for non-compliance on the rule, approved by CARB in July 2007. (See “The CliffNotes version of CARB” sidebar on page 18.)
CARB placed the reason for this decision squarely on California’s devastated construction economy. “The construction industry has felt the sting of the faltering economy with reduced activity and idled off-road equipment,” said Goldstene in the February announcement. “This has made it difficult for contractors to pay for required clean-air upgrades for their fleets.”
It was, in the words of Bill Davis, executive vice president of the Southern California Contractors Association, a “scammy little” press release. “The truth is they don’t have enforcement authority under the Clean Air Act without a (federal) EPA waiver,” he says.
CARB admits the EPA waiver is critical. “EPA authorization is required before we can enforce requirements of the regulation,” says Kim Heroy-Rogalski, manager of CARB’s Off-Road Implementation Section. “Those performance requirements include all requirements to retrofit or turn over vehicles as well as restrictions on adding lower tier vehicles.” But CARB may get its wish sooner rather than later. EPA will conduct a public hearing on the waiver April 14, and invites comments through May 18.
Construction’s downward spiral in the state has called into question some of CARB’s basic assumptions when creating the rule. Now the uncertainty of when – or if – the CARB enforcement hammer will fall has many California contractors questioning the tremendous effort and expense they’ve made to comply.
Testimony time
As part of its February announcement, CARB issued an invite to a quickly-called March 11th CARB executive officer hearing: tell us your stories, it said. Tell us what impact these regulations have had on your company.
But contractors have been doing just that throughout the rulemaking process. Their letters, emails and attachments are part of the official proceedings during several years of CARB meetings discussing the off-highway rule.
At the hearing, Mike Shaw was the first contractor to take the podium (for video comments by Shaw and others at the meeting, go to EquipmentWorldDigital.com). Shaw is president of earthmoving contractor Perry & Shaw, located in San Diego County. “Ninety-five percent of our revenue is generated by self-performed work,” Shaw said, “and all of that revenue is generated by the use of heavy equipment. So, this rule is particularly onerous on our operation.”
Tom Foss, president and chief operating officer of infrastructure contractor Griffith Company, Brea, told the hearing he’d like to see a five-year delay in enforcement of the regs. “Five years allows the technology to catch up,” he said.
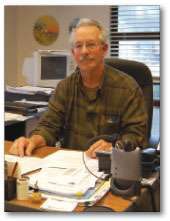
On the day Foss testified, CARB’s chairperson, Mary Nichols, was on a Griffith jobsite viewing Komatsu’s new hybrid diesel electric excavator that can cut fuel consumption and emissions 20 to 40 percent. Foss noted he had just met with another manufacturer about a hybrid dozer coming on line.
But such technology is expensive and still relatively rare. Manufacturers have only fielded a handful of hybrid machines thus far.
An enforcement delay, Foss said, would allow contractors to replace equipment – upon natural retirement – with the newest and most efficient machines available. “We’ve budgeted to spend about $1.5 million just in diesel particulate filters and repowers to try to get compliance over the next two years,” he added. (Diesel particulate filters are retrofitted to existing equipment to reduce particulate matter emissions; repowers directly replace an older engine with a newer emissions-compliant engine.)
Norman R. (Skip) Brown, president of Sacramento-based Delta Construction, reiterated previous comments at the CARB hearing: businesses such as his are doomed under CARB’s off-highway regulations. “This 67-year-old company will succumb to these regulations, period,” he said. “It will affect the small and medium-sized businesses worse, because they don’t have the capital to replace machines. I have $3 million worth of stuff now worth probably $300,000.”
Brown has seen – and survived – four recessions prior to this one, because an asset, once owned and paid for, allowed Delta Construction to pick right back up with the return of work. According to Brown, the difference this time is that, under California emissions regulations, those assets “vanish” and are not simply parked for a while.
In the ditch
Adding to the impact of the emissions regulations is a global recession that has hit California contactors hard. From a 2006 volume of $50 million-plus, for example, Perry & Shaw’s revenues now hover around $7 million. The company used to have 175 operating engineers; it now has 15. “We’re tucked in as tight as we can be,” Shaw says.
Perry & Shaw is hardly alone in its economic woes. In 2006, McKenna General Engineering, Corona, had $30 million in sales; today it’s at the $6 million mark. The company has laid off 150 employees, reducing its ranks to 50, estimates president Tim McKenna.
“We’re down 50 to 60 percent compared to 2006,” says Don MacIntosh, president, A.L. MacIntosh, Pico Rivera. Major markets for the site development contractor have “disappeared and private sector work is almost non-existent,” he says.
Fully one-third of the state’s construction industry has disappeared since its peak mid-decade, says the Associated General Contractors of America.
And the longer-term outlook is no rosier. At the hearing, Dr. Lynn Reaser, president of the National Association of Business Economics and chief economist for Point Loma Nazarene University, said California’s construction industry “will remain a shadow of itself for years to come.” Even if the economy heals more quickly than expected, Reaser told the board, the state’s construction industry would likely employ fewer than 700,000 in 2015, compared to more than 900,000 in 2006.
Relief in the numbers?
CARB’s off-highway rule is based in part on an emissions inventory the agency did in 2000 when the California construction industry was experiencing steady growth. This past December, AGC submitted its own emissions inventory, one that raised serious questions about the methodology and assumptions of the 2000 inventory.
In making its assertions both in December and during the March meeting, AGC used numbers taken directly from CARB’s Diesel Off-road On-line Reporting System, or DOORS, which requires contractors to give detailed information on each machine and engine in their fleets. All California construction fleets, no matter the size, are mandated to give information on each machine, including the vehicle type, serial number, in-house vehicle number, manufacturer, model, model year, engine serial number, engine manufacturer, engine model, engine family and horsepower. If you’ve installed a Vehicle Diesel Emission Control Strategy (or VDEC, such as a diesel particulate filter) or repowered, you’ll need to fill out some additional blanks.
Ironically, this reporting onus has formed the foundation for one of the industry’s strongest arguments against the rule.
Using the DOORS information, and employing the exact same methodology CARB used in 2000, AGC and its consultant Sierra Research came up with far different conclusions. The association contends that certain assumptions in CARB’s model are “demonstrably wrong and they grossly exaggerate even the latest estimates of emissions from the construction industry.” (See “What a difference a decade makes” chart.)
“We’ve budgeted to spend about $1.5 million in diesel particulate filters and repowers to try to get in compliance over the next two years.”
– Tom Foss, Griffith Company
According to AGC, their inventory shows the off-highway rule is not needed to satisfy the state implementation plan for reducing either NOx or PM emissions. The rule sought to reduce NOx emissions for regulated fleets to 298.4 tons per day in 2010 and to 273.3 tpd in 2011. AGC’s analysis shows without the rule, NOx emissions will be down to 222.5 tpd in 2010 and to 210.9 tpd in 2011.
On the PM side, without the rule, PM emissions will be 12 tpd this year, when the rule sought a level of 14.4 tpd, and at 11.7 tpd next year, slightly above the rule’s sought level of 11.4 tpd. These lower levels are due in large part to the state’s faltering construction economy.
Life under CARB
All of this may be too little, too late for some large contractors, who thought they were under a March 1 enforcement gun this year. Many large fleet owners – identified by CARB as having a fleet with more than 5,000 total horsepower – have been preparing for years to comply with these regulations. For these fleets, the regulations have not only meant a complete realignment of their fleet strategy, but of the way they do business.
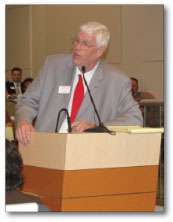
Perry & Shaw, for example, has seen its share of construction’s cycles. “When the economy goes down, we generally park our fleet and wait for business to come back,” says Mike Shaw. But this time the company faced not only CARB’s new rules but a rapidly deteriorating in-state used equipment market.
When Shaw started studying CARB’s then-proposed rules, he knew prices for used equipment would take a hit. “So we decided in 2006 if we were going to sell, we’d better do it now,” Shaw says. The company sold scrapers, dozers, loaders, rock trucks and other machines, primarily through auctions, going from 110 machines down to 45. Although unhappy at the time with the prices he got, Shaw now looks back and thinks he did well. “I never would have thought I’d have seen prices go as low as they’ve gone,” he says, “which has been a function of both CARB and the economy. In 2006, some Cat 657E scrapers with 1,000 hours on them sold for about $1.2 million each. In 2007 and 2008, similar machines sold in the $800,000 range and recently there have been some in that range selling for less than $200,000.”
McKenna General Engineering got hit with this used equipment price free fall when it started selling its Tier 0 equipment in 2007 and 2008, reducing its fleet from around 80 machines down to 25. “We got destroyed,” says Tim McKenna, president, “It was a significant loss.”
Repowering
For most of the decade, large-fleet companies have also been busy repowering their fleet, putting new emissions-compliant engines into existing equipment. Between 2002 and 2006, Perry & Shaw repowered 44 engines, which cost around $5.5 million, subsidized in part by California’s Carl Moyer incentive grant program. The program, administered by CARB provides incentive grants for cleaner-than-required engines, equipment and other sources of pollution. (For more information, go to www.arb.ca.gov/msprog/moyer/moyer.htm.) “The repowers made sense and we had lots of business at the time,” Shaw says.
Shaw’s initial repowers swapped out Tier 0 for Tier 1 engines, which he couldn’t add to his fleet today. “When you start compressing these timelines, your costs increase hugely,” Shaw says. “If you can use an engine for 20 years that’s one thing, but if you can only use an engine for five or six years, it’s a totally different thing.”
“We didn’t have any choice in the matter. We spent all that money and we’re stuck and we can’t go backwards.”
–Jim McKenna, McKenna General Engineering
One contractor got so heavily into repowers it made it into an art form. Sukut Equipment, Santa Ana, “made the decision to never rebuild another diesel,” says Michael Bobeczko, director of marketing, Sukut Construction, which rents its equipment from Sukut Equipment. Instead, the company developed a system to repower its equipment in the field – a process that cut downtime from months to days, Bobeczko says.
Sukut Equipment has repowered 175 engines to date, says Eric Schmidt, Sukut’s emissions manager, swapping out a certain portion as each new tier became available. Most of the repowers were funded by the state’s Carl Moyer program, with Sukut paying between 15 to 35 percent of the average $100,000 cost per large engine repower.
In 2006, Sukut had 200 major pieces of equipment. Since then, it has disposed of 20 machines in a variety of ways – selling them at auction and through brokers, and swapping some machines out for newer equipment, an exchange primarily involving trading scrapers for excavators and artics.
Another way
While many contractors facing CARB requirements have reduced their fleet, grading contractor A.L. MacIntosh has increased its fleet from about 30 machines back in 2005 to 51 currently. In 2005, up to 70 percent of the company’s fleet was Tier 0; currently that percentage stands at about 50 percent.
Don MacIntosh, owner of A.L. MacIntosh, explains his strategy: “When we saw the auction prices for used equipment start to plummet, we decided not to sell any machines,” he says. Instead, MacIntosh will use its Tier 0 machines as turn over units, retiring them to meet CARB’s NOx fleet average requirements.
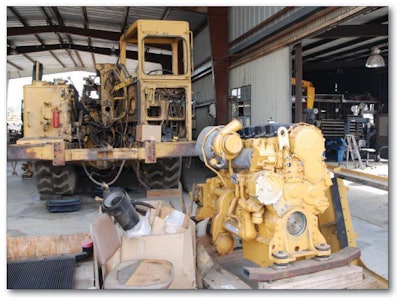
The machines MacIntosh has added since 2005 – bought when times were still good – were either new or late-model used Tier 2 and Tier 3s. Since he estimates his off-road diesel use is now down 32 percent, the credits for reduced machine activity passed by the California legislature in 2009 will put the firm in full compliance this year, and near compliance in 2011.
Last year, the California
Onward
While MacIntosh says the “postponement gives us some breathing room,” Shaw is dismissive. “They didn’t give us anything they didn’t have to give us since they can’t enforce it without the EPA waiver,” he says. McKenna is more resigned. “We didn’t have any choice in the matter,” he says. “We spent all that money and we’re stuck and we can’t go backwards.”
And some contractors find the postponement disappointing. “We’ve invested the time, money and effort in cleaning up our fleet and some of our competitors haven’t and at the end of the day, it hasn’t given us a competitive advantage,” Sukut’s Bobeczko says. “And we’re not the only ones in this position. There are a number of grading contractors who have been repowering their equipment for years. This is not something you can do in a month or a year, it takes time. Those of us who have spent considerable resources in complying with the spirit of the law haven’t been rewarded for it.”
Meanwhile, Shaw wonders how construction’s true tab for CARB compliance could ever be tallied. For example, while Shaw can add up his repower and VDEC installation costs, he says any real calculation needs to account for how he’s had to reconfigure his fleet. “I’ve reduced my fleet capacity for the kind of business I’m in by 50 percent,” he says, “and I can’t get that capacity back in a reasonable amount of time. Buying new machines is cost prohibitive. And even though in retrospect I got a decent return on selling my machines, I would have preferred to park them and wait until business comes back. The value of a machine is the work it gets done, not the resell value. It translates into your net worth, into your bonding ability and into your ability to generate revenue and profit.”
Next month: Even with this postponement, is California’s off-highway rule poised to spread across the nation? EW
The CliffsNotes version of the CARB rule
The California Air Resources Board off-highway emissions rule requires owners of existing fleets of off-road equipment to reduce emissions of NOx (nitrogen oxides) and PM (particulate matter) by retrofitting, repowering or replacing their equipment. If a company cannot meet the NOx fleet average standard for a particular year, it must either discard or turn over 8 to 10 percent of its horsepower in that year. It similarly requires fleet owners who cannot meet the PM fleet average requirements to retrofit 20 percent of their horsepower (total maximum) with the highest level of verified diesel emission control strategy (VDECS, including diesel particulate filters, which capture particulate matter from exhaust as it flows through).
Large fleets, identified as having more than 5,000 total horsepower, were scheduled to meet the first of these requirements this March. Medium fleets, with a total of 2,501 to 5,000 horsepower, are scheduled to begin compliance in 2013; and small fleets, under 2,500 total horsepower, in 2015.
The penalties for noncompliance to this rule could be significant, including fines of up to $10,000 per vehicle per day for PM violations and $500 per vehicle per day for NOx violations.
The first federal emissions standards – now called Tier 1 – for off-highway engines were phased in from 1996 to 2000. These standards dictated allowable levels of pollutants – including NOx and PM – from engine emissions. In 1998, EPA announced Tier 2 and Tier 3 standards, with phase-in schedules from 2000 to 2008. EPA signed the final rule for Tier 4 standards in 2004, to be phased in from 2008 to 2015. Tier 4 standards require NOx and PM emissions be reduced about 90 percent from Tier 3 levels.
–Taken from AGC’s January 11 emergency petition for a two-year deadline extension of CARB’s off-highway regulation and other sources.
What’s next?
Partly in response to a petition made by the Associated General Contractors of America on behalf of its California chapters, CARB has established a timeline that will lead to what its staff calls appropriate changes by late summer or early fall to the state’s in-use off-road diesel-fueled fleet regulation. Kim Heroy-Rogalski, off-road program manager, confirms the evaluation is taking into consideration one of the bones of contention formally raised by AGC. “We’re also evaluating some new information regarding the off-road inventory methodology that came to light earlier this year,” says Heroy-Rogalski, who laid out a program review timeline that would progress to CARB’s April board meeting, then to public workshops in May and June, and finally to the board’s consideration of rule revisions in August or September. For a current list of meetings, go to www.arb.ca.gov.
What a difference a decade makes
When CARB projected the state’s off-road NOx and PM emissions in 2000, the construction industry was about to embark on a six-year growth spurt. AGC’s 2009 inventory, based on CARB’s DOORS data, tells the story of an industry that’s now near idle – and emitting far less pollutants than CARB initially forecast, or even sought with its off-road emissions rule.
2010 NOx emissions (measured in tons per day)
311 tpd — CARB 2000 estimates of emissions from regulated fleets
298.4 tpd — Limit sought in off-road rule
225.5 tpd — AGC/DOORS 2009 emissions inventory
2010 PM emissions* (Measured in tons per day)
16.69 tpd — CARB 2000 estimate of emissions from regulated fleets
14.4 tpd — Limit sought in off-road rule
12 tpd — AGC/DOORS 2009 emissions inventory