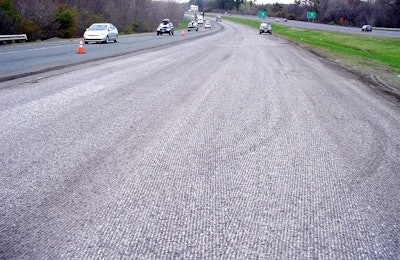
Doing more with less and aggressively seeking new ways to stretch budget dollars are how many businesses respond to a tough economic climate. Federal and state highway and transportation departments are no exceptions. Fortunately, academic research and equipment technology communities together have some promising results to share.
The National Center for Asphalt Technology (NCAT) on the campus of Auburn University (Auburn, Ala.) recently completed a study for the Alabama Department of Transportation (ALDOT) showing that pavement design standards used by many state transportation agencies for decades can be updated to reflect new asphalt material mixes and roadbuilding methods.
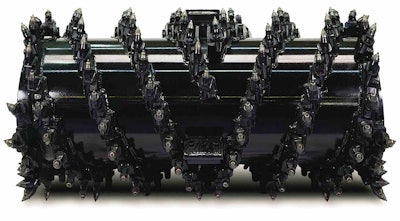
Specifically, after thoroughly testing various asphalt layer coefficients on its test track, NCAT’s results determined asphalt pavements can be safely built about 18 percent thinner. This means more highway departments can build and resurf
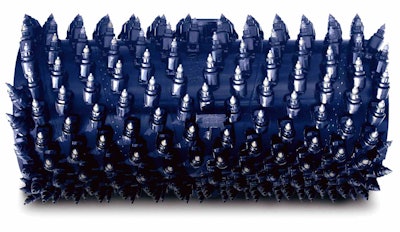
ace more roads without suffering any degradation in road performance.
Such new standards are also leading to new road-repair efforts to help stretch maintenance dollars. Traditional mill-and-fill efforts involve using road-milling machines with standard-spacing road-milling drums (bits spaced 5/8 inches or roughly 16 mm apart) to remove pavement for rebuilding. A new alternative, fine milling, involves swapping out a
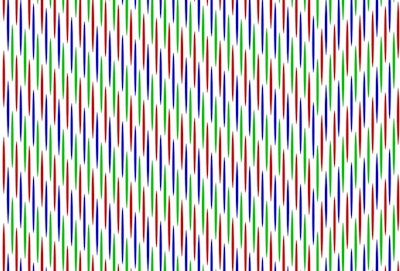
standard road-milling drum for a fine-milling drum with much tighter tooth spacing, 0.3 inches (8 mm) or less. This permits removing only a minimal depth of road surface depending on conditions and replacing it with thin hot-mix asphalt (HMA) overlays. Using thin HMA overlays can stretch maintenance budgets, but also requires fine-milled surfaces so the surface’s peaks and valleys don’t reflect through the new thin overlay.
Fine milling can address other road-repair conditions.
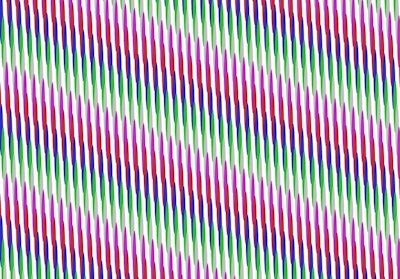
For example, excessive road-mix binder can accumulate on a road’s surface, depending on traffic loads and environmental conditions. This causes a polished surface and increases the chances of accidents due to decreased skid resistance. Where removing the entire road’s surface course and replacing it would have been the conventional solution, fine milling can remove only a top portion of the surface course needing replacement.
Wheel ruts can be efficiently removed by scarifying to a level below the overroll created by traffic and uneven road grades can be quickly fixed. Savings accrue from a number of related areas:
- Less damaged road material needing to be removed
- Less repair material needed
- Milling crews can operate independently from paving crews
- With less material removed and less repair material required, the number of haul trucks is significantly reduced
- Project and contractor costs are more efficiently controlled, expanding the scope and number of repair projects where necessary
How It Works
As previously mentioned, fine milling involves swapping out a milling machine’s standard road-milling drum (bits spaced roughly 16 mm apart) with a fine-milling drum exhibiting more closely spaced bits, 0.3 inches (8 mm) apart or less. Drums also include conical tools, sleeves, and blocks in a range of available styles, including weld-on blocks and proprietary quick-change systems requiring no welding and, in certain applications, no bolts.
Customized drum design can be the key to giving users the productivity they expect. With a wealth of proprietary drum-lacing programs, Kennametal engineers can tailor drum designs to specific customer parameters, with such user-selectable design elements as cutting pattern, diameter, width, advance rate, and rpm. The program then determine the total number of tools required, total cutting width, wrap angle per side, radial spacing, vane angle, throat width, and estimated kicker clearance. Drum configurations for a number of pavement conditions and road machine OEM specifications are also available.
Such operating specs can greatly affect fine milling projects. For example, a faster machine advance speed generally yields a rougher texture while a faster drum rotation (RPM) yields a smoother texture.
Saving Millions in Georgia
The Georgia Department of Transportation (GDOT) recently wanted to repair a distressed open-graded friction course (OGFC) on 15.6 miles of I-75 south of Macon. This project had a dense graded surface mix layer with an overlying OGFC that had been in service for more than 10 years. Although the OGFC had begun to deteriorate, the underlying mix was still in good condition.
Milling only the OGFC and replacing it with GDOT’s porous European mix (PEM) was determined to be the most cost-effective approach. However, this rehabilitation practice had rarely been done in Georgia. The potential existed for poor bonding between the PEM and the conventional milled surface, permitting surface water to flow through the porous layer and become trapped in the valleys of the conventional milled surface, (usually with a ridge-to-valley depth (RVD) of 8 mm or greater). Because of these concerns, Georgia DOT typically placed a costly new layer of dense-graded surface mix over the conventional milled surface prior to the PEM.
Fortunately, GDOT had run tests with the National Center for Asphalt Technology to determine the underlying OGFC was in good shape and became aware of fine milling technology. For the GDOT project, an even finer-spaced micro-milling drum at 0.2 inches (5.08 mm) was used.
GDOT’s texture specification for micro milling on the project included controlling the depth of the micro milled surface to an accuracy of 1.6 mm and maintaining RVD of 3.2 mm or less. Target smoothness was 825 mm/km, not to exceed 900 mm/km.
The fine-textured surface achieved by micromilling along with less than half the previous RVD allowed GDOT to place a new PEM layer directly on the milled surface of the existing dense-graded surface mix, eliminating the need for an additional surface mix layer. GDOT estimated savings of $58,000 per lane mile or a total savings of approximately $5.4 million for the project.
NCAT assisted during the project by evaluating surface texture depths in the micromilled surface using its Ultra Light Inertial Profiler (ULIP) and measuring smoothness with its Laser Road Profiler (LRP). Results indicated that the RVD requirements were achievable with the proper application of a fine-milling drum.
GDOT has been pleased with the cost-effective strategy of using micromilling to remove distressed OGFC and replace it with PEM. The agency has also added software to the LRP to allow determination of RVD values while measuring smoothness.
With micromilling, the end result is a super-fine surface. This surface is for milled surfaces that are left open to traffic. This will provide the best readability. Some states and providences have readability specifications in the ranges that require this type of milling. This milling is normally done with shallow cuts, such as 25 mm to 50 mm deep. Speed is varied to obtain the proper ride spec.
Fine milling is an option more road departments should investigate for effectively removing distressed pavement and eliminating the need for multiple layers (scratch and/or leveling). It also allows considering more options, such as thin-lift resurfacing, not feasible under regular milling methods.
For more on NCAT research, visit www.ncat.us. For more information on fine milling drums, drum designs, tools, and toolholders from Kennametal, visit www.kennametal.com.
This article, written by Nick Gaten, director of marketing for earth cutting tools at Kennametal, was written and contributed on behalf of Kennametal.