Steel and synthetic engineered fibers are enhancing performance in asphalt pavements and concrete.
By Tom Kuennen, Contributing Editor
New research is reaffirming the benefits of steel or synthetic engineered fibers in asphalt pavements and concrete, where they enhance performance, replace fine matter, and in the case of concrete, control shrinkage cracking and keep deicing salts away from reinforcing steel.
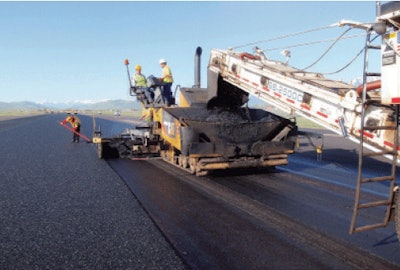
For decades, fibers of all origins have been hawked as cure-alls for pavement problems. Engineered materials have competed with reclaimed waste products like carpet scraps for their place in pavements, and when a performance problem developed, fibers in general – not the use of questionable materials – took the blame.
But now, fibers as an engineered material have taken their place in the toolbox of products with utility in road construction.
Synthetic fibers for asphalt
Cold climates, but also heat and rain in warmer climates cause cracks and deterioration in asphalt, says Scott Nazar, technical manager, FORTA Corp., a supplier of synthetic fibers. “DOTs and owners of other paved surfaces (e.g. airport runways and parking lots) can enjoy longer pavement life and increased structural stability if the asphalt mix is reinforced with synthetic fibers,” he says.
For instance, asphalt at 3.5 inches of depth, reinforced with synthetic fibers, is as strong as asphalt at 5.5 inches of depth not reinforced with fibers, Nazar says.
“These owners can save in the short term and in the long term,” he adds, “because roads reinforced with synthetic fibers last longer and crack less in the first place, no matter whether the environment is hot or cold.”
However, the majority of asphalt pavement work is of the mill-and-fill variety, he says. In these situations, the synthetic fibers can be used to extend the life of the thin overlay, because decreasing thickness is usually not an option.
“Not all fibers are created equal, and the difference matters for our roads,” Nazar adds. “Before contractors make the decision to use fiber technology to reinforce roads, they need to know the differences between types of available fibers that could dramatically impact the life cycle of a project.”
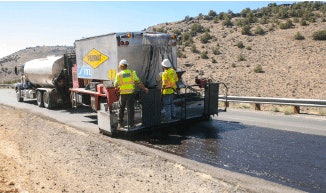
Engineered fibers for asphalt may include asphalt stabilization additive fibers, asphalt reinforcement fibers and fiberglass reinforcement. “Historically, discussions about using fibers for asphalt mixes have centered on cellulose fibers to prevent drain down that occurs when using stone matrix asphalt mixes (SMA) or other high asphalt-content mixes,” Nazar says. “The use of cellulose allows designers to put more asphalt cement in the mix without having a soupy mess.”
Another such mix is the polymer-modified, open-graded friction course (OGFC), which minimizes fines that could inhibit movement of surface water through the lift. Today’s OGFCs utilize cellulose fibers to forestall drain-down of liquid asphalt, although warm mix asphalt used for OGFCs can eliminate cellulose fibers in those mixes.
One of the first technologies using fibers was stress-absorbing membrane interlayer (SAMI). “Constructing SAMIs involves applying emulsion and spraying on a layer of fiberglass fibers, then adding on another coat of emulsion and aggregate chips,” Nazar says. “The SAMI provides a two-dimensional mat for preventing cracks from migrating through the pavement structure.” However, he adds, while the SAMI layer itself may not crack, cracking can occur in layers above and below the SAMI.
Until now, most fibers were derived from plastic and often melted in the mixing process. A portion of the melted fiber did help to modify the asphalt, increasing rut resistance and also cold weather cracking resistance, he says.
“We’re in a different age of blended fiber use today,” Nazar told Better Roads. “High-tensile strength fibers can be added to the asphalt mix during production at the plant, providing crack resistance throughout the entire depth of the pavement layer in which it is placed. High-tensile strength fibers include aramid fibers able to withstand temperatures from -320 degrees Fahrenheit to 800 deg Fahrenheit.”
A blend of fibers works well for the road agency, he says. “I’ve found a blend of aramid and polyolefin fibers is the way to go,” Nazar says. “It’s best of both worlds; the blend reduces both high temperature rutting potential and thermal cracking. I have even noticed improved densities of fiber mixes because the fibers keep the material from spreading out under the rollers during breakdown compaction. These high-tensile fibers have also shown to provide the best benefit when tested at high-strain values equal to or greater than 250 micro strains.”
Fibers enhance thin overlays
Thin-asphalt overlays are a sustainable, low-cost alternative to conventional hot mix asphalt overlays, but their performance can be enhanced with the optimal design, including additives like fibers, say Songsu Son, Ph.D. candidate, and Imad L. Al-Qadi, professor of engineering, and director, Illinois Center for Transportation, University of Illinois at Urbana-Champaign, in their 2014 Transportation Research Board paper, Engineering Cost-Benefit Analysis of Thin Durable Asphalt Overlays.
“Significant improvement of pavement performances has been achieved with regard to material selection and modification, mix design, and construction technology,” they say. “However, most of these improvements require high-quality aggregate and expensive modified asphalt binder or special equipment for construction.”
In response, new-design asphalt mixes have come to the fore as stakeholders seek better-performing mixes at lower cost, say Son and Al-Qadi. These new asphalt mixes offer significant cost savings while improving structure and function characteristics, including durability, friction, quietness, rutting, cracking and moisture susceptibility resistance.
To evaluate field performance of these new mixes under actual traffic loading and environmental conditions, including the control mixes, pavement sections with six asphalt mixtures and various wearing surface thicknesses were constructed.
Two typical Illinois surface mixtures were selected as control mixes: a 9.5-mm NMAS coarse dense-graded mixture (F-mix) and a 12.5-mm SMA. The SMA mixture generally requires more durable aggregates, modified asphalt binder, and cellulose fibers, which makes it more expensive than typical dense-graded mixtures.
Three fine dense-graded asphalt mixes with a 9.5-mm NMAS and one SMA with a 4.75-mm NMAS were developed for a relatively thinner wearing course. Locally available aggregates were employed, among them being a steel slag/fiber mix designed to provide good friction and high resistance to stripping and permanent deformation due to the use of steel slag.
A blend of polypropylene and aramid fibers was added into the slag mix to improve its tensile strength, allowing placement at a relatively thinner layer thickness. A PG 70-22, SBS-modified asphalt cement was utilized, and the aggregate mix was 62.2 percent dolomite, 17.5 percent natural sand, and 20.3 percent slag.
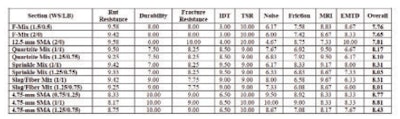
In-place field testing was performed immediately after construction and every four months up to two years. Testing at these intervals provided results for initial field performance and short-term performance for each section. The in-place field testing included onboard sound intensity measurement, laser longitudinal texture profiling, locked-wheel friction, and walking foot inclinometer (dipstick) rut measurement.
Then the pavements were evaluated and scored, and using a formula, the authors converted the ranks to numbers to calculate the overall performance numerically from 0 to 10 (worst to best). The steel slag/fiber mix scored second highest in their performance rankings.
“In general, the control mixes resulted in lower performance scores compared to the new mixtures,” Son and Al-Qadi. “The 4.75-mm SMA section with a 1-inch wearing surface provided the highest overall performance score.”
Stress-absorbing membrane interlayer
In Washoe County, Nevada, County Highway 447 was improved by cold in-place recycling, placement of a fiber-reinforced SAMI, and finished with a Type III slurry surfacing as the final wearing surface instead of a costly total reconstruction.
“With fuel prices going up, we are seeing a lot more truck traffic on 447,” says Bill Gooch, road supervisor, County of Washoe Road Division, Gerlach, Nev. “It’s a short cut; one truck driver told me taking 447 saves him three hours driving from Portland or Seattle to Phoenix or Las Vegas.”
Also, the highway is burdened once a year by the weeklong, end-of-summer Burning Man art festival celebrated in the desert north of Gerlach.
“Basically the highway was just sand and oil, mixed together,” said Greg Belancio, P.E., senior licensed engineer, Engineering Division, Washoe County Department of Public Works. “The section averages 4 inches thick and the county had been doing it that way since the 1970s.”
“The cold in-place process is really going to help us out,” Gooch said. “It’s totally redone the road surface. All the cracks are gone. And we follow with the fiber membrane, which should resist future cracking and provide strength against lateral loading. We anticipate that it will bring not just lateral and horizontal strength, but strength in all directions.
The crack-resistant membrane, called FiberMat by Colas Solutions Inc., is a specially formulated, polymer modified, fiber-impregnated membrane binder for use with chip seal applications or as an interlayer with various overlays (e.g. HMA, slurry surfacings or micro surfacing).
FiberMat provides strength and flexibility due to the utilization of chopped fiberglass strands that form a high-tensile strength matrix. The system is installed by a truck-mounted machine that uniformly applies the fiberglass strands – cut from onboard spools – in a random, continuous application.
In placement, the strands are sandwiched between two layers of sprayed latex polymer-modified CRS emulsion, prior to the application of an aggregate cover. Much like a conventional chip seal, the final product then is gently rolled with rubber-tired compactors to seat the aggregate into the product.
The combination of highly modified asphalt residue and a fiberglass reinforcement matrix creates a crack-resistant membrane that can stand up to heavy traffic loadings.
Fibers in concrete bridges
High-performance, fiber-reinforced concrete controls cracks and provides satisfactory bond strengths in bridge deck construction, say Levon C. Hoomes, E.I.T., Celik Ozyildirim, Ph.D., P.E., principal research scientist, and Michael C. Brown, Ph.D., P.E., associate director, Virginia Center for Transportation Innovation and Research, in their 2014 TRB paper, Evaluation of High Performance Fiber-Reinforced Concrete for Bridge Deck Connections, Closure Pours and Joints.
“Connections, closure pours and joints in bridges are often a source of distress due to cracks and openings in them,” say Hoomes, Ozyildirim and Brown. “Wide separation facilitates the penetration of harmful solutions which can lead to costly repairs.”
Cracks are caused by volumetric changes due to moisture and temperature and the application of service loads after the concrete has hardened, they write.
“The addition of a small amount of discontinuous fibers to a conventional concrete matrix minimizes cracking, but the size of these cracks still permits the intrusion of harmful solutions,” say Hoomes, Ozyildirim and Brown. “High volumes of suitable fibers used in high performance fiber reinforced concrete produce multiple very tight cracks (< 0.1-mm wide), which do not allow for the ingress of water and other harmful solutions.”
The authors evaluated plastic and hardened mixture properties, with emphasis on deflection hardening, flexural toughness, and bond strength. Different systems were tested: engineered cementitious composite (ECC); hybrid fiber-reinforced concrete (HyFRC) systems, including both steel and synthetic discontinuous fibers; HyFRC including only synthetic fibers; and ultra-high performance concrete with steel fibers.
The authors conclude the following:
• ECC and HyFRC mixes achieve deflection hardening with high fiber content of steel or synthetic fibers. ECC achieved the highest deflection hardening capacity of all systems tested.
• Although UHPC attained the highest stress capacity, the material did not deflection-harden; results are partly attributed to the settling of the fibers to the bottom. High shrinkage values do not necessarily indicate wide cracks. ECC exhibited the highest shrinkage values, yet showed deflection hardening and uniformly distributed, tight cracks instead of few wide cracks.
• Workability of mixtures with steel fibers was higher than those with synthetic fibers.
• All mixtures achieved adequate bond strength for use in closure pours.