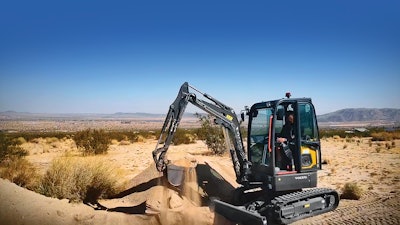
Editor’s Note: This is Part Six of an eight-part series on the evolution of construction equipment and the diesel fuel alternatives manufacturers are introducing, including hybrid machines, electric and battery-powered equipment, and hydrogen combustion and hydrogen fuel cell technology. You can read Part One in the series by clicking here. Part Two. Part Three. Part Four and Part 5.
Jacques Marais has worked in the construction industry for 35 years and has been seeking cleaner alternatives to diesel. The director at Baltic Sands out of Yucca Valley, California, his company specializes in environmentally sensitive, luxury off-grid property development and real estate.
Keeping up with the current trends while at trade shows and reading magazines and online sites pointed him toward electric machines.
"I became interested and felt like it was a good idea to pursue the idea of using them on certain sites that they would be suited for," Marais said.
Ultimately, his interest prompted him to reach out to Volvo Construction Equipment nearly two years ago to inquire about testing some of its then-new electric machines. Simultaneously, Volvo was in the process of looking for pilot users of the L25 compact electric wheel loader and ECR25, a compact electric excavator.
For Marais, it was just a fortunate intersection of circumstances that allowed his crews to use the machines and see what they were capable of.
“The pilot project with Volvo CE allowed us to pursue the ideal of being more ecologically friendly through the adoption of new technologies,” he said.
The commercial pilot was part of a $2 million grant administered by the South Coast Air Quality Management District (AQMD) to accelerate the deployment of zero-emission technologies for off-road mobile equipment, which is one of the major contributors to nitrogen oxide (NOx) emissions in the South Coast Air Basin. The South Coast AQMD region includes Orange County and major portions of Los Angeles, San Bernardino and Riverside counties, including the Coachella Valley.
The L25 Electric is comfortable working in rugged and remote conditions.Volvo
Test models of both machines had limitations relating to available work hours. Updates have been made to extend the work-time length since testing began.
“We applied them to projects that if they didn't fulfill an eight-hour day, it wouldn't be a train crash,” he said. “It suited the application for us, or that's what we ultimately discovered. At the early stages, we had to consider what their capabilities were against what we were trying to achieve on a particular site and try to match the two.”
The unique circumstances were the remote locations, which was part of the test to examine the practicality of electric machines in those scenarios.
Charging solutions became one of the biggest challenges. From a charging perspective, if working at a material handling facility with a regular plug-in point or a more urban environment where the machines are more geographically bound to an area or zone where they have ready access to electrical outlets, it appears more feasible.
"On the other hand, we had to cope with being very remote," Marais said. "We were working in the high desert, and we had no access on our sites to anything near us to an outlet that was coming from the existing grid."
Provisions had to be made to transport and relocate to an urban area to plug in. There was a distinctive downside to the lack of a charging solution initially.
“That posed a challenge for us and, of course, as part of the contractual agreement, we were not allowed to use generators, which would have gone against the purposes of the experiment,” Marais said.
To accommodate the test, they had to reconsider how some of the developments were being completed. Rather than start with slab and groundwork, the solar array was commissioned to go first, giving the crew an outlet and then charging the electric machines onsite to complete the remaining groundwork. It was used to power the machines overnight and during lunch, helping the remote jobs move faster and more efficiently.
“That became a very useful solution for us,” Marais said.
Other than the charging solution, he was impressed with the two electric machines.
“If you had to compare them to their diesel counterparts in terms of the actual performance when they're running, there was nothing to differentiate them," Marais said. "The capabilities were, in my view, equal to Volvo's diesel-powered machines of the same size. In our unique circumstance, we were successful in having a good run with them."
For the test program, the L25 and ECR25 performed a wide range of tasks. He said the ECR25 shaped building pads, performed over-excavation for subgrade improvements, dug trenches for gas, electrical and water lines, performed various landscaping tasks, and excavated the irrigation recovery systems. In many instances, the excavator set the soil aside into stockpiles to be moved later by the L25.
The L25 reshaped the larger areas, performed the finish grading to assist with stormwater control, and relocated the soil stockpiles for further processing.
Now and in the future
Marais said if he had the opportunity, he might pursue such machines. As it is, he is still in the process of setting up infrastructure so just trying to find a footprint that's big enough to be able to justify and warrant having that type of equipment in a fleet is not currently in the cards.
The upgraded battery option on the L25, however, may hold some promise.
For companies that are well established, organizations that have the wherewithal to deal with the cost difference and charging solutions, he said, going electric is certainly plausible.
"The positive side of it is, in terms of its performance capabilities, it's all the qualities that are required by these machines and what they want to get out of them if it were versus diesel-powered," Marais said. A reduction in noise and lack of emissions are the other prime positives.
For example, he said the reduced noise helps during meticulous work and communication between the operator and crew members.
"If you work in confined spaces, if you're working in restricted areas, if you're working in urban built-up areas, and you're looking for noise abatement, these are very positive things," he said. "That's what I would tell a contractor that would be looking at these."
One point that he would emphasize to any contractor considering buying electric is to recognize that they are not mass-production machines. Having been in the industry for more than 30 years, he's done plenty of time and motion studies on equipment.
The ECR25 Electric performed various tasks in helping to build off-the-grid homesVolvo
The smaller compact wheel loaders like the L20 or L25 or compact excavators are invariably working with a team, or they have been paired with other machines that are contingent on one machine doing an activity first or a crew coming along to clean up the bottom of a trench or other space with shovels and spades.
“There are opportunities for contractors to identify where they are not using the equipment for eight hours a day and not to be intimidated by that limitation,” Marais said. Actual machine time is closer to four to five hours across a full eight- or nine-hour workday in most cases.
“All contractors can do some sort of a projection in terms of what their activities are going to be like and how long they're going to take it and how many hours the machine is going to consume,” Marais said. “That's something for a contractor to consider, and that could be something positive.”
In addition, he noted that the electric machines are clean and easier to maintain. The electric machines don't require diesel engine maintenance, such as changing oil, oil filters and diesel particulate filters. The DEF tank is also eliminated. What remains is the hydraulic system's oil and filter and the coolant for the inverters and the drivetrain.
Other than hydraulic fluids, there is minimum machine involvement. Marais noted that, of course, the pin and bush points need to be greased. During the test, Baltic Sands did not run a machine a full cycle to the point of service, but the overall intervals were said to be equal to or exceeded that of the diesel counterparts.
Marais admits that the additional upfront cost of the electric machines is currently a downside. Determining whether the ROI is there requires doing an exercise balancing the life cycle of the machine and cost.
“Suppliers know that is an issue. I don't think it's only Volvo. I think a lot of the OEMs are battling to get the process to be commensurate with the diesel-powered units,” he said. “I think when they get to that intersection point, they'll find it a lot easier to offload the machines.”
Volvo CE has recently delivered its first production models of its ECR25 electric compact excavators to customers after field testing.
Reservations for the ECR25 and the L25 Electric compact wheel loader were opened in August 2021, and the first deliveries were made earlier this year. Now additional models, the L20 electric wheel loader and EC18 and ECR18 electric excavators have since become available for reservation.
According to Volvo, as the development of electric machines continues, the diesel versions of its compact equipment will be phased out. The compact line of electric equipment is only the first in the rollout as engineers develop systems for larger construction equipment.
The next step for Volvo is a 22-metric-ton electric excavator set for trials in 2023. Marais said he was approached to be involved in the pilot program, but it did not fit his schedule.
“They've set themselves some lofty goals, which I think can be achieved judging from the teams they've got onboard,” Marais said. “I’ve always been curious and quite anxious to see where this is going and how we can apply electromobility to our business. I can’t emphasize enough how excited we are to be in this position right now. I just have a sincere belief that this is the future.”
Volvo