Lasers
Despite competition from 3D GPS systems, 2D laser control systems are still a viable and low cost way to guide your earthmoving operations. But the smart buy today is a 2D system that you can upgrade to 3D later on.
By Tom Jackson
When rotating lasers were introduced to the earthmoving market many decades ago, they were hailed as a breakthrough technology. And while they can’t be considered cutting edge any more, lasers, despite the profusion of more advanced and more expensive 3D total stations and GPS systems, are still holding their own.
“A good quality laser and machine mounted receiving system is still widely accepted as being one of the most reliable forms of elevation control,” says Dan Dykhuis at Leica Geosystems.
What has changed in lasers over the years has been mostly incremental. They’ve gotten more durable, less expensive and manufacturers have improved what they call their “feature sets,” adding things like wireless remote operation, self-leveling capabilities, and plug-and-play components. Older lasers used big, bulky batteries, but laser systems today enjoy the fruits of improved battery technology and have become lighter and more powerful.
Leveling the field
There is still a considerable number of applications in earthmoving that don’t require anything more than a laser – athletic fields, building pads and footers, plus simple parking lots. “A lot of my [laser] customers are smaller contractors,” says Tim Baker, segment manager for site preparation products for the building construction division at Trimble. “They have utility machines: skid steers, backhoes, and compact excavators. Some have dozers. A lot of them do landscaping, general contractor work such as hospitals, commercial work and small subdivisions.” The same is true with trenching and pipeline work.
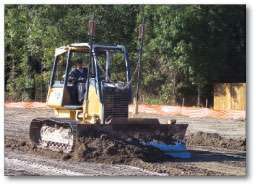
The key to these customers, says Baker, is to give them something that’s easy to put on and take off a machine. Whereas a GPS customer will likely dedicate one machine to a system, the laser user might switch his receiver and control panel between a number of different machines throughout the construction season.
Upgrade paths
Perhaps the biggest change in today’s lasers has been driven by the GPS revolution. Manufacturers of both types of systems have developed laser systems that can quickly be upgraded to GPS. And with some GPS systems, you can switch from 3D back down to 2D, says Brian Juroff at Topcon. “You can grade inside a building with just the touch of a button. There are still applications where 2D is necessary. Where the satellite signals are degraded due to obstructions or a heavy canopy and the GPS is not operating at peak efficiency you have to go to conventional means,” he says.
This mixed system approach is gaining popularity. “It’s not uncommon in a large subdivision to have GPS 3D doing the bulk of the grading, but you also might have a couple of 2D excavator systems doing simple trenching or retention pond work. These 2D systems can be easily upgraded as applications dictate thanks to a common system architecture that can use the 3D sensors from other machines,” says Jeff Drake, segment manager machine control products for the heavy highway division machine control products at Trimble.
Plumbed at the factory
Assuming you’re going to go with an automated blade control system, many machine manufacturers now make their equipment “guidance-ready” from the factory using can-bus wiring and an extra circuit on the hydraulic valve bank.
But you can also retrofit older equipment or machines that aren’t factory wired for blade control systems by adding a hydraulic circuit and the wiring. Expect to pay $3,000 to $6,000 to have additional hydraulics installed. Once you’ve plumbed the machine’s hydraulics to take directions from an electronic signal, installation of an automatic system is only a matter of putting brackets for the control panel in the cab and receivers on the blade.
Automate or indicate
“Indicate” or visual-only laser systems, show the operator his blade position using illuminated bars or arrows. They are less expensive than plumbing a machine for automated blade control. But for most contractors, automation makes more sense.
“Guys start out manual, or visual, and then they realize that they should have spent the money and gone with automatic,” Dykhuis says. “Operating a dozer visually can be tedious. Larger contractors and repeat buyers are going to go automatic, whereas a first-time buyer thinks he’s going to save some money with a visual system, but he usually comes back for the upgrade.”
And even a good operator can’t make the constant corrections and micro-fine changes in blade elevation as fast or consistently as a laser guided hydraulic system. End result: automatic systems give you better, quicker results with a less skilled operator and less stress on that operator.
Excavator control
Another application for lasers that has become popular in just the last few years are laser- based excavator systems. These show you in real time just how deep your bucket is and offer numerous advantages:
• You don’t over-dig, which saves time and fuel and prevents operators from disturbing soil below the design grade.
• You dig flat, precisely graded trench bottoms.
• You don’t have to put a man with a survey pole in the bottom of the trench, reducing labor and greatly improving safety.
Laser-referenced excavating systems use angle sensors on the boom and stick that feed information into a small computer/controller. The computer combines all the angles and distances and gives the monitor in the cab an exact picture of where the bucket sits in real time relative to the design parameters of the trench.
Lasers vs. GPS
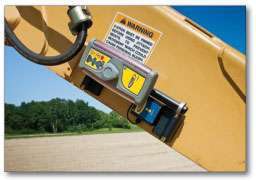
Applications will determine which tool is best for your situation – small flat planes for lasers, big complex surfaces for GPS. But before signing off on one or the other it’s also smart to consider all the variables:
Lasers pro:
• Low cost, $3,000-$5,000 for earthmoving systems
• Millimeter level accuracy
• Easy to learn and train operators on
Lasers con:
• Constrained by distance, 500 to 800 feet
• Circumscribes flat planes or slopes only
GPS pros:
• Not constrained by distance, can cover miles of terrain
• Circumscribes complex, 3D topography
• Eliminates much of the labor, cost and time delays associated with survey and staking.
GPS cons:
• Expensive: $40,000 to $100,000
• Accuracy only down to centimeter level without auxiliary system
• Satellite signals can be blocked by trees, mountains, buildings
• Requires more training time for operators, supervisors.
The other thing you have to consider is your return on investment. It doesn’t take long for either system to pay for itself. A couple of ball fields and a few building pads and your laser system has earned you back what you paid for it. Likewise technologically savvy contractors can sometimes pay for a GPS system with a few big earthmoving jobs.
But given their high initial cost, plus the training involved, you need a lot of work and the right kind of work to justify a GPS system. With a laser system it’s not essential that you use it every day to get a decent return on your investment.
“Both the laser and GPS systems can have immediate payback,” says Drake. “But once you put the infrastructure in to support GPS and optical [total stations] it becomes ubiquitous on the sites and at that point contractors tend to deploy as much technology as they deem necessary for the project.” EW
The new family of machine control laser sensors from Topcon includes the LS-B100 series, which offers on-grade matching and wireless capability in a unit that’s easy to move between machines. The CAN compatible sensors can be run as an indicate-only sensor or set up for automatic machine control. Also in the family, the RD-100W receiver allows for in-cab on-grade matching and on-grade accuracy adjustments and two-way communication between the receiver and remote display.
Visit EquipmentWorld.com/info
Lever-engaged rare earth magnets on the LMR240 machine receiver from Leica make it easy to position and lock onto an excavator arm. LED up-down arrows show the position of the cutting edge in relation to the laser reference beam. The waterproof unit provides accurate grade information in fine or coarse modes and takes signals within 240 degrees of any rotating laser.
Visit EquipmentWorld.com/info
The LMR360R machine mounted receiver from Leica has a built-in vertical indicators to tell you if the excavator stick is plumb or over or under extended. When used on dozers or grader these LEDs can be turned off to save battery power. The LMR360R can be magnetically mounted or secured with an optional mounting clamp and can pick up the beam from any rotating laser in a 360-degree field.
Visit EquipmentWorld.com/info
The Spectra Precision Laser DDS300 works wirelessly, enabling you to quickly change it from machine to machine. Using the laser receiver as a reference allows you to continue digging without multiple benchmarks and the 7-inch color touch screen with audible alarm provides intuitive menus and stores profile templates.
Visit EquipmentWorld.com/info