By Brian Morrow
The uncertainty that contractors face regarding unknown subsurface conditions can be their greatest risk. This type of risk is inherent on most road and heavy construction projects, commonly because testing of subsurface conditions is expensive and limited. This results in conclusions being drawn from limited data. In addition, this risk is often further exagerrated because geotechnical engineering is uncertain, often described as part science and part art.
In light of this risk, most major standard form construction contracts contain a differing site conditions clause. These clauses typically allocate to the owner the risk of unknown site conditions that the contractor could not have reasonably anticipated based on the contract documents and/or site investigation.
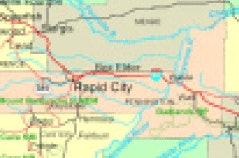
Differing site conditions clauses typically offer two separate bases for relief: Type I clauses are based on site conditions that differ materially from the conditions indicated in the contract documents, while Type II clauses are based on site conditions that differ materially from those ordinarily encountered and recognized as inherent in the work.
In the recent case, Appeal of NDG Constructors (August 21, 2012), the Armed Services Board of Contract Appeals (ASBCA or Board) denied the claim of NDG for a Type I differing site condition. NDG contracted with the Army Corps of Engineers for $959,300 to tunnel a waterline underneath I-90 near Rapid City, South Dakota, to serve Ellsworth Air Force Base. NDG’s work included constructing a 16-inch waterline under I-90 by tunneling and jacking approximately 560 linear feet of 54 inch steel casing. NDG subcontracted the tunneling portion to BT Construction, Inc., (BTC), a pipeline excavation contactor, for $706,000.
The contract documents incorporated two geotechnical reports from American Engineering Testing, Inc., including a total of 7 borings, soil samples obtained in accord with ASTM procedures, and lab tests of the soil samples. During the work, NDG and BTC encountered difficult soil conditions that slowed their planned rate of progress, including shale rock, fat clays, and wet soils.
NDG submitted a claim of $146,278.94 and 9 calendar days based on alleged Type I differing site conditions. The contracting officer denied NDG’s claim, and NDG appealed to ASBCA.
In reviewing its review ASBCA noted that Federal Acquisition Regulation 52.236-2(a)(1) provides that Type I differing site conditions consist of “subsurface or latent physical conditions at the site which differ materially from those indicated in the contract.” In order to prove entitlement to a Type I differing site condition, NDG had to establish that:
… the conditions indicated in the contract differ materially from those actually encountered during performance; the conditions actually encountered were reasonably unforeseeable based on all information available to the contractor at the time of bidding; the contractor reasonably relied upon its interpretation of the contract and contract-related documents; and the contractor was damaged as a result of the material variation between expected and encountered conditions.
In light of the foregoing, the Board analyzed the three different aspects of NDG’s claim.
First, NDG claimed that the soil profile was a differing site condition because the soil transitioned from clay to shale quicker than expected. NDG’s expert testified that he anticipated shale would be encountered approximately 202 feet from Boring B-3, though it was encountered approximately 100 feet from Boring B-3.
NDG’s expert reached this conclusion by drawing a straight line between Boring B-2 (where shale was indicated) and Boring B-3 (where fine alluvium soil was indicated).
The Board found this analysis faulty, in part because the soils reports and boring logs did not indicate where the transition to shale would occur. In addition, in preparing its estimate, BTC recognized the transition to shale would take place “at some point” as opposed to any specific point. As a result, the Board denied this aspect of NDG’s claim.
Second, NDG argued that “[a] reasonable contractor would have anticipated encountering mostly lean clay, with some ‘fat to lean clay’ or ‘lean to fat clay.’ Instead, NDG and BTC actually encountered mostly fat clay.” However, the Board found the boring logs indicated that Boring B-3 encountered a “mixture of lean to fat clay,” while Boring B-2 encountered “fat to lean clay.”
Since the material that was encountered — “mostly fat clay” — did not materially differ from the possible range indicated in the boring logs (“fat to lean clay” and “lean to fat clay,”), the Board concluded that NDG failed to prove a Type I condition in this respect.
Third, NDG contended the moisture content of the soils was much higher than indicated or anticipated, and thus, was a differing site condition. NDG stated that it encountered soils described as “very wet” or “extremely wet,” while the soils reports described the soils as “moist to very moist,” and as “soft wet soils, along with groundwater . . . that should be anticipated.”
The Board did not see a difference between the wet conditions claimed by NDG and the soils described in the reports. In addition, the Board found NDG’s expert’s sampling of soils unconventional and contaminated by Bentonite slurry. Because the soil moisture encountered by NDG was what the soils reports indicated “should be anticipated,” and the soil samples relied upon by NDG were not reliable, the Board found that NDG failed to prove a Type I differing site condition in this instance.
This case illustrates the difficulties that can be encountered in trying to prove a Type I differing site condition claim. In order to prevail on such a claim, the contractor needs to scrutinize the contract documents and show how and why the actual conditions encountered were different from those indicated. This includes an analysis of contract language and technical documents incorporated into the contract such as soils reports.
Brian Morrow is a partner in Newmeyer & Dillion LLP, a law firm in California. He is a licensed California Civil Engineer, and specializes in construction law, including road and heavy construction. Contact him at [email protected]