Terex glider reman
What it takes to turn an aging front discharge concrete mixer into a good-as-new machine
By Tom Jackson
In the current construction economy, some ready mix producers are reluctant to buy new mixer trucks at full price. But, as their fleet ages, it requires more and more repairs, suffers more downtime and ultimately produces less income for the owner. What’s the producer to do?
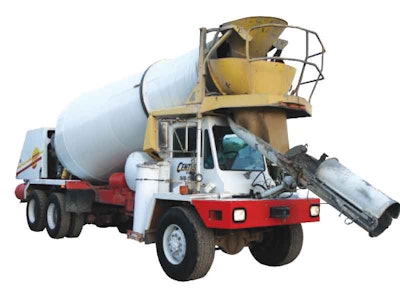
One solution is to look into the reman programs being offered by some OEMs. In these programs the dealer or OEM takes your used machine and rebuilds the critical components to good-as-new-condition for a cost that’s considerably less than new – up to 40 percent less than a new machine. You get almost all the productivity and life of a new machine and eliminate the frequent disruption and cost of unscheduled repairs.
To get a better idea of how these programs work we talked with Jim Aslin, an equipment specialist with the Terex concrete producer group. Aslin walked us through the process of ‘glidering’ a front discharge mixer truck.
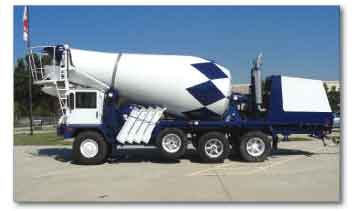
“The ideal candidate is a donor truck in the 10- to 12-year-old category,” Aslin says. “The reasoning is that we are going to get a second round out of the major components, say another eight to nine years, and at that point, more than likely, the major components will reach their point of being obsolete and be ready for retirement.”
Another significant economic advantage of glider trucks vs. new is the avoidance of Federal Excise Tax if the process is managed within defined guidelines. For example, the cost of the glider must be less than 75 percent of the cost of a similarly specified new truck. This cost savings often exceeds $10,000.
Component considerations
“In all cases, we must re-use the original tandem driving axles,” Aslin says. “Also, we must re-use either the original transmission and/or the original engine. One of those two major components may be a reman but not both. The reman component cannot go back in time. It must be equal in year of manufacture to that of the donor truck or a newer upgrade. The other component can be rebuilt.”
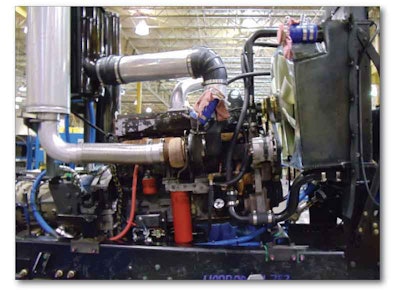
The typical glider truck is rebuilt on the same factory line where the new trucks are built in Fort Wayne, Indiana; however, ready mix producers with sufficient facilities and mechanics may opt to do the teardown or rebuilds themselves. The most commonly reused components include the engine, transmission, transfer case, drive axles, wheels and tires, drum drive transmission and hydrostatic pump and motor for the drum.
Aslin says customers can send them most any brand of mixer truck and the factory will use those components to create a Terex glider truck.
Here’s a checklist of the typical components sought for the Terex glider and their criteria:
• Engine. Look for horsepower to equal the rest of your fleet.
• Transmission. Automatic is preferred but manuals can be upgraded to automatic.
• Tandem axles. Requires a 46,000-pound rating, but you can reuse 40,000-pound axles in a limited number of configurations.
• Front axle. Requires a currently manufactured axle with a minimum rating of 21,000 pounds with S-cam brakes.
• Mixer drum. This is replaced with a new drum.
• Hydraulics. The main pump and motor may be reused or upgraded to new depending on condition. All other hydraulic components will be new.
• Air system. Replaced with all new components with the exception of a customer supplied engine air compressor. A reman or rebuilt engine will have a reman compressor.
• Drum drive. Can be reused as is, exchanged for a factory rebuilt or purchased new with no core necessary.
• Frame. This will be built new to engineering specs that coincide with the axle configuration.
• Wiring. All new.
• Suspensions. All new. (Aslin emphasizes that while some customers want to re-use tandem axle suspensions, Terex cautions against it.)
• Wheels and tires. The best choice is hub piloted wheel rims. Dayton cast spoke open center are acceptable. Stud piloted are the least desirable. Customer supplied tires are fine.
• Transfer case. Terex suggests reusing, but the customer may elect to purchase new.
• Auxiliary axles. New and included in the price. Customer may elect to supply his own wheels and tires for the auxiliary axles.
• Additional components. New drivelines, steering box and steering pump, new cooling package including radiator, transmission cooler and charge air cooler if applicable.
Evaluation and disassembly
Terex gives the customer the option of doing the disassembly or having the factory do the work. If the customer does the work, Terex supplies the teardown instructions. “The customer knows the component history best and must be the judge as to determining the use of major components,” Aslin says. The components will be inspected again at the factory.
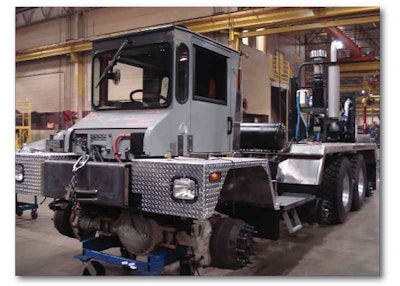
Customers can also opt to do their own reassembly with a kit supplied by the factory. The basic glider kit includes a plumbed box frame drilled to accept auxiliary axles, dressed cab, steering gear with new front suspension and a roller pedestal with rollers.
Aslin cautions that there is a steep learning curve to rebuilding one of these mixers. You need dedicated shop personnel with a high level of skills, overhead lifting capability and a sufficiently sized spray booth and painting equipment. Only about 10 percent of ready mix producers opt for the kit route.
Factory turnaround
When the Terex factory handles all the work it takes about six weeks for tear down, parts inventory, cleaning and inspection in preparation to go onto the assembly line, Aslin says. Subject to the availability of a production line slot, it will take another four weeks for assembly, testing, paint and final inspection.
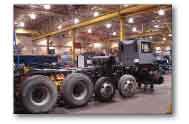
The customer can drive the truck to the factory, have it sent on a lowbed trailer, or disassemble it and send the donor components only. The warranty is one year, bumper to bumper, with the exception of any customer supplied components.
Emissions and retrofits
Since new trucks as of last year are required to have expensive diesel emissions systems on them, the cost difference between a glider truck and new is even greater. Compared to new trucks with the EPA 2010 compliant engines, the typical glider truck will range in cost at 50 to 65 percent of a new truck, Aslin says.
Glider trucks aside, engine repowers have been done on some types of trucks and off-road equipment in areas of the country where air pollution restrictions call for it. But, putting a diesel engine with selective catalytic reduction (SCR) technology into an older truck is impractical. “That integration involves additional fuel tanks, pumps, heated fuel lines and additional computer ECU upgrades that would be cost prohibitive,” Aslin says.
Aftermarket exhaust filtration devices such as diesel oxidation catalysts (DOCs) and diesel particulate filters (DPFs), however, can be added to a glider truck to help meet local emissions regulations. EW