Single drum vibratory compactors
Stay on top of the maintenance and you can get a decade of low-cost operation out of these workhorses
By Tom Jackson
And although it’s a simple machine, a lot of iron and a stout diesel engine go into every one, pushing the price of the most popular size class into six digits. But with good PMs you can amortize the cost of your single drum compactors over as much as 10 years, giving you a lot of value over time.
To find out more about the owning and operating costs of single drum compactors we talked with Ricardo Perez at Dynapac. Perez suggested we use Dynapac’s CA250 single drum soil compactor as an example. The CA250 sports an 84-inch drum and has a maximum operating weight of 29,765 pounds (smooth drum) or 30,100 pounds for the PD or pad foot model. It runs on a 110-horsepower Cummins water-cooled diesel engine and carries a 66-gallon fuel tank.
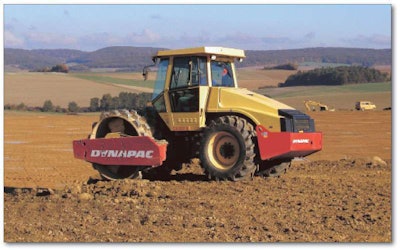
Typical usage for this type of machine works out to about 1,000 hours a year, and the average useful lifecycle runs about 10 years, Perez says. “The average soil roller is kept until its repair costs are not acceptable and justify buying a new one,” he says.
We based our O&O cost calculations on a ballpark purchase price of $100,000 for the machine. We assumed a diesel fuel price of $2.75 a gallon and fuel use at a half a gallon per hour. Preventive maintenance and recurring repair items are fairly well established norms, but the labor component of these costs may vary depending on whether you do your own maintenance or have a dealer or shop do it for you. See our list of scheduled maintenance for the CA250D on page 34. Operators’ hourly wages will also vary greatly depending on the region of the country you work in and whether or not you employ union craft workers.
Since this machine has such a long lifecycle we did not add a resale price back into the total. This is done on some machines with a short lifecycle and a high resale value, however in this case it was not warranted. Different O&O calculating methods will treat this issue differently so it’s best to consult with your accountant on whether or not to include resale as a cash positive entry against the total cost.
For interest, taxes and insurance, we calculated those at 0.9 percent times the selling price divided by the hours per year, which works out to 90 cents per hour. Taxes and insurance are usually fixed amounts but the interest you pay may vary quite a bit depending on dealer incentives and down payments.
As with most construction equipment O&O estimates, operator wages are your most expensive item followed by the purchase price, fuel and repair and maintenance in that order. There’s not much you can do to affect local wages, but you can and should do everything you can to keep the fuel costs down, including good maintenance and operating technique and limiting idling.
As with all our owning and operating cost calculations, these figures are theoretical and for discussion purposes only. To get a more accurate assessment of what your costs will be consult with your equipment dealer. EW