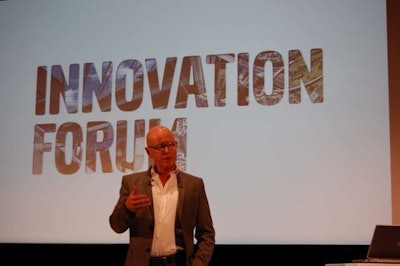
Volvo Construction Equipment kicked off its Innovation Forum Tuesday in Eskilstuna, Sweden with a fast paced series of briefings from the company’s top managers. A big equipment rodeo/demonstration also added to the festive atmosphere.
The event gave members of the press a rare opportunity to rub shoulders with the company’s brain trust and delve into the details of what makes this highly progressive, environmentally-focused company tick. Over the next month more than 5,000 customers and dealers will travel to Sweden for the big briefing.
Although company leaders stayed mostly mum about the exact technology Volvo CE will deploy in future machines, there were enough hints to at least develop some speculation as to what the company will unveil at ConExpo in March. Whatever Volvo brings to ConExpo, you can be assured it will be safer, more environmentally conscious and come with a dash of high-tech, Scandinavian style.
The Plan
Anders Larsson, vice president of technology, kicked things off with a description of what he and Volvo refer to as “the Plan.” And while the Plan is still something to be fully realized in the future, the company is hard at work developing the technology to make it work today.
When the Plan does come together it will include things like zero unscheduled stops, machines that instinctively avoid accidents, autonomous operation, 1,000 percent improvement in energy efficiency, fully electric machines, zero pollution and fill for life fluids, Larsson said.
Some of the technology is already here, Larsson said, such as autonomous wheel loaders guided by lasers and GPS. “We are working on a lot of interesting things,” he said.
Core values
Environmental care is one of Volvo CE’s core values, said Arvid Rinaldo, global communication strategy manager. In addition to maximizing fuel economy on its machines, Volvo is getting near to reaching its goal of having a CO2-neutral factory in Braas, Sweden. The company is also researching a variety of alternative fuels, with natural gas and dimethyl ether-fueled engines getting the lion’s share of the testing, he says.
Design
When it comes to design, Volvo strives to build “emotional capital” into every product, says Stina Nilimaa Wickstrom, design director. This means engaging the customers’ emotions and senses, giving them a look, feel and experience that they can associate with positive past experiences.
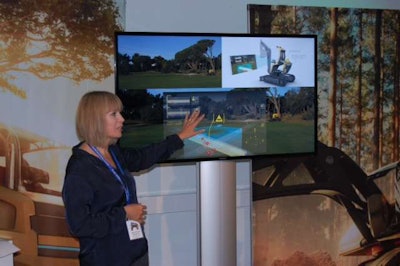
Given the size and scale of large earthmoving machines it is important that operators feel in control of their machines. For a machine like an articulated truck this is achieved by centering the operator seat in the middle of the cab, maximizing sight lines and giving the controls an intuitive layout, Wickstrom said. “It has to be simple, intuitive and safe. An operator can only process so much information,” she said.
The design department at Volvo is also used as a research tool and a way to encourage creative thinking among the engineers, Wickstrom said.
The actual features of these concept machines may or may not get pulled into a future earthmover. “We may gradually take in the interesting features of these machines,” Wickstrom said. The more important goal is to stimulate thinking and creativity.
Materials science is also closely watched by the design department, Wickstrom said. “We are constantly looking for new materials. There are a lot of things happening in renewable and recyclable materials. We have to be constantly looking for these things so we are not surprised.”
Emerging technology
While the design departments use their imagination, Jenny Elfsberg, director of emerging technologies, brings a team of engineers together to track the next big thing. Three big trends or paradigms, as Elfsberg calls them, are evolving in the heavy equipment world today.
Paradigm shift number one involves system decoupling. Right now most machine components are connected mechanically. Decoupling some of these and using electricity or hydraulic pressure to power the driveline or components will eliminate power losses and improve efficiency. Electric hybrids and hydraulic hybrids are examples that exist now, Elfsberg says, but the trend is toward total system electrification.
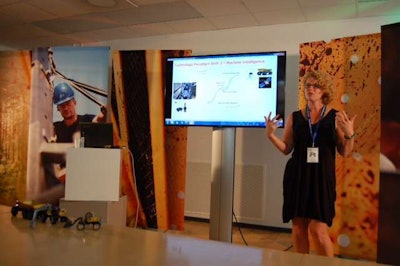
Paradigm shift number two is machine intelligence. In the automotive world an example of this is parking assistance and collision avoidance systems. Similar systems could be used to create an auto-dump bucket–a wheel loader that uses sensors to guide itself through the dump cycle so as not to bang the bucket against the side of the truck. Eventually, says Elfsberg, fully autonomous machines are a likely outcome.
The third big trend is what Elfsberg called total business solutions. “This is taking care of our customers,” she said. Solutions can take the form of site planning, machine to machine communications and telematics, and will vary depending on the needs of the customer.
Drivelines

Gunnar Stein, global director of driveline systems, said his group has challenged itself to develop systems that could eventually improve fuel efficiency to the point where the machines can move 50 percent more material using the same amount of fuel. Creating the OptiShift torque converter transmission in 2009 boosted efficiency by 15 percent, Stein said. The next step could be a continuously variable transmission that decouples wheel speed from engine speed and cuts fuel consumption by another 25 percent.
Volvo is also looking at electric and hydraulic hybrid drive systems, Stein says. Another promising technology is downsizing the engine and adding electric motor boosters on each wheel, which could up fuel efficiency by 50 percent.
Stein declined to say which technology was in the lead currently. The eventual winner will be determined by the market and the needs of the customer. All these alternative driveline systems cost more than conventional arrangements and the customer will need to see a return over time. Fuel prices, and CO2 regulation will all play a factor. “We already have the technical solutions,” Stein says. “We have to be ready when these boundary conditions change.”
Engines
One Volvo technology that is settled and heading to market in January is its Tier 4 final engine design. The company will use a SCR system coupled with a DPF in one component, said Peter Engdahl, manager of engine performance. The engine draws from Volvo’s considerable experience in developing diesel engines for trucks and busses and except for a few bracket changes is largely the same engine as its basic Class 8 truck engine.