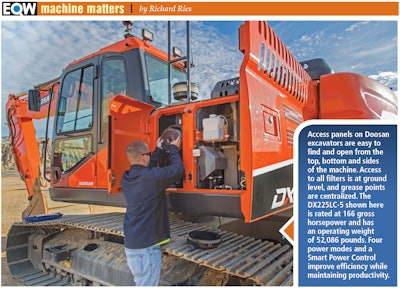
In the early days of machine control the customer had two options: take it or leave it. When manufacturers started bundling basic packages as standard equipment, the “leave it” option started to fade away.
The early-adopter contractors heralded the arrival of machine control as the best thing since hydraulics, but many felt it was costly and unnecessary. Some operators resented the suggestion that they needed software to be proficient.
The market has matured. OEMs offer a menu of packages from simple indicate systems to those nearing autonomous machine operation. Now customers are interested in getting the right package for their specific needs. Even seasoned operators appreciate the ease and convenience of machine control.
1D, 2D, 3D
The flagship model of Cat’s new next-gen excavators, the 330, comes with 2D Grade as standard. Through a touchscreen monitor, the system provides guidance for depth, slope and horizontal distance to grade. Grade Assist, also standard, automates boom, stick and bucket movements for single-lever, on-grade digging. Upgrades to Advanced 2D and 3D grading are available.
“In the simplest terms, 1D systems are designed to regulate single plane grade and slope,” Winemiller says. “2D systems regulate grade and slope with many variations needed on the work site. 3D systems regulate grade and slope dependent on the positioning of the machine across the entire work site, based on GNSS machine position, laser-guided sensors or total stations, and changing map and worksite topography.” Each level provides significantly more information, precision and functionality.
Aaron Kleingartner, marketing manager, Doosan Infracore North America, says a 2D system can maintain grade during backfill. “If the operator wants to add 8 inches of Class 5 gravel in a trench, the system can be used to do that and stay at grade.” With a 3D system, the operator can move and feed material anywhere on a jobsite. “3D helps sculpt and mold the site to plan. In a drainage system, for example, you can add and remove material to control where water comes from and where it goes.”
Now or later?
“The building blocks that allow a contractor to use a 2D system are the same as what is needed for a 3D system,” says Andrew Dargatz, Case brand marketing manager. This allows the customer to be conservative on the initial investment and upgrade later if conditions warrant. “A contractor should not fear investing in one system and then having it become obsolete when they’re ready to graduate to 3D.” That said, there are benefits to having the right technology in place at the time of purchase. “Taking delivery of the machine ready to go will get you up to speed faster, and you won’t have to take the machine out of rotation later to do an upgrade,” Dargatz says.
Mixed availability
John Deere and Hitachi have a Grade Reference Ready option from the factory. “This enables dealers and customers to choose the grade guidance or control offering that is best for their application and best for their pocketbook,” says Jonny Spendlove, product marketing manager, excavators.
“Select Hyundai excavators are ready for the installation of the Trimble Earthworks system, which has been calibrated and tested for Hyundai,” says Corey Rogers, marketing manager, Hyundai Construction Equipment Americas.
Link-Belt offers 2D Machine Guidance (MG) and 2D Machine Control (MC) as a factory option on only the 210 X4; it will be available on other models in the near future. “We started with the 210 X4 because it’s our most popular machine,” says Rob Dulaney, Link-Belt product marketing specialist. MG provides visual and audial cues to help the operator maintain the desired grade. MC automates movement of the
Volvo debuted Dig Assist on just one machine, the EC220E, at ConExpo in 2017. It will offer it on all crawler excavators, from the EC220E to the EC480E, soon and the company will add it to remaining full-size crawler models at least as an option later this year. It will remain optional on wheeled excavators, says McLean, “because wheeled models are popular with municipalities, and those customers are very price sensitive.” Dig Assist uses Volvo Co-Pilot and that system’s 10-inch high-resolution touchscreen.
The PC390LCi-11 is the latest model in the Komatsu lineup to have 3D, fully integrated machine control as standard. 3D includes giving the operator the ability to achieve grade anywhere on the jobsite without being limited to planar surfaces and benchmarks, says Sebastian Witkowski, product marketing manager, Intelligent Machine Control. He says Komatsu is seeing many first-time machine-control users starting with 3D and skipping over the 2D option. The 3D feature is now standard on all machines, from the PC210LCi-11 to the PC490LCi-11.
Komatsu says it is helping customers get the most from their Intelligent Machine Control system. “Customers have one point of contact for all their service questions through our Technology Solutions Experts program,” says Witkowski. “That’s true whether they’re inquiring about PM intervals or 3D machine control.”
Beyond intelligence
Rogers says Hyundai offers operators three means of interacting with their machines. Of these, push buttons have been around the longest; touchscreen monitors are newer; and haptic controllers are the latest development, a feature pulled from the automotive market. “The haptic remote control uses vibrations and pulses to guide the operator through menu selections for maximum convenience,” says Rogers.
Many features address safety. Hyundai has AAVM (All-Around View Monitoring) to provide a 2D, four-channel, 360-degree view around the excavator. Their IMOD (Intelligent Moving Object Detection) gives visual and audial alerts when a person or object is within 16.5 feet of the machine. An optional LED light package with two lights each on the frame and boom and three on the cab improve visibility, especially in low light conditions.
Gradall machines also have an advantage in that they’re designed to work with knuckles and tiltrotators. Adding these features to conventional excavators can reduce breakout force and affect stability, especially when working over the side, says the company.
Manufacturers are also making changes to their electronics in areas other than machine control. Link-Belt offers RemoteCARE on all properly equipped excavators, with no subscription fee. This means RemoteCARE follows the machine to the secondary market and beyond, adding residual value. Volvo excavators come with onboard weighing architecture; activating the feature requires only the purchase of a software package. Joysticks on Volvo machines have tiltrotator controls and outrigger and blade controls on wheeled models.
Andrew Earing, excavator product manager, Komatsu, says their proportional joystick controls make the most of advanced work tools. With a hammer, for example, control is more natural than the heel-and-toe method required with foot pedals. Diagnostics available through the in-cab monitor can provide information on more than 160 points, depending on the model of excavator.