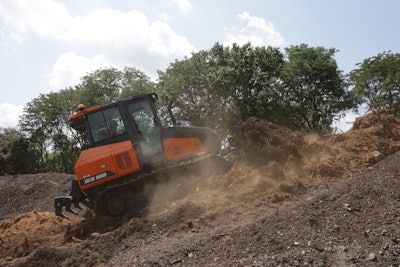
Dozers don’t spring to mind as the machines most likely to sport the latest technology, but recent models are bristling with advanced features.
Several manufacturers say their latest dozers are the best ever, touting such technology as operator-assist features, factory-integrated machine control and even remote-control operation.
But before we get into the new tech and take a look at the latest models on the market, we’ll start with some fundamentals to help you spec your next dozer.
Spec’ing the right dozer
Jeremy Dulak, product manager, dozers, Case Construction Equipment, says choosing the right dozer still means matching the machine to the fundamentals of the customer’s work.
“What type of work do you do?
“How large is your typical jobsite?
“What other equipment do you have and how will this dozer’s performance be best matched to those other machines?
“What’s the balance between fine grading and cutting?”
The most advanced dozer is the wrong dozer if it doesn’t match the customer’s work profile.
Derek Furr, product application specialist, Cat, emphasizes the importance of matching your dozer to your staff.
“Honestly assess the proficiency of your operators so that you can accurately assess the value of assist features.” He says Cat offers dozers from basic canopy models to fully configured machines, so getting the right set of operator-assist features is straightforward once a baseline of operator skill is established.
What about blades?
There are many styles of blades to match the many types of dozing applications. Some manufacturers leave blade choice to the customer as part of the spec’ing process. Others got with a standard blade, and customers wanting something else have to make a special order.
Matt Goedert, Deere solutions marketing manager for dozers and motor graders, says the company’s 750K, 850K and 950K have two main blade configurations with multiple sizes: a six-way PAT (power angle tilt), which is the more versatile of the two, and OSD (outside dozer) with push beams that transfer the load to the rear of the tracks and is good for heavy dozing and point loads, such as stump removal.
“In the OSD configuration, a semi-U blade is the most common,” says Goedert, “and provides both good finish grading and good carrying capacity.”
A full-U blade carries more but provides lower penetration and cutting force in hard materials and is most commonly used for working with processed materials. A PAT configuration adds versatility, with the ability to angle the blade to manage material and complete fine grading tasks, while still having the capacity for heavy dozing.
He says that because the undercarriage is such a large part of initial and ongoing costs, Deere offers three choices to match customer needs. The standard sealed and lubricated design is suitable for general dozing. The extended-life undercarriage uses bushings with an additional coating of harder wear material. The Maximum Life undercarriage uses coated bushings as well as heavier sprockets, rollers and idlers for the most demanding conditions. “The goal is to have balanced wear so that the dozer is taken out of service once for undercarriage service when all the components exhibit comparable wear, so customers get maximum life out of all the components.”
All hydrostatic-drive models from Komatsu, the D37 through the D71, come standard with six-way PAT blades, because they “provide the most versatility and control,” says Rafal Bukowski, Komatsu product specialist, HST dozers.
The Komatsu D65, a torque-converter model, has a sigma or semi-U blade, with a PAT blade on the waste model.
Don’t overlook the small dozer
The availability of advanced technology, such as Komatsu’s iMC 2.0, makes smaller models more capable.
“It’s a common misconception that bigger is always better,” says Bukowski. “But smaller models are more competent than in the past and are perfectly suitable for a large part of traditional dozing applications while providing lower operating costs and easier transportability than with larger machines.”
He points out that “smaller” doesn’t mean “small.” The D37 and D39, Komatsu’s smallest models, have operating weights up to 22,817 pounds and blade capacities up to 3.14 cubic yards.
Case: Machine control and the Minotaur
Case Construction Equipment offers factory-fit machine control on its 750M through 2050M dozers. The option includes factory-installed and calibrated 2D, dual-mast 3D and SiteControl CoPilot features from Leica Geosystems. The factory-fit approach simplifies initial investment by grouping the selected Leica system with the dozer into a single transaction. It also enhances residual value by offering the assurance of a factory-integrated system, Case says.Case Construction Equipment
As compact track loaders became larger and more powerful, there was concern they were stealing market share from small dozers. OEMs agree that if customers need a machine for dozer applications, a dozer is still the right choice. But for customers who want more versatility, a CTL with a dozer blade makes sense.
Case built the Minotaur DL550 with these customers in mind, says Jeff Jacobsmeyer, product manager for the DL550. While the DL550 looks like a CTL, it has a fully integrated C-frame like a dozer.
“The DL550 is a single platform that can perform multiple tasks and do them all well,” says Jacobsmeyer.
The 114-horsepower DL550 uses the same blade as Case’s 650M dozer; optional equipment includes a drawbar and a five-position ripper with three shanks. The vertical-lift machine has seven bucket and three track options. “If you plan on using a good mix of dozer mode, loader mode and attachments, the DL550 Minotaur is a great option.”
Cat Next Gen improvements
Cat has three models in its small dozer line: the D1, D2 and D3 (above). All have hydrostatic drive and Cat C3.6 engines with net power of 80, 92 and 104 horsepower, respectively. Operating weights are 17,855, 18,382 and 20,640 pounds with dozer blade, enclosed ROPS cab, operator and fluids. A three-shank, parallelogram ripper is available for all three. Each gets Next Gen updates.Caterpillar
Operator-assist features are software-driven and include such items as enhanced Smart Blade and traction control. By damping blade motion, Stable Blade allowed operators to produce a smoother surface when the blade was down. The enhanced Stable Blade provides comparable damping control with the blade in other positions.
The ARO (attachment-ready option) includes advanced Stable Blade and preparation for the addition of Cat Grade or Cat Grade 3D. A new blade-load monitor combined with Auto Carry prevents track slip, as does low-slip traction control for low-speed operations.
Cat Command remote control comes as line-of-sight (LOS) and non-LOS. A controller provides LOS control up to about 75 feet, depending on conditions. The controller is a “belly box” configuration.
Non-LOS is a complete station that communicates via Wi-Fi to control several machines with virtually unlimited range. Control can be manual or with Cat Grade 3D. Machines ship remote-control-ready; the actual remote control is installed by the dealer.
DD100: Doosan’s first dozer
The first Doosan DD100 is delivered in U.S.Doosan
The 9-metric-ton DD100 is targeted at the North American market. Production began in June 2022. Two additional machines have been shipped to the U.S. for final testing and product demonstrations.
Production on a second model, the new 13-metric-ton DD130, is expected around February 2023.
Standard features on the DD100 include an 8-inch Smart Touch display, rearview camera, LED lighting and front, rear and side wiper blades. 3D Machine Guidance and 3D Machine Control are options.
Dressta TD-15M and TD-25M models
The new TD-15M from Dressta has a two-speed steering drive that delivers 100% power to both tracks, allowing operators to push a full load through turns with maximum material retention. Single grouser tracks are available in seven sizes ranging from 20 to 37 inches wide. All five blade options can be equipped with hydraulic tilt and angle as well as manual blade pitch adjustment. Power is from a Tier 4 Final/Stage V-compliant Cummins B 6.7 rated at 232 gross horsepower.Dressta
Horsepower has been increased to 232 on the TD-15M and 375 on the TD-25M. Both are Tier 4 Final and European Stage V compliant and have Cummins engines with Dressta powershift transmissions providing six forward and six reverse speeds.
They can be spec’d with wide or long tracks, rippers with single or multiple shanks, landfill configuration and rigid or angle blades. Both models have new cabs featuring 33% more glass, left and right ergonomic joysticks, a 7-inch full color monitor and high-efficiency air suspension seating.
The mid-size TD15M is intended for customers working on roads, landscaping, forestry and landfills. The large TD25M is intended for heavy applications such as mining and quarries.
John Deere using feedback
The John Deere 950K has a PowerTech engine rated at 265 net horsepower and hydrostatic transmission. Operating weight is up to 73,700 pounds. Track on ground is 126.5 to 135.1 inches. Standard configuration is 43 single grouser extreme service shoes and 12-foot 10-inch blade with a 31-inch dig depth and 2-foot 7-inch tilt.John Deere
Deere also spends time in the field gathering insights from customers and dealers. “In some cases a customer or customer group has been involved in the development of a feature from concept to production,” says Goedert.
Part of the development process is to ask hard questions, says Goedert. “Does the feature provide value? Does it require operator education? Will it be apparent? That is, will the operator even be aware the feature is available for use?”
He says this process was key in developing Slope Control, an entry-level integrated grade control, as well as SmartGrade, the fully integrated 3D grade control system.
Komatsu iMC 2.0 is here
The D71PXi-24 from Komatsu has 240 horsepower and hydrostatic drive and benefits from iMC 2.0 features. With quick surface creation, operators can create a temporary design surface with the push of a button. Tilt steering control continuously and automatically tilts the blade to maintain straight travel. The two roof-mounted antennas receive signals from GPS, GLONASS, Galileo, BeiDou and QZSS to maintain blade accuracy even on slopes and under shadows from obstructions.Komatsu
Proactive dozing control is one feature of iMC 2.0. The machine learns as it works, collecting data from each pass to predict the most effective and efficient subsequent passes. This track mapping approach can deliver up to 60% greater productivity.
Another feature, track lift layer control, is used for maintaining consistency while spreading fill, which Komatsu claims can double production.
Komatsu’s new D71 has 47% better visibility ahead of the blade, 9% greater engine power and 13% more blade capacity than the D65.
The D71i-24 comes with all iMC 2.0 features including proactive dozing, lift layer control and tilt steering control.
Liebherr Generation 8 for greater grading
Liebherr’s PR 716 dozer has an operating weight of up to 34,830 pounds and a blade capacity of up to 4.07 cubic yards. The engine is rated at 125 horsepower (SAE J1349), and the hydrostatic drive is electronically controlled. Eco mode, auto idle and auto shutdown improve fuel efficiency and lower operating costs. The isolated cab, air suspension seat and touchscreen monitor provide operator comfort.Liebherr
Liebherr Active Sensor Control is standard and provides blade stabilization in all axes. Two independent integrated circuits use gyroscopic and inertial moment sensors for higher grading speeds and precise fine grading. Kits are available to expedite installation of 2D and 3D machine control systems from Trimble (Earthworks) and Leica.
Generation 8 dozers also features improvements for the operator. The cab is fully isolated from the machine base for dramatically lower noise and vibration. Climate control is standard. Access and descent lighting with delay provide greater safety in low light conditions. A 9-inch display is standard.
What about delivery times?
Sources agree that supply-chain issues continue to confound product availability.
Issues can be unpredictable, and there’s no definite end in sight.
All agree that customers’ best option is to work closely with dealers and develop a proactive plan for fleet management.