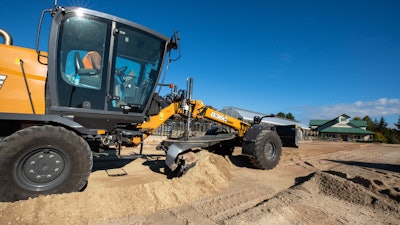
Conventional wisdom holds that motor graders are the most demanding of all machines on the jobsite. So it would seem graders would be first in line for technological advances to make operation easier. Often they are, but it’s not necessarily because they are complicated machines.
“I think as an industry we tend to overplay how difficult it is to operate motor graders,” says Nathaniel Waldschmidt, product manager at Case Construction Equipment. “Yes, it takes time and effort, but graders can be learned and mastered just like any other machine.”
He says it’s not the nature of grader operation that makes technology so valuable, but the nature of the work graders do, where technology can dramatically improve both production and accuracy. “In this competitive landscape, it feels like a no-brainer to incorporate technology” into grader operation.
Machine control is one of those technologies fit for a grader.
Case has two models in its grader catalog, the 836C (shown above) and 856C, and each leaves the factory ready to run machine control, says Waldschmidt. “Between graders and dozers, it’s these applications that machine control was really made for.” The factory prep allows easy integration of systems from Leica Geosystems, Topcon and Trimble.
Both Deere 872 and 872 GP (shown) feature Auto-Shift Plus for simplified operation that requires no inching pedal. The GP (Grade Pro) model includes multiple advanced automation features. Both are powered by John Deere PowerTech PSS 9.0L engines rated at 300 net horsepower. The Deere transmission provides eight speeds forward and reverse with 6WD in the first seven gears.John Deere
The Machine Presets function allows operators to program multiple functions into one button. To prepare for roading the machine, for example, one button tap can straighten machine articulation, raise and rotate the blade to its stow position, raise the rear ripper, activate the hazard lights and beacon and enable Auto-Shift.
The Auto-Shift Plus transmission allows the grader to come to a full stop in any gear without the use of the clutch and to restart with a press of the throttle. It also does away with the need for an inching pedal and performs automatic shifts in gears four through eight while roading.
SmartGrade is Deere’s latest tech advance. It is a fully integrated, mastless system that maintains accuracy while allowing the operator to control articulation, blade pitch and wheel lean as required.
SmartGrade-equipped models also support Topcon GPS and LPS systems while retaining the advantages of a mastless design.
“SmartGrade allows operators to run with no limitations, in any position, while grading with automatics,” says Matt Goedert, solutions marketing manager, roadbuilding, John Deere.
Powered by a 163-horsepower engine, the Komatsu GD655-7 grader features a two-mode, three-stage Variable Horsepower Control to match operating parameters to the application for improved performance and fuel savings. The new transmission shift lever allows fingertip selection of F-N-R. Refinements include a “right sized” steering wheel for use in roading, plus a new steering lever to provide low-effort fine control while grading.Komatsu
The GD655-7 comes configured for easy installation of the Topcon 3D-MC2 system. Standard steering includes both a steering wheel and armrest-mounted steering lever to match applications and operator preferences.
Experienced grader operators are rightfully proud of the complex skills they have developed over the years. So how welcoming are they of technology that simplifies grader operation?
“An expert operator will appreciate the tools that make tasks easier by automating some functions, so operators can focus on results and what is happening around them,” Repp says.
He adds that few, if any, other types of equipment have as many degrees of freedom as a grader, and automating some functions allows highly skilled operators to focus on tasks that demand their high level of skill.
Cat’s 140 GC is designed to combine high performance with low costs on small to mid-size jobs. The Cat C7.1 engine is rated at 196 maximum horsepower, and the automatic powershift transmission provides six forward and three reverse gears while eliminating the need for an inching pedal. The 12-foot moldboard and a host of attachments, including scarifiers, rippers and front blades, ensure versatility.Caterpillar
Levers were first; they were straightforward to use, and operator efficiency improved as muscle memory deepened over time.
Then M Series graders in 2007 introduced joysticks, which offered low-effort, intuitive, three-axis control, auto-articulation and grouped all major functions into two joysticks.
In 2018 the Next Gen machines arrived with the choice of levers or joysticks.
“Some operators, especially those with more experience, prefer the low effort of joysticks,” says Kohout. “Sometimes the preference is based on application.” Rough cutting favors levers, while finish work is best done with joystick controls.
Kohout says the right combination of technology helps combat the current labor shortage. Low-effort joystick controls enable older workers to remain on the job longer, and automated features bring new operators up in proficiency much faster.
A caveat: “Those new workers still need to learn to manage material and to understand how what they do fits into the total site.”
Cat 120 GC and 140 GC graders come with steering wheels and lever controls. Beyond that, these two models allow customers to choose features and technology à la carte.
The 140 GC, for example, comes with a standard seat; upgrades have mechanical or air suspension. Customers can move up from the base cab to a cab with HVAC or down to a canopy. ROPS/FOPS is optional. An on-demand fan is standard and a reversing fan is optional.
A no-spin differential is standard, while all wheel drive is an available option.
How important is AWD?
“It offers 40% more tractive effort than rear tandem drive,” says Kohout, “but also has higher initial and ongoing costs. The question is, does the boost in productivity offset the higher costs?”
Cat’s AWD provides steering speed compensation to minimize tire scrub in turns. On non-GC models it allows all drive to come from the front wheels only at speeds up to 5 mph, minimizing disruption of the finished surface.
Here again Kohout offers a word of warning. AWD emboldens some operators to run their graders like dozers, which they are not.
Repp points out that the majority of grading operations are performed with rear drive, even on graders with AWD.
“For a system that gets used only part of the time, there’s a lot of additional cost, wear, fuel consumption and maintenance.”
AWD does have its place in certain situations, “but it is not really needed the majority of the time. Justifying AWD comes down to how much additional you’re willing to spend and if it is actually required for the job at hand.”
Improved mechanics
Deere offers an optional Premium Circle on all graders with a sealed bearing and pinion for reduced maintenance costs and less downtime.
The design eliminates the need to adjust and replace wear inserts and provides 40% more circle torque and 15% more speed compared to the standard circle. The only required maintenance of the Premium Circle is to grease the bearing every 500 hours.
Case graders feature an A-frame drawbar with a heavy-duty boxed frame design to reduce lateral stress and extend operating life.
The saddle can be hydraulically set to five positions. Gooseneck geometry allows the operator to rotate the moldboard over 90 degrees for each working side with no mechanical interference.
Graders as snow removers
Kohout says the key to efficient snow removal with a grader is the proper outfitting.
“New wings and plows enter the marketplace often,” he says. “Know what advantages these new products offer.”
As snowfalls become lighter in many areas, mastless wings become more appealing. Modern snow tires may eliminate the need for chains, and some snow tires provide true all-season performance.
“Do you need a trip edge? Do your LED lights run hot enough to prevent icing of the lenses? Do you have the right beacons?” he says contactors should ask themselves.
“Graders are highly configurable for snow removal so make sure to do your homework.”
Dump trucks equipped with plows have the advantage of spreading deicing chemicals or grit while plowing, says Waldschmidt, but graders offer much better visibility to the clearing area. Graders are also more agile and, when equipped with snow wings, are better at shoulder clearing and moving snow farther off the road.
“Motor graders are wildly underrated for their efficiencies and capabilities in snow removal.”