Hamm’s new PH hybrid powertrain system for tandem asphalt compactors debuted earlier this month in Houston at World of Asphalt 2018, billed as a new concept that will save owners fuel, costs and maintenance.
Hamm introduced the hybrid powertrain system in the HD+ 90i PH tandem roller.
Expected to be available this year, the hybrid system underwent field trials in selected markets during 2016 and 2017 and is expected to be available in North America with double vibration (VV) and vibration-oscillation (VO), as well as the smooth drum-pneumatic “combi” rollers (VT) as options.
The hybrid solutions combine two power technologies: By combining an internal combustion engine with a hydraulic system, Hamm says it’s the first roller manufacturer to develop a technical solution suitable for series production.
For the first hybrid power models, Hamm chose the HD+ 90i, a popular tandem roller in the medium weight class. The previous generation of this roller was powered by a 114-horsepower (85 kW), Tier 4 Final diesel engine.
In this new hybrid power roller, brief peak loads are handled by a hydraulic system, enabling the roller to be equipped with a smaller 74-hp diesel engine while delivering the same performance as the previous model. The load on the diesel engine is also reduced in that the radiator fans are electrically operated for optimum efficiency.
Hydraulic system works like pumped storage power station
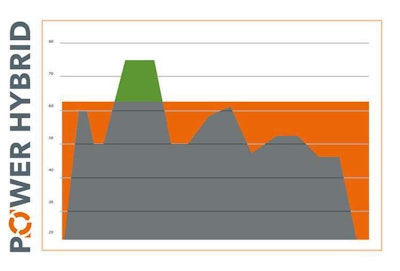
Hamm says the hydraulic system works rather like a pumped storage power station.
As soon as the power demand falls below the maximum load of the internal combustion engine, a pump fills the hydraulic accumulator.
If a lot of power is called for, such as when starting the vibration drive, the hydraulic system functions as an auxiliary drive to supply a maximum short-term load of up to 27 hp (20 kW).
Then, the cycle begins anew, refilling the accumulator. The principle functions optimally because for normal applications, the maximum load is always only called up for a matter of seconds. Afterwards there is sufficient time to replenish the accumulator.
Quieter, lower fuel consumption and less maintenance effort
The company says this results in numerous benefits:
- The 9 mt HD+ 90i PH roller can be powered by 74-hp (55.4 kW) engine in place of a 114 hp (85 kW) unit – and with the same compaction power.
- The smaller engine does not require an SCR catalytic converter or DEF fluid. This results in advantages in terms of handling and maintenance.
- The power train is markedly quieter.
- The hybrid power train, in combination with the electric fan, drives and a start-stop system result in savings of up to 15 percent in fuel consumption. This also “substantially” cuts CO2 emissions, the company says.