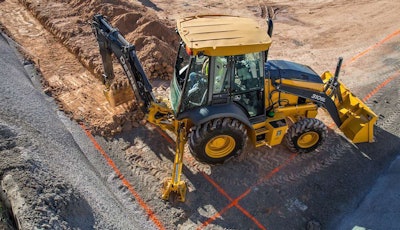
Productivity
Auto Smooth Ride is part of the Automate package; an equivalent is offered on most models from most OEMs. Settings for the feature on JCB machines are on, off or auto. “We recommend auto mode,” says Rafael Nunez, backhoe product loader marketing specialist, JCB. “Auto maximizes loading productivity while reducing spillage, and eliminating the bobble-head effect on drivers during travel.”
The optional Speed Selectable Automatic Ride Control on Case machines kicks in automatically when the machine is traveling at a specific speed. In addition to electronics-enabled productivity features, Case also offers hardware-based improvements. While typical lock-to-lock is three full turns of the steering wheel, optional Comfort Steer cuts this in half, allowing the operator to maneuver more quickly and efficiently. Case ProControl is a swing-damping feature that eliminates rebound on the backhoe. “ProControl reduces wear on components, lowers fatigue and provides greater precision for the operator,” says Katie Pullen, Case backhoe brand marketing manager. Optional Power Lift increases the hydraulic capacities of the boom and bucket forces, allowing the machine to lift up to 8 percent more.
Operator environment
Caterpillar’s F2 Series backhoes have a new cab, which features several storage locations and great visibility, says Sherrie Williams, Caterpillar backhoe marketing. “Loader joysticks with differential lock are located at the operator’s finger tips and the 420 and 430 single-tilt machines now have a thumb roller to operate the auxiliary functions.”
Nunez says the seat-mounted pilot controls in JCB backhoe loaders is an important piece of the operator environment. With seat-mounted controls, the operator no longer has to hunch over floor-mounted backhoe controls. The challenge was to run pilot hydraulic lines that would swivel with the seat.
Along with a spacious operating area and ergonomic controls, Case offers traditional three-stick controls. “Case is one of the few manufacturers to still offer a three-stick control, in addition to pilot controls,” says Pullen. “A lot of operators still prefer this configuration, because it’s how they learned to run a backhoe. It allows them to control the boom and bucket with one hand, and operate the steering wheel with the other. It is important for experienced operators to be able to run the machine in the way that is most familiar and comfortable to them without having to relearn the controls.”
Serviceability
Ernie Ferguson, division sales manager of compact equipment, Terex Construction Americas, says the key to serviceability is to stay on schedule with daily and weekly checks, as well as regular PM intervals. Because daily checks are essential to finding little issues before they create major problems, all service points have easy ground-level access, and the hood tilts fully open on Terex backhoe loaders.
Ferguson also recommends doing an annual review of maintenance records to spot any patterns. “It’s important to look at what components are failing, and to determine why, how, and when they failed, as well as to know which components are holding up over time to analyze those trends.”
Ferguson notes that Tier 4 Final affects serviceability because engine design and horsepower category can affect service procedures. “Terex does not manufacture engines, so we have the flexibility to evaluate the compliance solutions offered by multiple manufacturers and select the best technology for each machine application, according to the way our customers use the machines.”