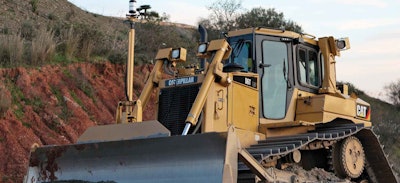
Big machines often see upgrades and new technology first, since the cost of introducing these features represents a lower percentage of the overall cost. But as OEMs become more adept at configuring these features and the costs drop, these features begin to move to smaller machines.
Dozers in the 105- to 210-horsepower class are benefitting from this trickle-down of features and technology. That’s welcome news since these machines are in high demand for a wide range of applications including site prep, land clearing, material handling, recycling and waste management, and forestry.
Leveraging electronics
One of the key enabling technologies in this migration of features is electronics. Jon Gilbeck, crawler dozer global marketing manager for John Deere Construction and Forestry, emphasizes the multiple ways that electronics benefit customers. Telematics, such as John Deere’s JDLink, provide more information, which Gilbeck says, “helps customers work smarter and saves them money.”
Bruce Boebel, dozer product manager for Komatsu, points out that the features can be scaled to meet individual customers’ needs. While larger contractors may opt for a continuous data feed, smaller customers typically want only alerts and higher-level data.
The information provided by telematics can be simple or intricate, says Brad Stemper, brand marketing manager for Case Construction Equipment, which will introduce its M Series dozers to North America later this year. “The key is to get the right level of detail so that the information makes sense to customers and delivers what they want.”
As advanced electronics become standard on dozers in this class, more machines are grade-control-ready from the factory. With wiring, controls and hydraulic systems all prepared to integrate with grade control, the addition becomes true plug-and-play. This greatly reduces the cost of adding grade control if you choose this option. Grade control improves productivity and precision for all operators and is especially beneficial to operators with less experience. A growing number of government entities require grade control when requesting proposals for work.
Grade control is also enhanced by basic design elements. The outside dozer blade on Deere’s 850K, for example, has a 3-hole blade pitch with screw-type fine-tune adjustments for infinite settings.
Hardening of electronic components has been around for a long time, from when engineers first spec’ed potted switches and ruggedized printed circuit boards, yet electronic components continue to become more robust. One example is Deere’s Sealed Switch Modules (SSMs). As the name implies, the switches are sealed to protect them against moisture, dust and debris. What sets SSMs apart from other hardened electronics is their multi-functionality. The switches enhance anti-theft by prompting the operator to enter a four-digit code before the machine will start. Idle time before auto-shutdown, which can be set by the operator, is controlled by an SSM while another delays shutdown until sufficient cooling of the turbocharger has taken place. Most switches in the cab, including the ignition switch, have been replaced with SSMs.
Electronics also enable total machine control by which the operating characteristics of the machine can be tailored to the operator’s preference. Changes are made by navigating through the monitor in the dozer’s cab. Settable performance characteristics include aggressiveness, decelerator response, FNR shift rate, steering rate, steering modulation and forward/reverse speed.
Undercarriages and hydrostatic drive
Because undercarriage costs are a disproportionate part of total owning and operating costs on dozers, OEMs have worked hard to reduce those costs. At the core of their efforts are the elimination of the need to turn pins and bushings to maximize service life. Other steps have been taken to reduce life cycle costs.
Deere’s Max Life undercarriages feature larger components with more wear material and include SC-2 coated bushings. Testing showed these bushings offer wear life up to two-and-a-half times longer than that of hardened steel bushings.
Boebel points to Komatsu’s PLUS (Parallel Link Undercarriage System) as their approach to longer undercarriage life and reduced owning and operating costs. Key features of the PLUS design include extra seals, rotating bushings, increased wear material, and greater depth of hardening.
Caterpillar’s SystemOne undercarriages feature lifetime-sealed and lubricated cartridges. For severe duty applications, where abrasive conditions or high-impact applications are common, Cat offers a heavy-duty undercarriage.
Hydrostatic drive is common in dozers in this size class. Gilbeck says benefits include superior fuel economy to alternative mechanical solutions, infinite speed control, power management, live power turns, counter-rotation, dynamic braking, and hill hold. The results are high efficiency and ease of operation, even for less-experienced operators.
The Liebherr hydrostatic drive is a sophisticated system that enhances the inherent benefits of such a system, according to Robert Klima, product manager for Liebherr. Pumps and motors are electronically controlled. Motors are variable-displacement axial piston type, and pumps are variable-displacement piston type. They can turn at maximum speed with zero output, which means they operate at peak efficiency regardless of system demands, and that full output is available at any time. There are no gears, clutch, forward, neutral or reverse; everything is controlled by fluid direction and volume. Because there is no mechanical connection, shock loads to the drive are damped out by the hydraulics, which reduces noise, vibration and harshness and prolongs component life.
Liebherr uses a splitter from the engine’s crankshaft to run two or more pumps side-by-side instead of in series. The splitter is slightly overgeared so the pumps turn at a higher speed than the engine. This allows higher pump speeds at lower engine speeds, typically 1,800 rpm.
Shopping list
It’s important to start with the basics when spec’ing out a new machine. Those basics are weight, horsepower and drawbar pull, according to Case’s Stemper. All three work together to deliver performance. Track shoe width must be matched to the underfoot conditions. Also on the list of basics is operator comfort. Ergonomics; noise, vibration, and harshness; low-effort controls, improved visibility and sight lines all play a role. “Comfortable operators tend to be productive operators,” says Stemper.
While customers give a lot of consideration to the blade of a dozer, some overlook the other end of the machine. Rear implements include rippers, winches, drawbars and counterweights. Spec’ing the rear is important to the overall package. For example, Cat’s D6T requires a rear counterweight be used with their VPAT blade if no other rear implement is installed.
As contractors expand the type of work they do and the geographical area they serve, the size and weight of equipment must be added to the list of basics, says Dave Cusac, global track-type tractor application specialist for Caterpillar. “Machine models and configurations are often selected solely based upon transportability. These machines are moved from job to job more frequently in today’s environment and haul permitting can be both time-consuming and costly.” He says road construction, wind farm contractors and especially petroleum pad builders are among those who are most affected by transportability.
Komatsu’s Boebel offers guidance for those seeking to optimize machine size in order to stay healthy in a difficult economy. “Machine size is becoming a big factor as customers diversify to stay solvent,” he says. “Long-term strategy and risk play roles here.” Customers should ask themselves hard questions. Do I have enough volume to justify a bigger machine with its higher owning and operating costs? Should I stay in a niche and turn down work outside of that niche? Answers aren’t likely to be black-and-white. The point is to make buying decisions based on a well-considered business plan.
Features that make life easier are becoming standard. These include single-side service points, many accessible from ground level; hydraulically-driven, reversible fans; and a cooling package (or at least the fan) that tilts or swivel for improved service access. When ROPS is designed into the cab rather than provided as an add-on, visibility is improved.
Living with Tier 4
Boebel suggests customers see what’s included beyond the initial Tier 4 price increase. For example, Komatsu’s complementary planned maintenance goes for 3 years or 2,000 hours and includes up to two swap-outs of the diesel particulate filter in the first five years. To appreciate the impact of Tier 4 on their operations, customers need to understand active and passive regeneration, the regen method used by the machine and the regen patterns including the ratio of active and passive regen of the models they’re considering.
Not all Tier 4-compliant dozers rely on DPFs. Komatsu’s 105 hp D39-23 uses a diesel oxidation catalyst and exhaust gas recirculation to meet the standards. Also contributing to the low-emissions performance are a variable flow turbocharger, direct flow air filter, high-pressure common rail fuel injection and a 16-valve cylinder head. Cat’s D6T has the company’s C9.3 ACERT engine. ACERT Technology features their NOx Reduction System, which is cooled EGR, and Clean Emissions Module (CEM), which puts a DPF and DOC in one compact package.
Regardless of how a particular machine meets Tier 4 requirements, there will be an effect on customers’ owning and operating costs and on their preventive maintenance program. Since there is no standardized approach to meeting requirements, it’s important to understand the impact of the emissions control system on the machines you’re considering. Dealers are good sources of information on the matter, but so are other contractors. Boebel encourages customers to communicate with their peers. “Talk to other customers and lean on their knowledge.”