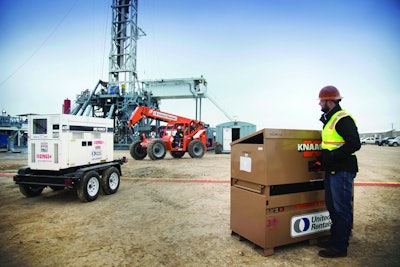
Do you know where all your tools are? It’s not such a simple question to answer given the daily variables and moving assets (human and inanimate) on a construction jobsite, compounded by external forces such as weather and change orders. Tools also break or get lost and some “walk off,” only to appear the next day on eBay.
Small-tool management may seem like the smallest problem on your plate, but in a $12 billion market of owned and rental tools, underutilization stacks up to an industry loss of $1.73 billion, according to data from United Rentals’ (UR) Tool Solutions division. The absence of accountability for tools accounts for industry losses of $1.2 billion, says the company.
And when you lose track of tools, you can wind up buying or renting more than you need, going over budget and losing money.
“Underutilization is one of those silent killers when management doesn’t have the right visibility and transparency to know what’s being utilized and what’s not,” says Adrian Gram, director of sales and marketing at UR Tool Solutions.
Tracking technology—now and next year
UR recently overhauled its tool-management software, Tool Trailer, which is part of its Total Control worksite management software. UR customers now have access to real-time jobsite location and utilization for their assets.
The tool-tracking software is ideally suited to large construction and industrial projects, and the service incorporates a UR Tool Solutions staff member performing the tool management function for the customer/contractor. “The tool rooms and trailers are all operated by a subject matter expert, so the customer can focus on building rather than managing tooling and equipment,” Gram says.
There’s more coming, UR says, including Bluetooth tracking for their existing custom-stocked and ProBox offerings, planned for next December. “All the tools inside the new ProBox will have a Bluetooth chip on them,” Gram explains, “creating a smart inventory management system for customers so they don’t have to manually track tools on a piece of paper,” Gram explains. (ProBox is a gang box stocked with tools and supplies specific for and delivered to a project.)
UR says an advanced ProBox will bring tool visibility to smaller jobs that don’t require a full Tool Trailer solution. As it’s now envisioned, three “gateways” will work together to simultaneously monitor tool location and utilization: cellular (i.e. from a manager’s phone), Bluetooth from the ProBox and GPS telematics on UR rented equipment will all detect small tools throughout the worksite like invisible tool spies. All that data will feed into real-time, mobile reporting so managers always know what they’ve got, where it is and whether it’s in use.
“When you employ all three gateways not only do you have the individual superintendent or United Rentals employee using their phone, but you also have a fixed gateway inside that job box telling you what is and is not in the box and then you have our equipment operating around the jobsite,” Gram says. “The scissor lift will recognize that drill over in the corner and all three gateways work in harmony.”