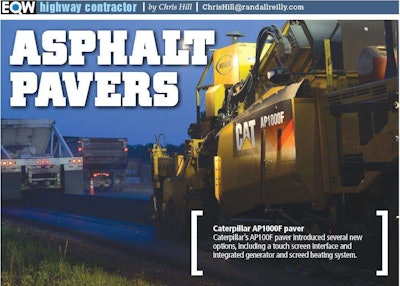
When you boil it down, not much has really changed about the asphalt paver. It’s still a tractor laying down and spreading material as it travels. But that simple principle required a lot of setup, skill and man-hours to perform.
So the changes in the equipment over the years have progressed with the goal of reducing each one of those three variables.
In the past few years, several OEMs have turned up the focus on the operator and the support crew. Controls are more clearly marked and backlit for improved visibility for the operator up top. There also are more control options for crew members working on the screed platform.
“There’s a good ease of operation for the operator,” says Dan Maitland, equipment operations manager for Ajax Paving Industries, which uses a Volvo P7170 paver in operations in Florida. “The screed setup we like because it’s fairly easy for the operators and for the crew. About 30 minutes in the morning and they’re up and running.”
Maitland says the newer machines are a nice fit into the company’s operation, as they closely monitor reliability and cost over the lifecycle of a machine.
“Pretty much for me what I look at is the cost of ownership throughout the life of a paver. Here at Ajax we typically run about a five-year lifecycle, maybe 5,000-6,000 hours on a particular paver, then we’re switching to another paver.”
There’s increased comfort for the operator in the seat and much more visibility, with control positions on the left or right of the machine, and sloped styling to allow better line of site. Screeds have been updated, with faster heating options and vibration, which provides more compaction at the back of the machine, and thus requiring less work from roller operators.
And the advent of 3D paving has provided more “paving to design” options and has increased accuracy and cut down on the need for stringlines, particularly with grade and slope control options.
“We’re continually upgrading our equipment and try to keep it as new as possible,” says Mark Bettis, vice president of Bettis Asphalt & Construction in Topeka, Kansas, whose company uses Caterpillar AP1055F pavers. “It’s become quite important with the technology.”
Here’s a look at some of the new asphalt pavers and features from some of the manufacturers:
Vögele
Wirtgen Group’s Vögele Super 2000-3i asphalt paver features Euro styling, which offers a more contoured front, aiding the operator’s line of sight.
It features a basic width of 10 feet and a maximum paving width of 28 feet. Designed primarily for highway construction and large-scale commercial applications, its top placement rate is 1,540 tph. The machine is powered by a 6-cylinder, Tier 4 Final Cummins QSB6.7-C250 engine rated at 250 horsepower. A new ECO mode lowers fuel consumption with 234 horsepower still at the paver’s disposal.
Operators will find a new console mounting system, making left and right shifts of the console on the operator’s stand easier. Vögele’s Niveltronic Plus Leveling System handles automatic grade and slope control and the machine features the new ErgoPlus 3 operating system complemented by a large color display.
Paver controls are “clustered in logical groups,” Vögele says, and buttons on the ErgoPlus3 console are easily identifiable by touch, even when wearing work gloves. The ErgoPlus 3 operating consoles were completely redesigned for this machine, and two remote controls for each side of the paver can be used as well.
Vögele’s VF 600, VR 600 and AB 600 TV screeds can be mounted to the Super 2000-3i. The VF 600 screed, which uses unequal-width front-mounted extensions for multi-variable width applications, has a maximum paving width of 25 feet and 6 inches with bolt-on extensions. The VR 600 screed has rear-mounted extensions for main line applications, providing maximum paving width of 28 feet with bolt-on extensions.
And the AB 600 TV screed, with rear-mounted extensions, achieves higher compaction thanks to integrated vibration and tamper. The screed is designed for placing cold reclaimed asphalt pavement for road base or polymer modified asphalts. Its maximum paving width is 27 feet 11 inches with bolt-on extensions. Electric screed heating is standard on the paver and typical heat-up time is 20 minutes.
Roadtec
The company’s RP-170e, a rubber-tire 8-foot highway-class paver, features a 6-foot 4-inch wheelbase designed for high maneuverability, ride quality and traction. It’s the smallest machine in the company’s paver line, with a hopper width of 10-feet, 5-inches, and a shipping width of 10 feet 6 inches.
The wheelbase design allows for a tight turning radius of 30 inches, which the company says will be ideal in “congested sites and space-restricted urban areas,” such as around barriers and drains.
While it’s a small paver, it offers big machine operator comfort features. As with the company’s other pavers and material transfer vehicles, the RP-170e offers the FXS fume extraction system that redirects away from the operator fumes emitted by the asphalt mix.
The machine also features Roadtec’s Comfort Drive operator system designed to be more ergonomic and provide unobstructed views. The system offers fingertip controls and switch and buttons placed on the armrest. The RP-170e also has dual operator stations that can swing out beyond the sides of the machine so the operator can see the side of the machine, the material tunnel and the back of the screed.
The paver also can be fitted with Carlson screeds, including the EZ-IV and EZ-V front mount screeds and the S-8 standard wedge-lock screed or the Eagle 8 rear extendable screed. All of the screed options are electrically heated and vibratory.
Volvo
Volvo’s highway-class P7110B (tracked) and P7170B (wheeled) pavers feature Tier 4 Final engines, 360-degree operator visibility and multiple control positioning options.
The company changed the engine’s position so it could keep the hood height and machine profile low to provide a 360-degree view. While doing this, they made the top cover longer and added a removable side cover to make the machines easier to service.
For the operator’s benefit, the two machines feature left and right consoles that rotate, tilt and extend beyond the edge of the paver. Engineers designed the seats a bit higher as well, raising them by 1.5 inches to provide additional line of sight. And to help with visibility even more, Volvo updated the two point indicators so they can be read from the paver operator station or the screed operator’s position. Volvo also included side air vents to reduce heat build-up around the operator area.
The company designed two-stage, 42-inch hydraulic tunnels for improved head-of-material control without bolt-on extensions. Screed options include the Omni 318, Omnio 1000 or Ultimat 200 and dealer-installed Wedgelock options.
Volvo’s CareTrack telematics system is also available as a factory-installed option on the P7110B and P7170B.
Atlas Copco/Dynapac
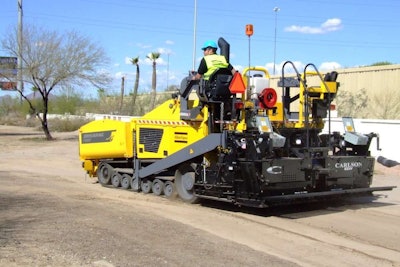
Atlas Copco has updated is Dynapac F1000 series pavers with the F1000W wheeled model and F1000T tracked model, with a center auger drive system option and a hydraulic tunnel extension system.
The center auger drive offers a chain box with a width of 6-inch and 17-inch diameter flights, enabling uniform material flow and reducing centerline segregation. The company says the system is best for high-speed paving work and work involving pavement width changes periodically, including highways, city streets and large parking lots.
The new hydraulic tunnel extension is 22 inches wide and automatically retracts as screed extensions retract to avoid collision. Atlas Copco says it reduces excess head of material in the tunnel and keeps asphalt from escaping into track components.
Additional features on the F1000 series include dual operating stations that swing out to the side of the machine, gas-spring hinged doors for access to the hydraulic systems and engine components, and Carlson front- or rear-mounted screeds.
The company also has recently made its FleetLink telematics system available in two packages, one for small pavers and one, FleetLink Advanced, for large highway-class pavers.
Contractors can use the system to set up maintenance schedules, with reminders sent via email when a machine is getting close to its next service due date. It also features a geo-fencing option to track equipment location. In the advanced package, users can look at the service status of all the machines in a fleet.
The basic package works on pavers up to the F1200C, and the advanced package works on the F800T, F800W, F1000T and F1000W.
Caterpillar
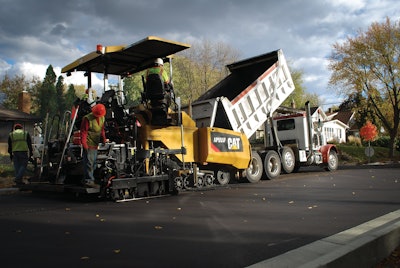
The company’s AP500F/555F and AP300F/355F, in wheeled and tracked versions, are the latest in its F-series asphalt paver line that includes the AP1000F/1055F and AP600F/655F.
The largest of these new models, the AP500F/AP555F, features an ECO mode that matches the engine speed to high load demands or when additional cooling is needed. Like the previous F-series pavers, it features a screed-heating system powered by an integrated generator that brings the screed up to temperature in roughly 15 minutes.
These models also offer control options via a new color touchscreen display. The display offers access to more control options compared to the usual switches, but operators can use either the display or the switches to operate the machine.
Additional flexibility is available through dual controls from either the operator’s or screed platform for ratio control of the conveyors and for mix height adjustment. Cat also has made a pendant control available for an operator to use while walking alongside the paver.
The AP500F/AP555F can be fitted with two screeds, the SE50 V that is vibratory only, and the SE 50VT that offers vibration and tamper-bar action.
The mid-size AP300F and AP355F offer an ECO mode (also available on the AP500F/AP55F), auto-fill feeder system and single-touch feeder system activation along with the touchscreen console and the screed-heating system.
The AP300F machines also feature a warm-up/clean-out mode that operates the feeder system at a reduced speed for quicker wash-down. This feature also lifts the auger for easier transport.