How the construction team for Minnesota’s Highway 23 Paynesville Bypass completed this project ahead of schedule despite truncated work season.
As with many of the older roadways in the United States, increased traffic has made them congested and ultimately unsafe. Minnesota State Highway 23 is one roadway facing the dilemma of too much traffic for a route that has been in existence since the 1920s.
The 343-mile highway, located in central Minnesota about 80 miles northwest of Minneapolis, is the second-longest state road in the state. It serves as a major connection between the area’s residents and employment centers, as well as being a key recreational and tourist access route.
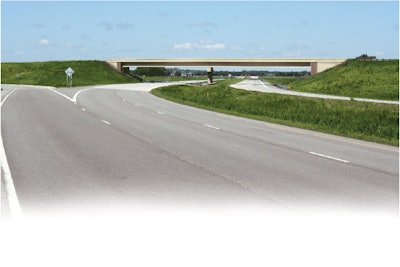
To improve mobility and safety for motorists traveling along the Highway 23 corridor, the Minnesota Department of Transportation (MnDOT) embarked on a project to extend 7.7 miles of the divided highway. Work began on the Paynesville Bypass project in mid-April 2010 and was completed in July 2012. Along with the construction of a four-lane divided bypass, the project also included grading, construction of eight bridges, surfacing and lighting.
Quarry next door
To procure materials for the project, the contracting company, KGM Contractors Inc., worked with Cold Spring, Minnesota-based Kraemer Trucking and Excavating Inc. It turned out that the trucking and excavating company didn’t have to look any further than its own backyard for the raw materials.
Several years ago, Coldspring, headquartered in Cold Spring, began a quest to understand how its business impacted the environment and the communities it serves in its quest to become the greenest stone manufacturer in the world. Natural stone is often considered an environmentally preferable material due to its durability, minimal processing needs and local availability in many markets. Coldspring’s Quarry Materials Division uses quarried materials that are not suitable for dimensional stone applications to create jetty, rip-rap and aggregate.
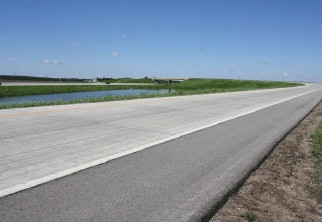
This extracted stone works well for use on construction job sites by excavating companies, contractors, landscapers and trucking companies. Applications for the extracted stone include all construction aggregate uses including concrete stone, bituminous mixtures, road bases, rail sub ballast and ballast, erosion control, shore protection and dam reconstruction.
Coldspring was able to supply and deliver the open-graded asphalt base (OGAB) needed for the project. They had a good source of high-quality granite that was only 15 miles from the project site.
Meeting the needs of a local market
The Highway 23 project required 43,000-tons (the equivalent of 2,150 truck loads) of granite aggregates from multiple quarries. The granite aggregate was provided in sizes from 3/8 inch to 1 inch.
The stone was used to build an 8-inch base of rock for the Paynesville bypass. It formed a drainage layer to remove water and minimize cold weather frost issues, and was placed directly below the new highway. Concrete was then poured on top of the open-graded base. The granite was sized to provide an interlocking base that was workable and significantly more stable than other locally available gravel base materials. With granite aggregate as a base, edge drains and overall drainage are maintained throughout the pavement life, which minimizes the possibility of concrete breakage and cracking.
Kraemer Trucking crushed the material to meet the project’s specifications. The company performs residential and commercial site work, as well as municipal projects including street construction and has worked with the aggregate supplier on a myriad of projects throughout the past 40 years.
Working ahead of schedule
One of the major challenges on this project was a very tight timeframe. Because of Minnesota’s weather challenges – a winter season that can last for six months – the season to complete road projects is small.
Project timelines and scheduling meant the OGAB had to be delivered at a high rate to keep the project on schedule, says Chad Kraemer, president of Kraemer Trucking. To accommodate the excessive truck traffic, this meant Coldspring had to keep its gate hours open as long as needed to deliver the daily quantities needed to keep the project on schedule, he said. “To keep the trucks rolling, most work days would start at 6 a.m. and end at 8 p.m.”
Adding to the timeframe challenge, the project faced a month-long shutdown due to the non-ratification of the state budget, which caused all government activities to cease operations. Yet, even with the shortened work seasons and the government shutdown, the Highway 23 Paynesville Bypass was completed more than a month ahead of schedule.
A team effort to make strict standards
MnDOT’s strict standards meant that a granite product had to be produced that would meet the road agency’s tough gradation specifications. It was paramount for the contractor on this project to be selective in the feed of material to produce specified material for the project.
Now travelers on Highway 23 have a safer, less-congested route between Willmar and St. Cloud, Minnesota. The aggregates producer was able to serve as a valuable partner to the contactors by providing the aggregate, from a nearby processing facility, at the density and durability required.
Article and photos are courtesy of Cold Spring (coldspringusa.com).