Whether it’s dense-graded, open-graded or gap-graded mix or stone-matrix asphalt, don’t forget their impact on compaction.
Dense-graded mixes are produced with continuously graded aggregate. In other words, there are a variety of sizes of aggregates in the design. The design formula includes asphalt cement and fines. Typically, the larger aggregates are surrounded by a matrix of mastic composed of asphalt cement and fines. The asphalt cement may be modified by materials such as polymer or latex rubber to develop additional stiffness.
Because the larger aggregates are surrounded by the mixture of asphalt cement and fines, there is less danger of damaging aggregates through the use of high-compaction force. Depending on the layer thickness, medium to high amplitude is often selected when compacting dense-graded mixes.
Dense-graded mixes
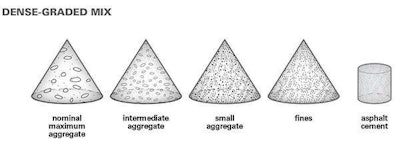
Dense-graded mixes are often classified as either coarse or fine. Coarse mixes have a maximum aggregate size of 19 mm (3/4 inch) or larger. Coarse mixes are usually laid down in fairly thick layers of 75 mm (3 inches) or thicker. Mats that consist of coarse mix are less likely to move around under heavy compaction energy. You can use vibratory compactors in higher amplitude ranges and pneumatic compactors with higher ground pressures.
Some dense-graded mixes are classified as fine mixes. Fine mixes have a maximum aggregate up to 13 mm (1/2 inch) and typically a fairly large percent of fines and asphalt cement. Some fine mixes can be unstable during the compaction process, especially if layer thickness exceeds 50 mm (2 inches).
Static compaction may be needed to help stabilize fine mixes prior to vibratory passes. High-compaction energy can damage layers of fine mix. Lighter compactors, either steel drum or pneumatic, are recommended for use on fine mixes.
Open-graded mixes
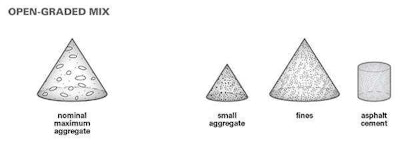
Open-graded mixes have relatively uniform-sized aggregate typified by an absence of intermediate sized particles. Mix designs typical of this structure are permeable friction layers and asphalt-treated permeable bases.
Because of their open structures, precautions are taken to minimize the amount of asphalt cement draining to the bottom of the layer by using modified asphalt cement, usually latex rubber or fibers. Stone-on-stone contact with a heavy asphalt cement particle coating is typical for open-graded mixes.
Gap-graded mix
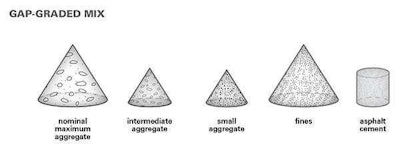
Gap-graded mixes use an aggregate gradation with particles ranging from large to fine with some intermediate sizes missing.
Gap-graded mixes are also typified by stone-on-stone contact and are more permeable than dense-graded mixes.
Stone-matrix asphalt

Stone-matrix asphalt (SMA), like other open-graded mixes, will be missing most intermediate aggregate sizes.
However, stone-matrix asphalt mixes have a much higher proportion of fines. Modified asphalt cement combines with these fines to produce a thick mastic coating around and between the large aggregate particles.
Shape matters, too
Aggregate shape also affects compaction. The shape of the aggregate determines the amount of internal friction between the particles.
Rounded aggregates have low internal friction and move closer together within the layer under less compaction energy. However, mixes with rounded aggregates tend to be unstable and move around under the weight of the compactor. Therefore, when you know the shape of the aggregate is rounded, select low vibratory amplitude or a light static compactor.
Angular aggregates, on the other hand, have high internal friction. Once they are moved into contact with each other, angular aggregates produce high pavement strength. More force and heavier compactors are needed to overcome the internal friction between the fractured faces of crushed stone aggregate. Most high-traffic mix designs specify the use of crushed aggregates with a certain number and shape of fractured faces.
The role of thickness
No matter what type of mix or what type of project, an important factor is the ratio between the size of the largest aggregate in the mix and the thickness of the layer. This ratio strongly affects the ability of the mat to accept compaction energy and reach the specified density.
For example, a layer thickness of 10 cm (4 inch) and a maximum aggregate size of 25 mm (1 inch) are relatively easy to compact. You can use high compaction forces and not worry about damaging aggregates. With a 4:1 ratio, there is ample space for aggregate movement allowing the aggregates to re-orient. Many public works departments specify a 3:1 ratio as a minimum for high-traffic mix design.
When the ratio of layer thickness to aggregate size is less than 3:1, the compaction process is much more difficult. In particular, when there are angular aggregates in the layer, it is likely that those aggregates will not move into the proper compacted orientation without being damaged.
The compactor operator is more likely to notice drum bouncing or the appearance of uncoated rock at the surface of the mat. Lack of density and damaged aggregates will lead to premature mat failure. When the ratio of layer thickness to aggregate size is less than 3:1, low compaction energy is needed.
In summary, crews will always need to monitor temperatures.
But, don’t forget that what happens before the mix even reaches the jobsite has an impact, too. v
Article and photos courtesy of Cat Paving.
(Editor’s note: This excerpt first appeared in “The Cat Paving Products Guide to Asphalt Compaction.” The book is available on Amazon.com and through participating Cat dealers.)