Noise emissions are as much of an environmental problem for urban trafficways as exhaust pollution, but new research is showing how sound wall performance can be improved, and how traffic noise can be mitigated.
Decades of research have shown that blendings of noise wall, the right choice of vegetation, and low-noise pavements such as the Next Generation Concrete Surface (NGCS), or asphalt open-graded friction courses (OGFCs), will suppress traffic noise much better than any one of those elements by itself.
Sound barriers are of different compositions, including metal, wood and recycled plastic fabricated to resemble wood, but precast concrete is by far the preferred material, as it’s durable and can be cast into any kind of aesthetic form, including locally significant iconography.
But the costs of sound walls vary widely, and they’re always expensive, ranging from $2 million per linear mile in Indiana (2014), to an average of $3.9 million per mile, according to 2009 estimates by the Washington State Department of Transportation , with lower costs for rural barriers, and higher for urban. The cost – versus the number of entities to benefit – is a factor in whether they are constructed at all.
Last year’s National Cooperative Highway Research Council Report 738: Evaluating Pavement Strategies and Barriers for Noise Mitigation attempts to reconcile today’s “quiet pavements” with the current federal law, which doesn’t take them into consideration when mitigating traffic noise.
“Title 23, Part 772, of the Code of Federal Regulations requires that noise analysis be performed for specific types of projects when potentially impacted receptors are present,” NCHRP 738 says. “This regulation identifies several noise mitigation measures but excludes pavements as a noise abatement measure. Recent advances in quiet pavement technology have shown the potential for using such abatement technology as an alternative to noise barriers. However, issues such as cost, maintenance requirements, and the ability to maintain noise reduction features throughout time need to be addressed when considering quiet pavement technology.”
Based on the results of the evaluation, a methodology that uses on-board sound intensity [OBSI] data to quantify the noise levels of existing and future pavement projects was developed, including their performance over time. The methodology also considers modification of the Federal Highway Administration’s Traffic Noise Model (TNM), used to predict future highway noise resulting from capacity improvements, and life cycle cost analysis to evaluate the initial cost of abatement and cost of maintaining that performance over the life of the project.
Download this important new document by searching for “NCHRP 738” on the web or by going to https://onlinepubs.trb.org/onlinepubs/nchrp/nchrp_rpt_738.pdf.
To build or not build?
Today, noise barriers are constructed for what are termed Type I highway projects, defined as either construction of a highway on new location, or the physical alteration of an existing highway which significantly changes either the horizontal or vertical alignment, or increases the number of through-traffic lanes.
As agencies don’t want to build noise walls that don’t serve enough residents, parks or businesses to make them worth building, the walls must meet feasibility criteria. An environmental review is required for Type I projects, and, using the TNM, if a significant future reduction in sound can be attained at a number of observation points (“receivers”) at or near buildings, a noise barrier is determined to be reasonable cost-wise, thus feasible, and eligible for federal funding.
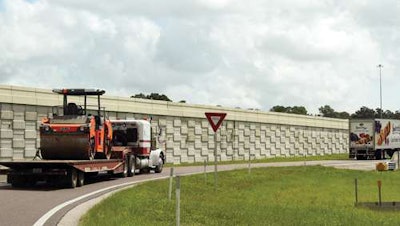
The cost-effectiveness is determined by assigning a value to the square footage required of the barrier, the total of which can’t exceed a certain value per benefited receiver. If there aren’t enough benefited receivers to justify the wall, it doesn’t get funded. In Maine, the cost per benefited receiver can’t exceed $31,000 or the barrier is deemed not feasible.
Type II or “retrofit” projects are noise abatement projects along existing highways. The implementation of a Type II program is not required by federal regulations, but might be eligible for federal-aid funding if the state agency follows guidelines. Otherwise these must be paid entirely by the agency or by private fundraising, for example, from nearby residents.
For more info go to fhwa.dot.gov/environment/noise. New FHWA guidance on noise barriers was provided late last year and can be downloaded at fhwa.dot.gov/environment/noise/noise_barriers/acceptance_criteria/analysis/analysis.pdf.
Evaluating lower-cost barriers
With costs ranging from $2 million to nearly twice that, agencies are looking for lower-cost alternatives to sound barriers, especially for the Type II projects which don’t get federal funding. A new, lower-cost form of noise barrier is the line-of-sight (LOS) barrier, which can make limited sound suppression more widely available in urban and suburban neighborhoods.
The line-of-sight noise wall is just tall enough to break the horizontal line of sight between the highway (noise source) and the home (noise receiver), report Shuo Li, Ph.D., P.E., and Samy Noureldin, Ph.D., P.E., Indiana DOT, and Bowen Guan, Purdue University, and Yingzi (Eliza) Du, Ph.D., Indiana University-Purdue University, in their 2014 Transportation Research Board paper, Residents’ Perceptions and Attitudes toward to Line of Sight Wall and Conventional Concrete Noise Wall for Traffic Noise Abatement.
“Since the eye level height at a standing position is 67 inches for the average U.S. adult, the height of [a] LOS wall may be around 6 feet,” they write. “While the LOS wall does not fit into the current noise wall policy and could not use federal funds for construction, it may achieve a 5 dBA noise level reduction and provide a measure to improve customer satisfaction at a less expensive cost than conventional noise walls. In addition, the LOS wall policy could include the option to require a portion of the cost to be provided from private funds.”
In a predecessor (2013) report by the Joint Transportation Research Program of the Indiana DOT and Purdue University, Evaluation of Alternatives to Sound Barrier Walls, the same authors elaborate on the LOS wall concept.
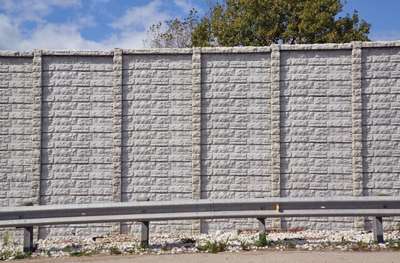
In general, LOS walls are smaller, and therefore cheaper, than conventional noise walls, they say. As LOS walls are smaller, and may have no surface treatment with absorptive materials, they may not provide noise reduction of at least 5 dBA that can commonly be achieved by conventional noise walls.
“There are some unique [issues] with the construction of LOS walls,” they say. “First, LOS walls provide an alternative to meet the expectation of our communities to some degree at a much less expensive cost. More areas may be justified for noise abatement measures.
“Second, LOS walls provide a channel to utilize private funds for those projects that do not meet the classification of a Type I projects or those locations where the cost-effectiveness criteria cannot be met,” they write. “Third, unlike the noise wall policy, the LOS wall policy is not mandated and not necessarily to provide a noise reduction of 5 dBA or more. It becomes more flexible in the design of wall appearance and selection of wall materials, and easier to preserve aesthetic views and scenic vistas to a reasonable extent.”
Following a comparison test of LOS versus conventional precast walls, and surveys of public adjacent to the projects, the writers found that it’s advisable for Indiana DOT to opt to participate in a Type II program, or develop a retrofit noise wall program including a LOS wall policy.
“For LOS walls, the minimum height should be at least 6 ft., but tall enough to block the view of trucks,” they find.
Download your copy of this essential 2013 publication, Evaluation of Alternatives to Sound Barrier Walls, at https://docs.lib.purdue.edu/jtrp/1530/.
Looking closer at materials
Different materials perform differently for the owning agency. “Metal walls are vulnerable to the impacts of rocks and errant vehicles and require protection guardrails,” says Indiana DOT. “Wood walls are prone to weathering, resulting in gaps, and therefore reduced acoustic performance. The fiberglass noise walls may cost as much as the precast concrete wall. The acrylic noise walls may cost two times as much as the precast concrete wall to achieve the same noise reduction. The vegetation noise walls may not be UV-stable and the maintenance – particularly watering to keep the plants alive – is costly.”
In June 2014, an important research paper on sound wall performance – Comparison and Testing of Various Noise Wall Materials – was released. This document, by Deborah S. McAvoy, Ph.D., P.E., and Ryan Theberge, E.I.T., was released by the Ohio DOT and evaluated the efficacy of different sound wall materials in Ohio.
“Noise barriers are a necessary structure along the highway to protect the local residents from excessive road noise,” McAvoy and Theberge say. “There are many different materials from which noise barriers can be constructed. As of 2004, the most widely used noise barrier material was concrete, which accounts for approximately 80 percent of all the noise barriers in the United States. Other noise barrier materials include metal, plastic, wood or soil. Each of the materials used to construct noise barrier has advantages and disadvantages both acoustically and aesthetically.”
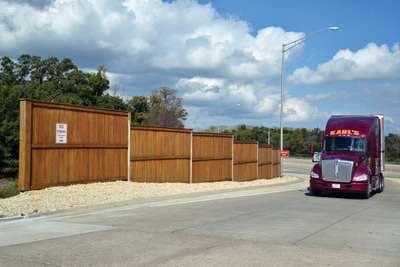
The FHWA’s Traffic Noise Model provides a method for predicting highway noise levels for various noise barrier alignments and heights, and is used in determining whether predicted traffic noise levels warrant abatement, and if warranted, the model is used to design the abatement structures, they write. But in utilizing an “average” pavement type, the TNM doesn’t account for different pavements, some of which are designed to reduce noise. In addition to seeing which barrier types work best in Ohio, the researchers wanted to see to what degree the TNM actually predicted performance.
Seven different materials were field tested across Ohio. These included absorptive concrete walls, reflective concrete walls, hollow fiberglass walls, rubber-filled fiberglass walls, steel walls, clear walls and earthen berms.
“The noise barriers were tested by measuring noise levels in front of the barrier, above the barrier and behind the barrier, while recording traffic data (volume, class, and lane position) and atmospheric conditions,” McAvoy and Theberge say.
The TNM parameters were set to replicate each site that was tested and the noise reduction results from the model were recorded. The results from the model and the field were then compared to determine if the TNM is an accurate representation of the field.
Through this analysis, the research team determined the most effective noise wall material for the reduction of traffic generated noise associated with freeways for a location and situation.
McAvoy and Theberge found the following:
- Clear (Transparent) walls. The life cycle cost analysis found that clear noise abatement walls produce a 0.38 insertion loss (sound attenuation) per dollar of cost. This is among the lowest of the materials tested. Clear noise abatement wall have tremendous advantages in the reduction of visual impacts based upon their ability to prevent hiding scenic views or retail areas.
- Concrete noise abatement walls yielded a mean insertion loss of 18.54 dB. Concrete noise walls tend to take the appearance of many forms, depending on the desired appearance of the state or local municipality; therefore, their versatility in appearance can improve the highway roadside for both the driving public and residents. Concrete has a high structural strength and is resistant to vehicle impact damage. The life cycle cost analysis found that concrete noise abatement walls produce a 0.61 insertion loss per dollar of cost. This is the second highest of the materials tested. Due to the performance, durability and life cycle cost analysis, concrete walls should continue to be used widely across Ohio.
- Earthen berms. The life cycle cost analysis found that earthen berm noise abatement walls produce a 0.72 insertion loss per dollar of cost, highest of the materials tested. Earthen berm installation requires substantial land to develop the height necessary for noise abatement due to side slope restrictions for safe roadway departures of vehicles, and constructability. Earthen berms require landscaping or at least frequent mowing maintenance. Earthen berms should be further evaluated to find an appropriate for construction to reduce the variability in the noise reduction at the receptor.
- Fiberglass is a lightweight material, generally shatter-resistant in the case of vehicle impact and has the ability to take the appearance of many forms. But it may shrink and leave cracks in the wall, thereby limiting the noise reduction potential. Fiberglass can also deteriorate causing concerns to rise with appearance and material strength. The life cycle cost analysis found that fiberglass noise abatement walls produce a 0.45 insertion loss per dollar of cost.
- Wood noise abatement walls produce a 0.38 insertion loss per dollar of cost over their life cycle, among the lowest of the materials tested. Wood walls are constructed with a sustainable material that blends in with a natural or residential background. But with time, the wood will warp and shrink leaving cracks in the wall which limit noise reduction potential.
- Steel noise abatement walls produce a 0.38 insertion loss per dollar of cost, among the lowest of the materials tested. Steel is durable and able to withstand severe temperatures and conditions, such as sunlight, moisture, ice and salt, with a proper coating. But they may be electrically conductive and generate heat with sun exposure which prohibits landscaping from growing near the wall. “Based upon the acceptable levels of noise reduction, life cycle cost analysis, and the durability of the product, the concrete noise walls seem to perform better than the other noise wall materials,” they add. “The TNM, version 2.5, is an acceptable tool to predict noise levels for planning purposes.” ϖ