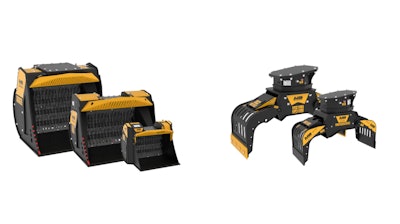
MB Crusher has added two new sorting grapples and three new padding buckets to its range of excavator attachments.
New Sorting Grapples
The new MB-G400 and MB-G500 sorting grapples feature a wider claw opening to precisely place large logs and stones and handle brush and debris.
The MB-G400 sorting grapple weighs 441 pounds and is compatible with 5,500- to 8,900-pound mini excavators. The 926-pound MB-G500 is suitable for excavators weighing 11,200 to 15,700 pounds.
An electrical kit for a two-hose function can be installed, allowing the grapple to rotate 360 degrees. Both models are available with or without a rotating tower. They can be paired with various accessories that simplify material handling tasks: a clam shell kit, a serrated side plate kit, and for the MB-G500, a rubber protection kit and a grip improvement kit.
A load-holding valve prevents the accidental opening of the valve in the event of a sudden drop in hydraulic pressure from the carrier. The silent block keeps noise to a minimum in urban and residential areas.
For added durability, wear parts are made of Hardox steel. The replaceable blades can also be turned upside down to extend wear life.
New Padding Buckets
The new MB-HDS307 and MB-HDS312 and MB-HDS412 padding buckets are ideal for aerating packed soil, reclaiming demolition debris, stones, or roots from clean soil, or screening backfill material to cover pipes or create trench bedding.
The MB-HDS307 weighs 375 pounds and is made for excavators from 5,600 to 11,200 pounds. The MB-HDS312 weighs 1,587 pounds and fits 15,700- to 24,600-pound excavators. The 2,688-pound MB-HDS412 pairs with excavators from 22,400 to 31,400 pounds.
For maintenance on the new models, centralized greasing can be done on site; shafts can be swapped in minutes; and maintenance tools are provided in a tool bag located in a designated bucket compartment.
An automatic hydraulic bumper system reduces hydraulic shock, so the engine, transmission components and operating machine are not damaged. The company says this results in a longer life for the equipment and reduced maintenance expenses.