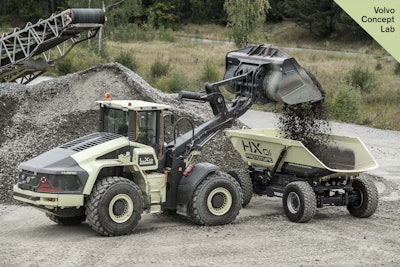
Volvo Construction Equipment drew the curtain back on a number of possible future products during its Xploration Forum this week in Eskilstuna, Sweden. The event, showcasing what could be called pre-prototypes, served to underline where Volvo is headed technologically. “We’re sharing these things because it’s real, it’s not a fantasy,” says Martin Weissburg, Volvo CE president. “We can’t tell you when these products are coming, but we can tell you that we have customers today that want them.”
Volvo CE is laying its technology bets—at least right at this moment—on autonomous vehicles and electrification. “Our challenge,” says Weissburg, “is what we’re calling the triple zero goals: zero unplanned stops, zero emissions and zero accidents.” In addition, the company is aiming at ten times higher efficiency through technology.
The experimental concept vehicles on display — some sporting retrofits on current machines, others in a “green iron” stage — included:
• The LX1 hybrid wheel loader, which Volvo says can deliver up to 50 percent improvement in fuel efficiency over current models.
• The HX1 autonomous, battery electric “load carrier,” specifically designed for Volvo’s Electric Site quarry research project.
• An autonomous wheel loader and articulated hauler.
Equipment World will examine these machines in detail in later articles, but for now here’s an overview of the Xploration Forum announcements:
LX1 hybrid
Customers have long asked Volvo for a hybrid wheel loader, acknowledges Scott Young, program manager for electromobility. These customers include environmental services giant Waste Management, which has a fleet of more than 2,000 Volvo machines. “For years, Volvo’s competitors kept telling me they had a hybrid machine, and I kept asking Volvo when they would come out with theirs,” says John Meese, senior director of heavy equipment at Waste Management.
Now Waste Management is participating in LX1 field studies. In fact, the LX1 on display at the event is now headed directly to California to participate in tests at two Waste Management facilities. There, the LX1 concept machine will go head to head with conventional loaders in fuel efficiency and emissions reduction tests.
The LX1 driveline has no axles; instead electric drive motors are mounted at each wheel. The machine also has electric hydraulics, an energy storage system, a much smaller engine than a comparable conventional machine and a sloped machine architecture that Meese is especially interested in. “The visibility has been increased so much you can see anyone who’s close to the machine,” he says. “That’s a great feature, particularly in some of our tight loading cells.”
Volvo calls the LX1 is “fundamentally a new machine,” with 98 percent new parts, and says it is capable of doing the work of a wheel loader that’s one size larger.
HX1
In researching how to create a quarry site that relies primarily on electric power, Volvo took a hard look at how aggregate is moved in today’s quarries. It was particularly interested in what it says in an inherent vulnerability in relying on large haul trucks to carry these loads: When one of these large haulers goes down, the entire operation suffers.
As an alternative, Volvo is proposing the HX1, an autonomous, battery electric load carrier. As conceived, a fleet of these smaller unmanned carriers will be able to move the same amount of aggregate as one large haul truck, and if one carrier does goes down, it will be a much smaller hit to a quarry’s production.
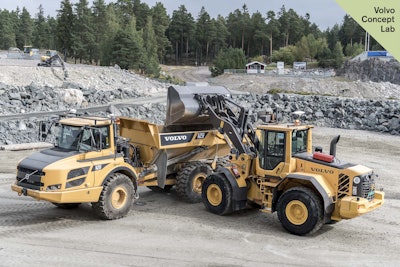
Autonomous machines
Volvo also has targeted autonomous machines, and presented two retrofitted units at the forum: a A25F artic and a L120E loader. Pitting the autonomous loader against a conventional machine in a repetitive one-hour load-and-dump comparison, Volvo says it found that the autonomous machine “could reach the equivalent of 70 percent of that of a skilled operator’s productivity levels when loading and unloading.”
Programmed to work together to carry out a specific set of actions on a predefined route, the automated duo isn’t ready for market yet, although early field tests have been conducted at an asphalt plant in Sweden. “It’s still early days for this technology,” says Jenny Elfsberg, director of emerging technologies, “and we’re working on developing solutions that have the required safety and performance levels that the market will accept.” One research hurdle: getting the machines to communicate with each other and with a central control point. “That’s crucial when it comes to avoiding collisions and facilitating the efficient flow of equipment,” she says.
Where to now?
Despite all the heavy iron evidence present at the event, Weissburg says the biggest shift in Volvo CE’s technology approach is the early involvement of customers in concept machines. “Without a full knowledge of machine applications, we’re innovating in the dark,” he says, adding, “This won’t be accomplished by Volvo alone, but by a full ecosystem of customers, academia and government agencies.”
At the center of Volvo CE’s technological approach is what the company is calling the Volvo Concept Lab. “This will be a place where we can ask questions, an area to play and communicate,” says Dave Ross, vice president, advanced engineering and verification. “It gives agility to a big organization. The green machines you’ll see today are not for sale, but for learning.”