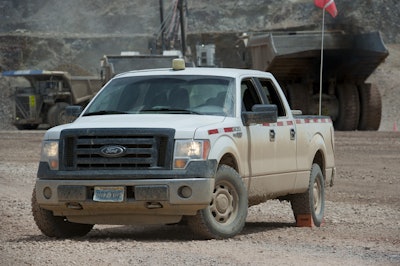
Barrick Gold USA played a key role in the development of Ford’s new F-150.
The company’s mining survey team drove two prototype F-150s with experimental aluminum-alloy cargo boxes at the company’s Bald Mountain and Cortez mines in Nevada from 2013 to 2014.
The beat on them, battered them and tortured them. Or, as Ford refers to it, “tested them.”
The test went so well for Ford, they implemented the new alloy technology in their 2015 F0150s. It went so well for Barrick, that they placed an order for 35 of them as they remove 2012 models from service.
“We are proud Barrick is purchasing all-new F-150s after testing early prototypes in some of the harshest conditions,” says Fritz Ahadi, Ford Commercial and Government Fleet Sales general manager. “This is terrific proof that even our toughest, most demanding customers recognize the benefits of high-strength, military-grade, aluminum alloy to help them get the job done.”
F-150s are used in all of Barrick’s U.S. gold mining operations – from initial exploration and mine support functions to land reclamation. Typical equipment the trucks haul includes compressors, pintle hitches – a special hitch used for heavy towing – and a variety of heavy-duty tools. Barrick is the world’s largest gold producer and operates six mines in the western United States.
“The F-150s see tough duty from operations supervisors, exploration field technicians, project managers, maintenance technicians and closure personnel,” said Rebecca Caudill, Barrick Gold USA fleet manager. “Many of the trucks go into extremely rugged conditions during the planning and mapping out of new projects, core drilling and daily mining operations. Our trucks will see 30,000 to 35,000 miles per year, accumulating well over 100,000 miles in the 40-to-45-month lease rotation.”
Barrick has ordered all-new F-150 SuperCab 4×4 models with the 3.5-liter V6 and 5.0-liter V8.