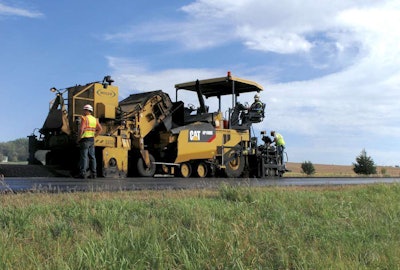
[imagebrowser id=143]
Number one on the “paving by the numbers” handout Caterpillar gives to contractors is “heat the screed.” That start-up process just got faster with the integrated generator and screed heating system on Cat’s new AP1000F asphalt paver.
“With this generator, which runs directly off the engine, you can heat up a standard screed in 15 minutes, all while only using 1,300 rpms,” says Jon Anderson, global sales consultant. This compares to the 30 to 45 minutes this process used to take. “Contractors told us they wanted faster heat-up times since it makes it easier to plan the job,” he says.
This time savings is even a factor when the SE60 XW-Series screed is at its maximum width of 33 feet. “Working at 2,200 rpm, you can still heat the screed up in 25 minutes,” Anderson says. Since 2,200 rpms may be too loud, especially for early morning urban start-ups, Cat has a quiet heat mode that keeps the engine at 1,300 and heats up the full-width screed in 35 minutes.
With the F-Series pavers, which also includes the tracked AP1055F along with the wheeled AP1000F, changing out heating elements has also been simplified. “We used to recommend changing out all the heating elements when doing a screed plate change at around 3,000 hours,” Anderson says. Now, it takes less than an hour to change out an element that’s failed, “ so there’s no need to change all heating elements at once.”
And if a heating element fails, the heating system will adjust so you can keep on paving through the shift. “We still, however, recommend you schedule a repair as soon as possible,” Anderson says.
Cat offers three screed options on the F-Series: the SE60V, SE60V XW and the SE60 VT XW, which offers both vibratory and tamper bars.
New controls
Anderson says the new screed and tractor controls offer both simplicity and flexibility. On the E-Series pavers, the screed extender control had one speed. The F-Series has a proportional extender control that offers two speeds, and can be operated from the screed, tractor or new pendant controls. “This gives you the ability to quickly pull in so you can work around obstacles, and then go back out,” Anderson says. The pendant controls allow the screed operator to stand alongside the machine.
The conveyor ratio control, which used to be adjustable only from the tractor controls, now can be operated from the screed. And now the tractor operator can adjust mix height. Grade control functions, which used to involve a different screen, are now integrated into the paver control screens at each station, and can be operated at the tractor consoles. A single-button autofeeder takes the place of four switches, and an auto-fill button alternates between running the augers and controls.
Propel and feeder system settings transfer between stations with the touch of a single switch. Speed, as well as operation and travel modes, are automatically adjusted at the stations.
Engine, drive
Powered by a Tier 4 Final Cat C7.1 ACERT engine, the paver uses selective catalytic reduction, a diesel particulate filter and diesel emission fluid.
The wheeled AP1000F has a optional 6-wheel drive, which provides 200 percent more front pull force over the E-Series pavers, Cat says. In addition, a front wheel assist or 4-wheel drive option increases front wheel pull force by 50 percent.