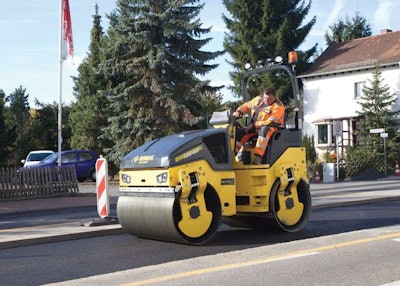
Editor’s Note: If you haven’t already, be sure to check out Part 1 of this series on pavers by clicking here.
If we do some math, we can calculate that the hypothetical Walmart parking lot we began paving in Part 1 of this pieces, should take two days if everything works right, says Chris Connolly, BOMAG sales manager.
In Part 1, the equipment manufacturers we interviewed gave us several suggestions for pavers. Today, we’ll dive into the roller options available.
A Bomag BW278 AD would be chosen to work as the break down roller immediately behind the paver working in a lay down temperature zone in the 250- to 300-degree range. Because vibratory compaction is particle rearrangement and these particles are not going to rearrange without some viscosity in the mix, it’s best to compact the asphalt at optimum temperature. As we lose temperature we also lose viscosity, so staying in a proper temperature range is extremely important to placing a sound asphalt pavement.
At 78 inches wide the BW278 AD allows us two passes on a 12-foot wide asphalt mat. By only making two passes on this panel we are able to stay “tight” behind the paver to work in a more favorable temperature range, Connolly says. With 4,000 vibrations a minute, the normal density and smoothness will require five passes on each 78-inch rolling width.
After 10 total passes, we return to the paver in static mode to start again. This size unit allows for proper overhang for the drum on each side of each pass. We would also require a second roller to help move this job along. The BOMAG BW138 AD-5 would be one choice to get close to the islands and curbing. The unit would work as a finish roller to help remove any lines left by the breakdown unit and smooth out the surface of any imperfections.
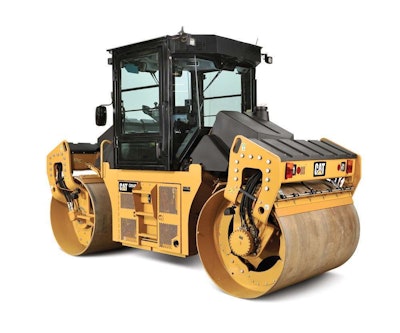
“A job of this size might be more efficiently done with a larger roller,” says Todd Mansell, training consultant, Caterpillar Paving Products. “If you could only pick one, we would recommend a Cat CD54B with split drums. It has a drum steer design that allows it to turn on a tight radius, and the split drums help prevent tearing the mat. It is large enough to keep up on the long straight runs, but the steering and drum design allows it to hug rounded corners and keep the compaction uniform.”
The drum steer design allows the machine to run with the drums offset to provide a compaction width range of 67 to 118 inches, which is handy for efficient finish rolling, says Mansell. Depending on specific production requirements, you could add a CB54B solid drum as a breakdown roller, use the CD54B split-drum as an intermediate roller, and a CC24 (combi roller – steel drum on front, rubber tires on back) for finishing. If two rollers are desired/required, then Cat would recommend the CD54B split drum and a CC24 combi roller.
“For the main breakdown roller on the parking lot, we don’t need a highway-class roller,” says Tim Kowalski, Hamm applications support manager, Wirtgen America. “Instead I would suggest a tandem HD O70V-S with 59-inch drum widths and a split drum in front with oscillation in the rear drum. The use of oscillation will smooth out any surface discrepancies and help in the compaction temperature window restricted by vibration.”
Kowalski says a split drum roller allows one-half of the drum to turn at a different rate from the other half, which is invaluable for compacting tight radii. The ability to move drums at different speeds keeps the mat from tearing. “If you have a lot of islands or other obstructions that you are making turns around, the split drum reduces the cutting of the material,” Kowalski says.
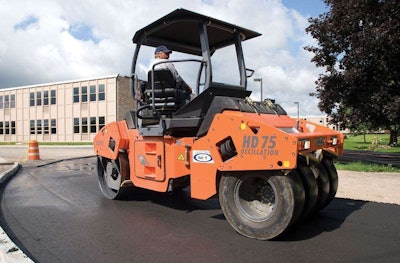
action of pneumatic tires at rear.
He says you might also consider use of a combo roller, in which a steel drum in front is matched by an array of rubber tires in the back. This combination of vibratory steel drum and pneumatic roller permits two kinds of compaction at once, boosting productivity. “The combo roller gives you the initial compaction with vibration up front from the steel drum, but also the ‘kneading’ effect of compaction with the rubber tires in the back,” Kowalski says.
Case says its DV207HF double drum asphalt roller is a good fit to roll and compact this asphalt parking lot. The roller is designed specifically for medium paving applications, says Woody Ferrell, product marketing manager for Case Construction Equipment. The breakdown roller should start to make its compaction passes before the asphalt temperature drops below 220 degrees. “We recommend a pattern of five to seven passes to attain 92 percent to 96 percent of maximum material density,” says Ferrell.
The Case roller achieves the target density with fewer passes thanks to a rolling width of 57 inches and the ability to select between 48Hz to 67Hz to compact the freshly laid asphalt. The standard hydraulically adjustable offset allows the operator to adjust the front frame over 7 inches so that it can operate in applications requiring a tight radius.
The Case DV207HF has a 34-degree steering angle along with (+/-) 8 degrees of oscillation, which keeps both front and rear drums in constant contact with the compacting surfaces. The roller has a 15-foot turning radius for tight asphalt compaction parking lot requirements, Ferrell says. The compactor will to compact 20 percent theoretical gradability with vibration on or 30 percent theoretical gradability with vibration off.
Cooling asphalt is a concern, because it must be compacted before it hardens, says Volvo’s Mooney. Because the parking lot construction is less controlled than a highway project, he says compaction is less of a concern as there is generally no testing. So the contractor is not as picky about the size of the compactor, other than to have rollers that are large enough to roll out marks.
Mooney recommends nothing smaller than a Volvo DD24 (2.5 tons and 4 foot width). Then, perhaps the job is large enough to bring in one a larger DD70 or DD110 compactor to get the large areas covered and use the smaller compactor for the tight areas.
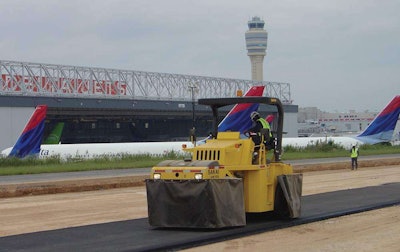
Sakai recommends using three asphalt rollers for the parking lot application, says Yuki Tsukimoto with Sakai. First consider the SW652ND roller, a 58-inch double drum machine that weighs 16,800 pounds for medium size projects. By flipping a switch, the operator can choose between N, or Oscillation Mode, and D, or Standard Vibration Mode.
The Oscillation mode provides an oscillatory motion of the drums, which is good for finishing the surface of the asphalt because it has a dynamic kneading effect, Tsukimoto says. The Standard Vibration Mode has high compaction capability, which will achieve the required density of the 3-inch thick pavement and the base as well. The typical application of the roller is to start with the D mode for the first three to five passes, then finish with two to three passes in the N mode.
Or, the contractor can use a GW750 roller in the breakdown, intermediate and finish rolling positions, Tsukimoto says. It’s a 77-inch-wide vibratory pneumatic tire (VPT) roller weighing 20,370 pounds and is well suited for medium to larger projects. The vibratory or dynamic kneading effect of the pneumatic tires compacts both asphalt and aggregates uniformly. A tight longitudinal joint can be achieved by the dynamic kneading effect. When steel drum vibratory rollers are used on the longitudinal joint, they often fracture aggregates that may cause joint deterioration in the future.
And the TW320 Combi roller, which has a vibratory front drum and four rear tires that are super-flat for a smooth finish, is a consideration for working around islands because of its small size, with a 47-inch-wide roller weighing 6,329 pounds, Tsukimoto says.