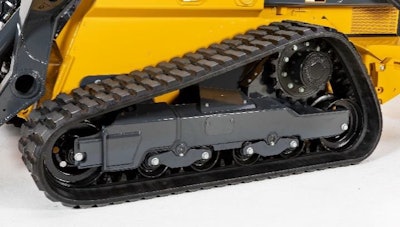
The smoother the ride, the smoother the finished grade. Less vibration also translates into less operator fatigue, better productivity, faster speeds and reduced spillage from the bucket.
That’s why John Deere has introduced an anti-vibration undercarriage system as an option on its 333G compact track loader. The first line of defense is the addition of rubber isolation mounts that absorb much of the high-frequency vibration and twisting of the machine superstructure. These also increase track life and allow for easier repairs.
Bogie rollers in the undercarriage oscillate over uneven terrain and prevent the machine from rocking back and forth.John Deere
A new angled steel shield was added to protect the hydrostatic hoses from exposure to debris. Four additional grease points are located in easy to access areas for simplified maintenance and less downtime from potential damage to the hydrostatic hoses.
The anti-vibration undercarriage system is now available on zig-zag bar tracks on the John Deere 333G compact track loader models and can be purchased in the United States and Canada and some international locations.