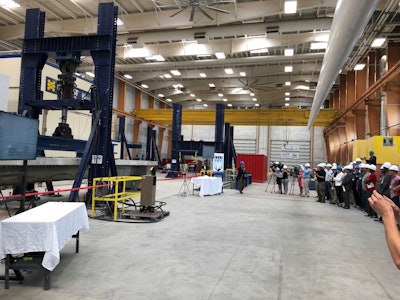
The University of Maine (UMaine) reports that engineers at its Advanced Structures and Composites Center have developed a new composite girder bridge system that can be deployed quickly. The engineers, Maine Department of Transportation officials, business leaders, investors, researchers, staff, and members from Advanced Infrastructure Technologies (AIT), UMaine’s licensee for the original “Bridge-in-a-Backpack,” conducted a strength test in the laboratory using computer-controlled hydraulic equipment to simulate the effect of heavy highway truck loads in order to prove the design modeling predictions and demonstrate the bridge system.
“As the commercialization partner of the Center’s composite arch bridge system, today’s event allowed us to showcase this new technology with potential investors, as well as DOT partners and executives,” said Brit Svoboda, chairman and CEO of AIT Bridges, according to the news article. “We’re ready to go to market.”
The patent-pending bridge system, which uses composite material girders and precast concrete deck panels, reduces the time and logistics required to build a bridge, making it possible to build a bridge in 72 hours. The new bridge girders are also designed to last 100 years, and the precast concrete deck is designed for easy removal and replacement. The bridge is designed for unsupported spans of up to 80 feet.
“Today’s bridge test exceeded our expectations,” said Dr. Habib Dagher, executive director of the UMaine Advanced Structures and Composites Center, in a a university press release. “The composite bridge withstood forces equivalent to more than 80 cars stacked on top of each other, and more than 5 times the HL 93 design load specified by AASHTO. The composite bridge girder exceeded twice the collapse strength of steel and concrete girders. Today was truly a remarkable engineering achievement made possible by research sponsored by the U.S. Army Corps of Engineers and the dedication and hard work of University researchers.
“This bridge system takes advantage of the unique properties of both composite materials and precast concrete, and it is designed with construction logistics in mind,” Dagher continued. “The bridge girders weigh only 1-2 tons for 40- to 80-foot spans, so that they can be erected with locally sourced common rental cranes, making them easy to deploy in most locations.
“The unique girder shape was designed to be nesting and stackable,” Dagher added. “As a result, three to four bridges can be transported on a single flatbed. This bridge system continues the University of Maine’s commitment to be a world leader in developing advanced, innovative solutions to address our nation’s infrastructure challenges. We thank the U.S. Army Corps of Engineers for sponsoring the research work.”
“We are delighted to see the University of Maine preparing to test yet another important innovation on July 12,” said U.S. Senators Susan Collins and Angus King in a joint statement, according to UMaine. “Maine, New England, and our nation need innovative technologies that will accelerate bridge construction, reduce traffic disruptions, increase the lifespan of infrastructure, and decrease costs to the taxpayer. The private sector partners and DOT officials attending the test will help to ensure that such critical technologies are quickly brought to market. As longtime supporters of UMaine R&D, we applaud the University for its continued leadership in transportation and infrastructure innovation.”