Bridge Work
Top FHWA bridge engineer looks at today’s and tomorrow’s bridges.
By John Latta
America’s bridges are safe.
T hat’s the core message in an overview of those bridges from Tom Everett, P.E., the Federal Highway Administration’s principal bridge engineer and bridge programs team leader.
“There are thousands of qualified bridge inspectors out there working to make sure bridges are safe for public travel and evaluating those bridges,” says Everett. “If a bridge is deemed unsafe, they take prompt action – they close it, divert traffic or whatever. We do not have a national bridge safety crisis on our hands. [People] don’t need to be afraid to drive across a bridge to work or as the kids go to school. We have a lot of people working every day to ensure that.”
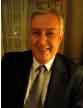
And this won’t change, he says. “I think you’ll see FHWA step up our oversight of the bridge inspection process.”
What’s more, he says, in terms of bridge conditions, the state of America’s bridges has shown a positive (downward) trend in reducing the total number of deficient bridges.
Of the challenges facing bridge owners, Everett, not surprisingly, says, the single biggest one is probably establishing a sustained funding source to adequately address the bridge needs. While we wait, he says, “we must maximize the use of the funding available to maintain our good bridges in good condition and, at the same time, reduce the population of deficient bridges with rehabilitation and replacement.”
Other significant challenges, he says, include: the increased deck areas of America’s bridges, which means more to maintain, preserve and inspect, increasing construction costs, and increasing traffic volume (by both volume and weight); dwindling resources for owners; and the need to “invest adequately in preserving existing bridges, and doing so systematically. This is one of the best ways to reduce the rate of deterioration.”
Changes have come in recent years in the way FHWA deals with bridges, and they will continue to come, says Everett.
“We must continue to learn from the deterioration mechanisms of our existing bridge population and design our future bridges to eliminate these deterioration mechanisms. The Long-Term Bridge Performance Program (see sidebar) will help us in this regard. Accelerated bridge construction and prefabricated bridge elements and systems (PBES) will have major impacts on how we build, inspect and maintain our bridges. High-performance materials will enhance the performance of prefabricated bridge elements.”
By placing greater emphasis on systematic preventive maintenance and system preservation, states can maintain existing bridges in good condition and minimize deterioration of bridge elements while addressing the deficient bridges, he says.
Funding uncertainty has created a need for greater emphasis on lifecycle cost analysis when bridges are rehabilitated or replaced to find the most cost-effective strategy, according to Everett, and business practices may need to change to evaluate the impact on the user and consider this in the project development process.
“In the area of bridge inspection and monitoring, there will likely be a move toward the collection of improved data, in terms of both quality and usefulness (level-of-detail: element level condition information rather than component level),” he says. “Remote-sensing and monitoring systems are being developed and in some cases used to identify problems at an earlier stage and to help keep bridges safe.
“We may see a move toward the establishment of bridge inspection frequencies (intervals) that are based on rational criteria, rather than an arbitrary period of time as is currently done.”
New technologies are changing the game, says Everett.
For example, on the inspection/condition evaluation side, engineers are continuing to find technology that lets engineers look inside of bridges to accurately tell what’s happening to the steel inside concrete bridges. “High-performance materials have made great strides. Take high-performance concrete – we’re getting outrageous compressive strengths and finding uses for that concrete. High-performance steel is in place and in many states, and among other things it’s very resistant to cracking. Fiber-reinforced polymers – we’ve only scratched the surface there. Concrete that doesn’t require vibration in placement has grown in use in the past five years and we’re learning more about how to use it. Lightweight concrete has been around a long time, but provides many possibilities for bridges; maybe lightening bridge decks will help us get more use from it.”
In the three sidebars in this story, Everett expands on these themes.
Integrated Bridge Project Delivery and Lifecycle Management Program
This project is primarily aimed at the control and sharing of bridge data using computer technology.
The technology reviews of bridges abroad sponsored by the FHWA and AASHTO highlighted the benefits of using integrated automation to achieve rapid coordinated design and construction, as well as subsequent cost-effective lifecycle maintenance, repair and rehabilitation. The current FHWA project is to demonstrate the “proof-of-concept” to U.S. bridge owners. The main focus of the work is the development of integrated engineering software that demonstrates applications and the benefits of the program, and shares that information with bridge owners.
The current U.S. practice of information transfer during the bridge design, fabrication, construction and operation processes is fragmented. These processes involve repeated manual transcription of data that is error-prone, approvals (e.g., of shop drawings) that are time-consuming, and formats that beg for standardization to facilitate electronic information transfer. A complete modeling of bridge information in a standardized format will facilitate integration of computer-aided design (CAD), computer-aided engineering (CAE) and computer-integrated manufacturing (CIM), resulting in rapid and better-quality project delivery and cost-effective lifecycle management.
Three demonstrations have been conducted so far. It is envisioned that successful development and demonstration of Integrated Bridge Project Delivery and Lifecycle Management may lead to a pilot project in the second phase of this effort. The second phase is not included in the ongoing work.
The Long-Term Bridge Performance Program
In April of 2008, the FHWA initiated the Long-Term Bridge Performance (LTBP) program.
The objective of this anticipated 20-year-or-longer research program is to develop a better understanding of how typical highway bridges perform under a variety of service conditions through detailed inspection, monitoring and testing of large population of bridges, representing the most common bridges in the inventory.
To make certain that the LTBP program would be a successful national program, the FHWA reached out to our partners at state agencies, other government agencies, researchers from home and abroad, and experts from the industry to establish a framework with short- and long-term visions, even before the program got underway in 2008.
Since the actual work began almost two years ago, the FHWA received tremendous support from a number of state highway agencies by sharing valuable information on the status of our nation’s bridges and in providing access to bridges in their respective state for monitoring, testing and evaluation.
The pilot study phase of the LTBP program that began more than a year ago is expected to be completed in September of 2011. This study was initiated to validate and refine the methods, protocols and guidelines for data collection and monitoring, and to ensure that the objectives of the LTBP program are well-defined before the larger number of bridges are monitored. The pilot study includes a total of seven bridges, one each in seven selected states, providing a broad representation of the many environmental conditions experienced throughout the United States. The pilot bridges are located in California, Florida, Minnesota, New Jersey, New York, Utah and Virginia. A variety of tools and cutting-edge Non-Destructive Evaluation (NDE) technologies are being employed at each pilot bridge to establish baseline characteristics and to monitor long-term bridge deterioration and performance under traffic loads and environmental effects.
The long-term data collection phase is expected to begin in spring of 2011. This phase will include detailed inspection, monitoring and testing of up to 500 bridges over the next 20 years, based on available resources.
The LTBP program is establishing a TRB advisory committee to provide advice and assistance on the conduct of the LTBP studies. The first meeting of this committee is expected to take place this spring. A State Coordinators Committee is also being established to coordinate the implementation and execution of LTBP activities in their respective states.
The LTBP program will continue partnering with stakeholders through additional focus group meetings, industry outreach and professional meetings in order to obtain the information and data that is needed to improve the long-term performance of the nation’s highway bridges.
Says Everett: “We strongly believe that the outcome of the LTBP program will strengthen our ability to deliver, manage and maintain an efficient highway infrastructure,” and will help:
advance deterioration and predictive models;
improve knowledge of state maintenance effectiveness;
demonstrate the effectiveness of sensor technology in bridge inspection/condition assessment;
implement performance-based design; and
foster the next generation of bridge and bridge management tools.
What has changed most in the past five or 10 years in the way FHWA works with bridges?
“We have an improved awareness of the factors that affect a bridge’s performance, from design to construction to preventive maintenance to inspection, and ultimately rehabilitation/replacement,” says Everett. Some examples:
1. Preservation: One of the biggest changes took effect under SAFETEA-LU, when Congress recognized the importance of preserving the existing inventory of bridges and allowed the use of federal bridge program funding for systematic preventive maintenance/system preservation.
2. Improved design codes: In collaboration with AASHTO, FHWA has invested significant resources into developing the Load and Resistance Factor Design (LRFD) specifications and providing training to the states in using LRFD. The states are now using LRFD for all federal-aid bridges.
LRFD is based on technological advances in bridge engineering, sound scientific principles and a systematic approach to ensure safety, durability, economy and aesthetics. The LRFD philosophy is consistent with other major bridge design codes used in other progressive countries around the world.
LRFD-designed bridges are expected to have a long service life with minimal maintenance.
3. Improved load rating codes: The AASHTO Load and Resistance Factor Rating (LRFR) serves as a compendium to LRFD in setting the standards for condition evaluation and rating of bridges. LRFR provides procedures and policies for determining physical condition, maintenance needs and load capacity for highway bridges. LRFR assists bridge owners in establishing inspection procedures and evaluation practices that meet the National Bridge Inspection Standards. FHWA supports AASHTO in adopting and publishing the Manual for Bridge Evaluation (MBE), which provides guidelines for using LRFR.
4. High-Performance Materials for Improving Performance of Bridges: FHWA in collaboration with AASHTO, industry and academia has developed and deployed high-performance materials:
High-Performance Concrete (HPC): HPC is one of several products investigated and advanced under the Strategic Highway Research Program. HPC has enhanced durability and strength not normally attainable in conventional concrete. HPC is denser, stronger and less permeable. (Strategic Highway Research Program 1 studies indicated that chlorides would diffuse through 2 inches of concrete cover in 12 to 20 years. For HPC elements using appropriate quantities of pozzalanic admixtures or slag, the chloride diffusion rate would be 50 to 70 years.) HPC enables longer bridge spans, increased durability (100-year life), improved engineering properties, better long-term performance and reduced life-cycle costs.
High-Performance Steel (HPS): Structural steels have high strengths, enabling engineers to design and build long-span bridges. However, extra care must be taken in welding, corrosion protection and crack prevention. To overcome these concerns in structural steels, a cooperative research program between the FHWA, the U.S. Navy and the American Iron and Steel Institute (AISI) developed HPS for bridges and structures. HPS has improved weldability, and resulted in excellent corrosion resistance, high crack tolerance and very high strengths. The combination of these improved properties of HPS leads to cost-effective applications in bridge design and construction. Many states are taking advantage of these properties in new bridge designs to improve long-term performance, lower first cost and reduced life-cycle cost through lower maintenance and repair costs.
Fiber-Reinforced Polymers/Composites (FRP): FRP has unique properties, such as high strength, light weight, corrosion-resistance, high toughness, etc., which make it very good for strengthening, repair and seismic retrofit of bridges and structures. FRP has great potential for providing engineering solutions for rebuilding our aging infrastructure. It has attracted the interest and attention of the research community, government and private industry to find ways to successfully integrate FRP in structural applications. In recent years, FRP has been used as rebars and prestressing tendons in concrete structures, sheets and laminates for strengthening concrete and steel members, wraps and shells for seismic retrofit of concrete columns, and structural shapes for bridges and decks.
Ultra-High-Performance Concrete (UHPC): A fiber-reinforced cementitious composite, UHPC is the next level of high-performance concrete. UHPC has very high compressive strengths in the range of 20 ksi to 30 ksi, and tensile strengths as high as 1.5 ksi. It has high durability – very low permeability and is highly resistant to abrasion, freeze-thaw and scaling. The cost of UHPC is steep at the present time. It is now used cost-effectively in a few applications, including closure pours between precast panels, precast deck panels and some girders.
5. Self-Consolidating Concrete (SCC): SCC is a concrete that does not require vibration during placement. SCC flows into and completely fills intricate and complex forms under its own weight, passes through and bonds to congested reinforcement under its own weight, and is highly resistant to segregation. SCC offers many advantages for the precast concrete industry and cast-in-place construction. For example, low noise levels in the plants and construction sites, eliminated problems associated with vibration, less labor involved, faster construction, and improved quality and durability. States are using SCC in precast, prestressed bridge elements, and cast-in-place projects.
6. Lightweight Concrete (LWC): Benefits over normal-weight concrete include reduced dead load of structure, enhanced durability (better curing), and reduced handling, transportation and erection costs (although actual material costs are higher).
7. Seismic Retrofit of Bridges: Older bridges are susceptible to damage or collapse due to earthquakes. FHWA has developed Seismic Retrofit Manuals to help states with state-of-the-practice in seismic retrofit of bridges. Seismic retrofit is a cost-effective way to protect our investments in bridges and structures. States with high seismicity are assessing the vulnerabilities of their bridge inventory and develop a program for seismic retrofit.
8. Accelerated Bridge Construction (ABC): ABC is taking advantage of prefabricated bridge elements and systems (PBES) to help highway agencies dramatically reduce construction time and traffic disruptions, resulting in improved safety in the work zone. PBES approaches offer high quality because they are manufactured offsite under controlled conditions. With the use of self-propelled modular transporters (SPMT), an entire bridge can be fabricated off the bridge site and then transported to the bridge site for overnight installation. SPMTs can be used to remove and replace bridges efficiently and effectively.
9. Improved bridge safety programs and practices:
We updated the National Bridge Inspection Standards regulations in 2005;
We are currently enhancing our oversight of compliance with the regulations (data-driven, risk-based process);
We have additional staff dedicated to bridge safety;
Following the I-35W collapse, we issued gusset plate inspection and load rating guidance to bridge owners.