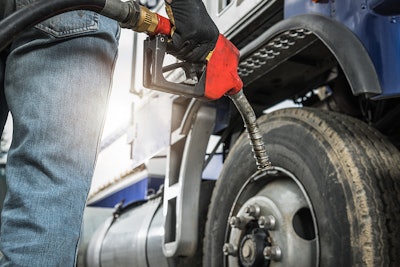
This is Part 4 of a four-part series on managing fuel costs as part of the Fuel Cost Volatility Survival Guide. (Read Part 1, Part 2, Part 3, and Part 4 or download the entire guide.)
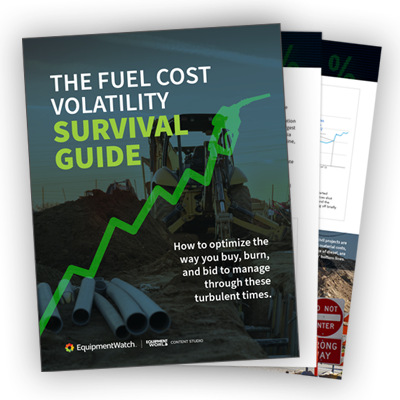
Download the Fuel Cost Volatility Survival Guide
→ Ninety-eight percent of construction equipment runs on diesel.
→ The price of diesel has increased 74 percent over the past 12 months and shows no signs of dropping.
→ Fuel accounts for more than 40 percent of machine operating costs – more than repair, parts, and labor.
Yet for most contractors, managing fuel is an afterthought. But with prices for construction materials and services increasing nearly 21 percent over last year, taking a hard look at costs – including fuel – is a matter of survival.
The good news is there are steps contractors can take to manage fuel costs. This guide outlines the current situation, looks at what’s driving fuel volatility (it might not be what you think), offers real-world ideas to help you manage today’s challenges, and gives you tools to maximize efficiency and profitability for years to come.
Of all the costs construction companies incur, fuel is probably the largest and worst managed, says construction company advisor Mike Vorster. “Looking at the total cost of owning and operating a fleet of construction equipment, I have seen many companies where fuel is one-third of the total equipment cost,” he estimates. “Those companies have a chief financial officer who manages the buy/sell/lease decisions and an equipment manager who tracks repair and maintenance costs. But who is looking after fuel?”
“Take a person that costs $30 per hour – you know exactly what they are doing,” he says. “But when I ask for the fuel consumption of a machine with a fuel cost of $30 an hour, people have no idea. It is a very big, very badly managed, and very volatile cost component.” If labor costs had gone up as much as fuel, “we would be hysterical,” he says. “But fuel goes up and we say it’s unavoidable and do little to sharpen our pencils and see where we can achieve some savings.”
Vorster’s solution to getting a handle on fuel costs? Appoint a fluids czar, someone who manages all machine fluids – fuel, but also oil, diesel exhaust fluid, coolant, and air – the same way the personnel department watches payroll or the shop superintendent looks after repairs.
“If labor costs had gone up as much as fuel, ‘we would be hysterical. But fuel goes up and we say it’s unavoidable and do little to sharpen our pencils.”
- Mike Vorster, Construction Consultant
The ideal fluids czar would be less mechanic than chemist, Vorster says, with a passion for cleanliness and watching the bottom line. The job entails buying, storage, distribution, and recordkeeping for all fluids, but given the rising price of diesel, fuel is where companies would really see the benefits of having such a role, Vorster says.
With diesel significantly higher than just a few months ago, contractors must realize they are dealing with a very expensive commodity that they can no longer leave unmanaged, he says. “They need to cut waste to the absolute minimum.”
Cleanliness and dryness are critical. “Most engine failures start in the tank,” he says. “Dirty fuel and wet fuel are the biggest causes of engine failure.” There are lots of opportunities for fuel to become contaminated. Many contractors have stationary fuel tanks on the job site but have no way of knowing how clean the fuel or the tank is. “When you’re transferring fuel from a bulk tank to a fuel truck and then to a machine, dirt gets in,” Vorster says.
The bottom line is contractors must understand that fuel has become a very high-risk component of their fleet costs, Vorster says. Because fuel used to be cheap, “everyone’s always taken it as a given. But it’s reached a tipping point where we can no longer just shrug it off as a necessary evil but where we must now do something about it.”