As prices for asphalt cement (AC) and polymer have shot up dramatically, agencies and contractors are looking for ways to hold the line on the cost of asphalt pavements.
By Daniel C. Brown
The number of transportation agencies that use recycled tire rubber in asphalt has increased steadily in recent years. Several states have specifications for adding recycled tire rubber to asphalt binder, including Florida, Georgia, Louisiana, Texas, Arizona and California.
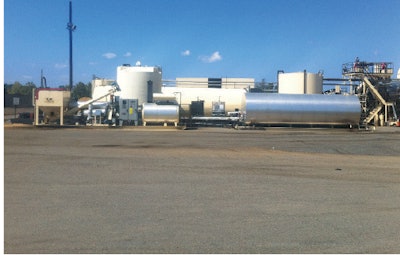
As prices for asphalt cement (AC) and polymer have shot up dramatically, agencies and contractors are looking for ways to hold the line on the cost of asphalt pavements. Currently, almost 20 percent of the asphalt binder sold in the United States for paving is polymer modified. This makes rubber an economically attractive extender of asphalt, since it contains both polymer and oil. Also, the price of recycled tire rubber is stable, unlike the price of AC and polymer.
Recycled tire rubber can be added to asphalt in three ways, says Doug Carlson, vice president of asphalt products for Liberty Tire Recycling, a Pittsburgh-based rubber provider. The classic method, specified by ASTM D6114, is called asphalt rubber, or the Arizona method. It is a wet process. Recycled tire rubber is added at close to 20 percent by weight of the liquid AC. The rubber particles are fairly large – up to 2 millimeters in size. The process requires special blenders that can be used in the field to react the rubber with AC.
Asphalt rubber has found its place in heavy-duty chip seals and in surface mixes that are gap graded to have space for the rubber particles. Open-graded friction courses (OGFC) and stone-matrix asphalt (SMA) can make good use of asphalt rubber. The material is comparable to an asphalt modified with 7 percent polymer, says Carlson.
More than ever, terminal or refinery facilities are either considering supplying rubber-modified binders or do supply them, says Jeff Smith, technical director for Cactus Asphalt, an asphalt rubber binder supplier. “That’s a change in our industry, because in the past they have been totally resistant to that,” Smith says. The reason is the lower cost of recycled tire rubber. “Even if it takes three times the tire rubber percentage to do what one percent of virgin polymer will do, still, the overall cost to the manufacturer is much less to use tire rubber.”
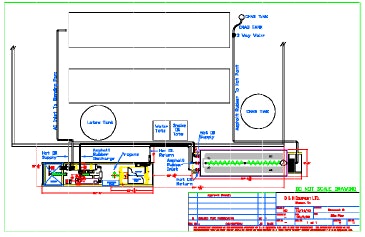
The third method is a newer dry process, approved by specification in Georgia. “It’s a very fine-grind rubber, less than 600 microns in size. And the dosage is only around 10 percent by weight of the binder,” says Carlson. “The new dry process also will get a lot of attention here in 2014 because there are quite a few states that have specifications based on mix performance. Contractors and states prove the mixes based on a Hamburg rut tester or the Overlay tester. Rubber happens to do very well under those tests.”
PG tests
Smith also points out that the movement to Performance Grade (PG)nparticulate rubber binder materials, such as asphalt rubber and polymer-modified asphalt rubber, is notable. This is being worked on nationally, with many people involved. “It’s a change to traditional specification requirements concerning the dynamic shear rheometer and how that is utilized,” he says.
John D’Angelo, formerly a high-ranking official with the Federal Highway Administration (FHWA) and now the chief operating officer of D’Angelo Consulting LLC, has written a white paper that describes testing procedures needed to evaluate the performance characteristics of rubberized binders. “Without a well-defined binder specification, adoption of the use of crumb rubber modified (CRM) binders will be almost impossible to achieve,” D’Angelo writes.
“Now with AASHTO [Association of American State Highway and Transportation Officials], we’re trying to develop a regular PG spec for rubber so that more states will feel comfortable in switching over and using it,” says D’Angelo. “There are still a few issues to work out with it, but it is just about finished and ready to be approved by AASHTO. There are a lot of states that are interested and are looking at the spec.”
New testing equipment geometries are required to test CRM binders with rubber particles on the order of 1 mm in size, D’Angelo points out in his paper. “One approach that has been used in the food industries has been testing with concentric cylinder geometries,” he writes. “Dynamic Shear Rheometers currently used for asphalt testing can be adapted to use a Searle (cup and bob) system. This type of system can perform all the same type of testing that is currently used for asphalt binder grading. The advantage is that the cup-and-bob geometry can easily handle larger gaps up to 4 to 7 mm, and therefore larger crumb rubber particles.” (The cup and bob uses a center cylinder, or bob, that rotates inside the cup, which holds the binder and is stationary.)
“Initial comparisons of new testing geometry to the existing …geometry has shown that equivalent results can be obtained,” writes D’Angelo in his paper. “The testing was done on both neat and CRM binders. Preliminary testing with the new testing geometry has shown that it will provide the same results as the standard parallel plate geometry in the dynamic shear rheometer. Both coarse and fine-ground CRM binders were evaluated and provide improvements in the properties of the binder,” D’Angelo writes.
In the field: Producing, paving and bumping up the grade
Wayne Marshall, corporate quality control manager for Reeves Construction Co., Greenville, S.C., and his company operates 22 asphalt plants in Georgia. Reeves and other contractors in Georgia have successfully produced and paved more than 500,000 tons of rubberized asphalt since 2007, Marshall says, adding that there have not been any unusual performance issues with those pavements.
Reeves owns and operates several machines that can blow dry, finely ground rubber – minus 40 mesh – into a mixing drum or into a mixing pugmill located at the discharge end of the dryer drum. “Now we have the DOT behind us with specifications for it, so they wanted more control over the process,” Marshall says. “Our machines have a weigh depletion system that can measure the dry rubber.”
Marshall uses CRM binder to bump up the grade of base virgin asphalt to a typical PG 76-22. That binder is used on high-traffic state routes and interstates. Base liquid, which for Reeves is typically a PG 67-22, is taken and then enough rubber is added to bring it up to meet the requirements of a PG 76-22, Marshall says. With the latest binder, 8 percent rubber is being added to the total binder to meet DOT specs, he says. The material normally comes in 2,000-pound Super Sacks.
“If the state lets a project that requires polymerized asphalt, you can either use the PG 76-22 SBS or in lieu of that, you can use crumb rubber,” Marshall says. “The spec reads that it has to meet the same specs as the SBS [styrene butadiene styrene] polymer.”
Marshall says he and Reeves officers like crumb rubber because its price is stable, unlike that of polymer. Major projects often take a couple of years from the bid date to start of construction. So the volatile price of polymer makes it difficult to bid an asphalt paving project. If a contractor bids for a polymer project at the current price, it could easily jump by construction time. If the contractor bids an escalated price, the risk is that someone else would underbid that price.
Reeves Construction Co. has just finished a project on I-75 that has 2 inches of SMA with crumb rubber and a friction course in downtown Macon, Ga., coming north through Macon toward Atlanta. “I think we used something like 40,000 tons of rubberized asphalt out there,” Marshall says. “We use it on a lot of state routes. We have a job down in Tifton that has nearly 90,000 tons on U.S. 319 that will be laid this year. And we have a 50,000-ton job down in Albany that will be starting as soon as the weather breaks.”
On Interstate 10
In California, Granite Construction Co. recently performed a “mill-and-fill” project by milling 1/10 of a foot from a 7.5-mile stretch of Interstate 10 near Palm Desert. Granite used a gap graded Superpave mix that blended crumb rubber into PG 64-16 virgin asphalt.
The California Department of Transportation (Caltrans) requires an extender and some high natural rubber to be used in combination with the crumb rubber. The total CRM modifier was 18 percent of the binder by weight, says Jim Marsolino, project quality control manager for Granite. Virgin binder was 82 percent.
“We blended it with our portable rubber plant,” Marsolino says. “We bought the crumb rubber, the extender and the natural rubber from suppliers, and dumped Super Sacks into our hopper. That mixture goes into a reaction vessel where everything gets mixed together to make the binder. It reacts for a certain length of time based on what the spec is for the rubber. Once it reaches the specified viscosity, it goes to our holding tank, and is then used for the manufacture of rubberized hot mix asphalt.” The reaction temperature was 393 degrees.
The mixture worked well, Marsolino notes. Caltrans requires a method specification for thin lifts of asphalt instead of a density spec. Granite had to complete a certain number of roller passes at each level – breakdown, intermediate and finish stages – before the temperature of the asphalt dropped below certain levels. Steel-wheeled rollers handled compaction for each of the three stages.
“We ran the plant at 180 to 200 tons per hour, paving at night,” Marsolino says. “We paved one lane at a time, and whatever we milled out in one night had to be paved that same night.” He said the contractor was able to pave some 1,400 tons per night in an eight-hour shift.
Adds D’Angelo: “History has demonstrated that CRM binders will perform well in rutting and cracking. Using the new testing techniques, CRM binders can be compared directly to the polymer modified binders. This clearly demonstrates that CRM can be used in place of, or in combination with polymer to provide a high-quality performance graded (PG) binder.”
Reeves Wins ARTBA Award
Reeves Construction Co. recently won the 2013 Globe Award from American Road & Transportation Builders Association (ARTBA) for a project on Highway 247 in Bibb and Houston counties in Georgia. Reeves says its West Division, in collaboration with the Georgia Department of Transportation (GDOT) and Rubber Asphalt Solutions (RAS) set the green standard for asphalt paving with this project.
The project consisted of 5.18 miles of milling and repaving the existing roadway. All of the performance graded PG 76-22 binder used in these mixes was modified with ground tire rubber of up to 10 percent of the total asphaltic cement content. A total of 27,250 tons of crumb rubber modified asphalt pavement was placed across four lanes from Echeconnee Creek to Liberty Church Road through Bibb and Houston Counties, Georgia. This included a total of nearly 311,000 lbs. of processed tire rubber. All of the 12.5-mm SP dense-graded mix was produced with 24-percent recycled asphalt pavement (RAP).
Daniel C. Brown is the owner of TechniComm, a firm that specializes in communications for the construction industry.