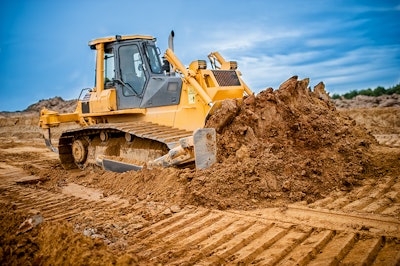
This is Part 3 of a four-part series on managing fuel costs as part of the Fuel Cost Volatility Survival Guide. (Read Part 1, Part 2, Part 3, and Part 4 or download the entire guide.)
“There was a time where the price of diesel fuel might not change 40-50 cents over many years,” says Brett Ames, district president with SEMA Construction, a nationwide, full-service contractor that operates 1,000 pieces of equipment. Back then, contractors paid more attention to fuel consumption factors than to the price per gallon of fuel. But skyrocketing fuel prices are now complicating the situation, Ames says. And because fuel plays a major role across all aspects of a construction project, fuel price increases have a much bigger impact on contractors than on businesses in many other industries, notes Ken Simonson, chief economist with the Associated General Contractors of America.
Diesel prices have increased 74 percent over the last year, with fuel now making up more than 40 percent of equipment operating costs. And fuel prices are only part of the story. Ames says SEMA’s overall equipment costs have gone up 33 percent. “We’re attributing it to a combination of factors including inflation,” he says.
The good news is, that if you’re smart about how you manage your equipment, experts say you can make money in this volatile market. That starts with taking a hard look at costs, Ames says. “We use EquipmentWatch consumption factors as a basis,” he says. When SEMA’s costs exceed those benchmarks, “we look at things differently.”
Contractors face a big jump in operating costs — driven primarily by fuel prices:The EquipmentWatch Internal Charge Rate Calculator helps contractors understand in advance what fuel price increases will do to their profit margin.
EquipmentWatch, owned by Equipment World's parent company, Randall Reilly, offers a calculator that helps contractors accurately calculate their internal charge rate: the amount they charge themselves to own and operate an asset with cost estimates and trends based on data collected from hundreds of thousands of models monthly. Contractors can measure the impact each variable cost factor – fuel, hours, field repair, tires, etc. – has on ownership and operating costs by adjusting the costs and the rate in real-time. In the current environment, the calculator can help contractors understand in advance exactly what fuel price increases will do to their project profit margin, including the cost of idling. “If you’re not keeping up with your rates, you could overcharge and lose a bid and if you’re not keeping up with your rates you could undercharge and lose money,” says Nick Holsinger, with EquipmentWatch.
Knowing that the rates you are charging accurately reflect your costs is especially critical in the current inflationary environment. “We talk to big contractors who haven’t updated their rates in 10 years, despite huge changes in costs, such as fuel,” Holsinger says.
Ames’s company historically sets rates every 2-3 years. “Now we’re looking at it almost on a monthly basis,” he says. Rising prices have “driven us to rethink our processes on a more demanding schedule. We have recently developed more sophisticated tools where a data analyst monitors cost. These new tools and monitoring allow us to adjust our internal equipment rates much quicker,” he says. SEMA is largely in the DOT market, “so the established contractual fuel escalation terms do not cover the actual cost.” On the private side, SEMA tries to negotiate and share with the owner the risk of fuel prices. “During these negotiations we develop a risk matrix showing the current price of fuel and including a specific trigger that would implement a method of payment,” Ames says. “Depending on the risk tolerance of the owner at times these conversations are not well received, however these pricing conditions are forcing us to have those conversations.”
Contractors who attempt to negotiate a fuel surcharge or rate increase should arm themselves with credible third-party data to show customers what they are up against, experts say. For instance, submitting an EquipmentWatch Internal Charge Rate PDF along with fuel receipts could be enough evidence to support a short-term increase in reimbursements, Holsinger says. And while no one wants to pay higher prices, “the alternative of having a contractor go out of business because of impossible costs or timing is likely to be worse for many project owners,” AGC’s Simonson says.
One immediate way to rein in your fuel costs is to get a handle on idling. If your operators typically let a machine idle while doing things outside the cab, encourage them to turn it off to save fuel by offering some type of incentive.
And since high fuel prices are likely to be around for the foreseeable future, when buying new equipment, make sure you do your homework to find machines that have the lowest cost of ownership, including fuel consumption. Also, consider renting versus buying. Renting can enable you to use the most fuel-efficient machine available and can also offer the chance to try out electric or alternative-fuel vehicles. Not sure if rental makes sense for your next job? This guide outlines the factors that go into this decision, including utilization, time on the project, and rental policies, and illustrates how they impact the rent versus owned decision for compact track loaders, backhoes, small- and mid-sized excavators, and wheel loaders.
Do you have machines that are underutilized? With the current shortage of used equipment, that idle machine just might command a premium price. “Equipment prices are higher than we’ve ever seen them,” says Ames, with equipment “temporarily becoming an appreciating asset.” Disposing of those machines might bring in needed cash to help you weather high fuel costs.
Longer-term ideas for affecting your fuel costs include adding fleet management software to monitor proper operating and maintenance practices, and transitioning to electric-powered vehicles if that makes sense for your location and job requirements.
For his part, SEMA’s Ames says tighter scrutiny of costs and keeping a sharp eye on price volatility are now part of the company’s processes. “We don’t see that changing a lot going forward,” he says. His advice: Implement procedures behind the scenes that enable your business to adapt to the changing market more quickly.
Tips to help your equipment sip – not guzzle – diesel
Small changes in how you operate diesel-powered machines and trucks can make a big difference in your fuel bill. Check out the following advice from the Diesel Technology Forum on how to save money on diesel fuel:
- Slow down. Your fuel consumption increases for every mile per hour you drive over 55 mph. (Each one-mile-per-hour increase in speed over 55 mph decreases fuel economy by 0.1 mpg.)
- Use cruise control. Advanced cruise control systems optimize engine and travel speed based on the load and can significantly boost efficiency.
- Operate in the highest possible gear. Doing so reduces engine RPMs and thus, fuel consumption.
- Stop idling. Idling burns about Âľ-gallon of diesel fuel per hour in a Class 8 truck. It also accelerates engine wear and tear.
- Plan your route. If possible, take a fuel-efficient route that bypasses construction delays. Consider driving at off-peak times to help avoid congestion.
- Maintain proper tire pressure. For every 10 psi a tire is under-inflated, trucks lose 1 percent of their fuel economy. Underinflated tires can also lead to tread wear and eventual tire failure.
- Perform preventive maintenance. Sticking to the manufacturer's recommended schedule for maintenance such as oil and air filter changes can help maximize fuel efficiency.
- Turn off accessories. If you don’t need them, shut them down.
- Right-size your equipment. Using an underpowered tractor or operating equipment at high RPMs and loads burns more fuel than using a larger machine.
- Upgrade your equipment. Newer machines are more fuel-efficient than older models.
- Use high-quality biodiesel fuels. Today’s diesel engines are compatible with blends of up to 20 percent high-quality renewable biodiesel fuels (and 80 percent regular petroleum diesel). These low-carbon diesel replacement fuels are available at a growing number of locations nationwide and can help reduce greenhouse gas and other emissions.