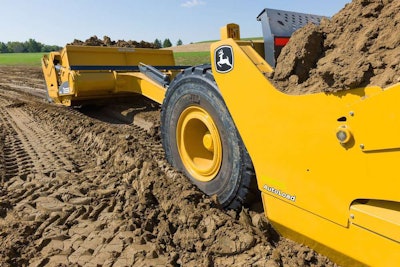
John Deere has made the most extensive changes to its scraper system since 2008, says Scott Bayless, scraper product consultant. “It’s the broadest lineup we’ve had since we started building scraper special tractors,” he says, “and we’re the only manufacturer that builds the entire system,” meaning both the tractors and the pull-behind scrapers.
The tractor and pull-behind scrapers offer a combination that can power through 90 percent of scraper applications, all while requiring a half of the labor and a third of the initial machine cost of self-propelled units, Bayless says. The result is a system, depending on the application, which can offer up to 50 cents per cubic yard savings over self-propelled scrapers, according to Bayless.
Carry-all scrapers, which dump their load much like a wheel loader, are typically used in loose, free-flowing materials. Ejectors, which push the loaded material out, are used in heavy clays and gumbos. Deere scrapers’ nomenclature for both types of scrapers indicates both capacity and width. For example, the 2112 has a 21-cubic-yard capacity and a 12-foot cutting width.
The tractor/pull-behind scraper set up, priced at around $700,000, has found its sweet spot in the geographical middle of the United States, working in residential site development and roadbuilding. “Customers are starting to look at them because they’ve gotten outbid on several jobs by people who use them,” Bayless says.
Tractors use Cummins, Deere power
With the Tier 4 Final models, Deere offers several upgrades to its tracked 9RT and wheeled 9R series scraper tractors, and has added its largest model to date, the 620-horsepower 9620R.
The 9620R, along with the 570-horsepower 9570R and 9570RT, features a Cummins QSX15 Tier 4 Final diesel. The remaining units in the seven-model line up, the 470-horsepower 9470R and 9470RT and the 520-horsepower 9520R and 9520RT use a John Deere PowerTech 13.5-liter Tier 4 Final engine.
Deere first offered a tracked scraper tractor in 2011. “We do things a bit differently, especially in how we attach the track frame to the tractor,” Bayless says. Deere uses a reaction arm bolted to the frame and affixed to the rear axle of the tractor, a configuration Bayless says gives a maintenance advantage. The mid rollers on the tracks are permanently mounted, instead of oscillating back and forth, which keeps the guide lug away from the track frame, leading to longer track life.
On the wheeled tractor side, a new HydraCushion front-axle suspension is designed to increase both performance and ride quality. With about 4 inches of travel, the HydraCushion really comes into play when loading. “When you take a high horsepower tractor with a high draft load, you typically get a lot of power hop,” Bayless says. “The only way to eliminate power hop is to raise the scraper or slow down, both productivity killers. HydraCushion eliminates the power hop and allows the tractor to put all the power to the ground. It also eliminates road lope during high speed transport.”
The wheelbase on the 9R tractors has been lengthened 17 inches. Deere increased the machine’s front frame strength by 10 percent; the rear frame assembly strength increased by 30 percent by using a structural rear axle, compared to the previous machine, which had the rear axle bolted to the main frame. “In this design, the rear axle is the rear structural member of the tractor,” Bayless says. A 400-gallon fuel tank, designed to take the machine through two shifts, is bolted on top of the structural rear axle.
Auto differential lock provides automatic traction to the 9R tractors, and keeps the differential lock engaged as long as the tractor is straight.
The scraper tractor line also includes Efficiency Manager, introduced earlier. This feature automatically adjusts and matches the engine and transmission performance to maintain ground speed with the lowest rpms, to reduce fuel consumption.
Ejector scrapers get significant revamp
On the scraper side, Deere’s ejectors received a significant revamp, including capacity upgrades from previous models. The 15-cubic-yard unit is now the 16-yard 1612DE; the former 18-cubic-yard model is now the 20-cubic-yard 2010DE (which also comes in a 14-foot-width 2014DE); and the 21-cubic-yard model increased to 24 cubic yards, now the 2412DE.
“The most noticeable change is the addition of a two-tire option on the 2010DE and 2412DE models,” Bayless says, which gives the units lower rolling resistance and drag when in mud. “It helps them pull through a lot easier,” he says. “You also don’t get as much mud packing between the tires as you do with four-tire set ups.” The downside of two-tire set ups is that they tend to duck walk, and do not offer as smooth as a grade as four-tire units.
The ejectors also have an integrated push block, Quik Attach Hitch and spill guard.
New carry-all options
A new bolt-on overflow spill guard is now available on the carry-all scrapers, raising the height of the spill sheet to keep material in the bucket, avoiding overflow on the tires, which creates excessive drag and carryback, slowing loading down and hindering production. The spill guard also increases the scraper capacity.
The carry-alls also have a new precision land leveling kit option, previously just available on the ejector units. “This allows these units to do both bulk material loading and precision land grading,” Bayless says. The kit includes an extended router, skid shoes and a flow dampening valve on the tongue of the scraper.
Cutting edges
Deere has also introduced interchangeable cutting edges that come in 16- and 20-inch lengths. “If you just have three segments over a 12-foot total length, each segment can be extremely heavy, and take two to three people to change,” Bayless says. “This way you can also mix and match them between tooth configurations.”
The router bit, which is the wear piece on the front end of the scraper designed to keep wear off the frame, has two sets of bolt holes, and “lower” and “replace” indications. When the bit is worn to the “lower” indicate line, it should be lowered to the second set of bolt holes; when the “replace” indicate line is reached, the bit should be changed.