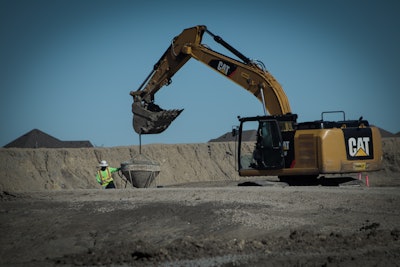
Equipment World
Its excavations resemble an inverted pyramid, descending down to 54 feet. They have to be designed by structural engineers, and trench safety plans are required.
Rey-Mar is among the elite companies building water, wastewater, and lift stations in the Fort Worth, Texas, area. With owners David Martinez, J.L. Rubio, and Oscar Martinez Jr. at the helm, the company primarily serves as a general contractor on public-funded projects.
The company was founded in 1991 by David and Oscar’s father, Oscar Martinez Sr., who was a subcontractor for concrete and general utility work.
David, after working for his father and with a water and wastewater construction company in Decatur, Texas, turned the company’s focus in 2012. At the time, leadership consisted of David, his father, and one of his uncles, and the company was still recovering from the Great Recession of 2008.
David credits his father with teaching him a strong work ethic, to not stop until the job is done. He later learned that there is more to life than work.
“That was the best thing my dad taught me and the worst thing he taught me,” David says, noting that he failed to balance work, personal and family time.
Other entrepreneurs, including his uncle, taught him that it's OK to relinquish responsibilities and that you need a team. That advice prompted him to bring his brother Oscar Jr. and longtime friend J.L. Rubio into the business.
“That's where this company really took off,” he says. “Introducing Rubio and Oscar and having the crews and the people that I hired years ago to grow with the company, instead of bringing in somebody new.”
Facing bidding wars and seeing the same engineers regularly, the leadership team developed a strong rapport with its customers.
"We must have a relationship with these entities that are going to call on us time and time again,” David says. “It says a lot about your consistency and ability to demonstrate that you’re a good contractor.”
To stand out, Rey-Mar ensures that it is always available for emergencies or to address a problem, even if it was caused by another contractor. The company has established a reputation solid enough that it can be selective about the projects it bids on.
“You don't want all the jobs; you just want the productive and profitable jobs. All the rest, everybody else can keep,” David says.
The team makeup of the company is something he recommends to up-and-coming contractors.
“When you're going to go do something as far as working or owning a company, you have to give it 100%,” David says. “You have to let people grow and take the reins, and when you do that, with the right tools and the right equipment, the proof is in the pudding.”
From 2014 to today, Rey-Mar Construction has grown from $1 million in annual revenue to $20 million. For that and more, they are one of 12 finalists for Equipment World's 2024 Contractor of the Year Award.
“We all work together as a team, and at the end of the day, it's a team working to push the company forward,” Rubio says.
That team spirit spreads to the field staff. On jobsites, Rey-Mar sets itself apart with crews that can be identified by the logos on their uniforms and the company’s equipment.
Rey-Mar Construction
All Cat
Any piece of heavy earthmoving equipment on a Rey-Mar site is a Caterpillar.
Oscar Sr.'s motto set the tone. He would say, "If you go to a job, you're driving a Ford. And if you're going to a jobsite and you want them to look at you in a different light, take Caterpillar equipment.”
It’s all about consistency, David says. “If you want consistency, have equipment that's not going to break."
Cat equipment, if maintained properly, will last a long time and yield a return on the investment at the end of its life, David stresses. In addition, with only one place to call and parts readily available with a distribution center nearby in Waco, Cat equipment simply makes sense.
For the company’s fleet manager, routine maintenance is kept on schedule via whiteboard and digitally. Any repairs beyond routine maintenance are typically done in the field by Rey-Mar's mechanics. If the mechanics are unable to complete the service, a Cat tech is called out, or the machine is sent in to the dealership.
“It just makes life so much easier,” David says. "The other thing is, if one of the Cat machines does break, it's because somebody did something wrong."
With all the equipment coming from Ford or Caterpillar, David tries to seek out the best deal he can. In the past, he would go to auctions, but he eventually realized that buying from a reputable dealer was easier than taking a chance buying equipment that may not have been maintained properly.
“If we're going to have it and we need it, we typically buy it and finance it through Cat Financial or buy it outright," David says. “You have to make the upfront investment if you want the benefit in production.”
Rey-Mar Construction
Safety First
With the inherent dangers of its deep, extensive excavations, all employees at Rey-Mar are well-versed in safety procedures.
Every day, the jobsite foremen pick a safety topic based on the work at the site. In addition, the safety parameters of the day’s work are reviewed to note any potential hazards.
“Everybody plays a role in safety,” Rubio says. “It’s zero tolerance as far as safety goes.”
Whether it is an employee with 10 years of experience or someone’s first day on the job, everyone is given full authority to speak up and call out if something appears unsafe.
“The mentality is we need to get these guys to the jobsite safely and home safely,” Rubio says.
Even with all the individual efforts, as with any construction company, accidents, most of which are preventable, do happen.
"If they do a good job, they're not only looking out for themselves but looking out for everyone else," David says. “I think that goes along with the camaraderie and that everybody gets along.”
Beyond the daily reviews and to maintain a level of competency in safety, Rey-Mary hosts biannual safety training sessions on a variety of topics and has implemented OSHA 10 training and certifications for employees.
In addition, management performs random checks to ensure workers are maintaining safe practices and are aware of proper procedures.
Rey-Mar Construction
From the Office to the Field
As with most construction companies, Rey-Mar faces the ongoing challenge of finding skilled workers. So they work hard to keep the ones they have.
"I think where we stand out and excel is that we take care of our guys," David says. “If you take care of your employees, your employees are going to take care of you."
All Rey-Mar employees get annual bonuses, and the top three supervisors and crew members are recognized annually.
"We don't like to promote any of it or to boast, but we like to show appreciation to the field staff because they're in and out of the holes, in the cold, the hot, and the rainy weather, and we see that because we were there,” Rubio says. “At the end of the day, we're pushing Rey-Mar into a better future so that a lot of people can feed off it.”
Rey-Mar strives to maintain and improve the communication between the office and field staff via weekly Tuesday morning production meetings.
“We've pushed to a point where our field has a strong voice,” Rubio says.
Proposed by Rubio, the meetings, which include management, superintendents, and project managers, allow better coordination with staff on projects.
A group text message among the project managers, superintendents, mechanics, and management is maintained to ensure constant communication throughout the company.
In addition, Rey-Mar has recently invested in Procore software to digitize more of the construction process and allow for faster distribution of plan changes, photo updates, staff, and equipment movement.
To accommodate these changes, iPhones and iPads are being distributed among the supervisory staff.
Looking Ahead
With a solid footing in the Dallas-Fort Worth area, the next step for Rey-Mar is branching out to different cities, such as Houston or Odessa.
"We're comfortable trying to pursue something there with the people we do business with here," David says. "So yes, the next step is branching out, buying more equipment, and dealing with the growing pains, but you have to have the right people, and that is the most difficult thing to do."